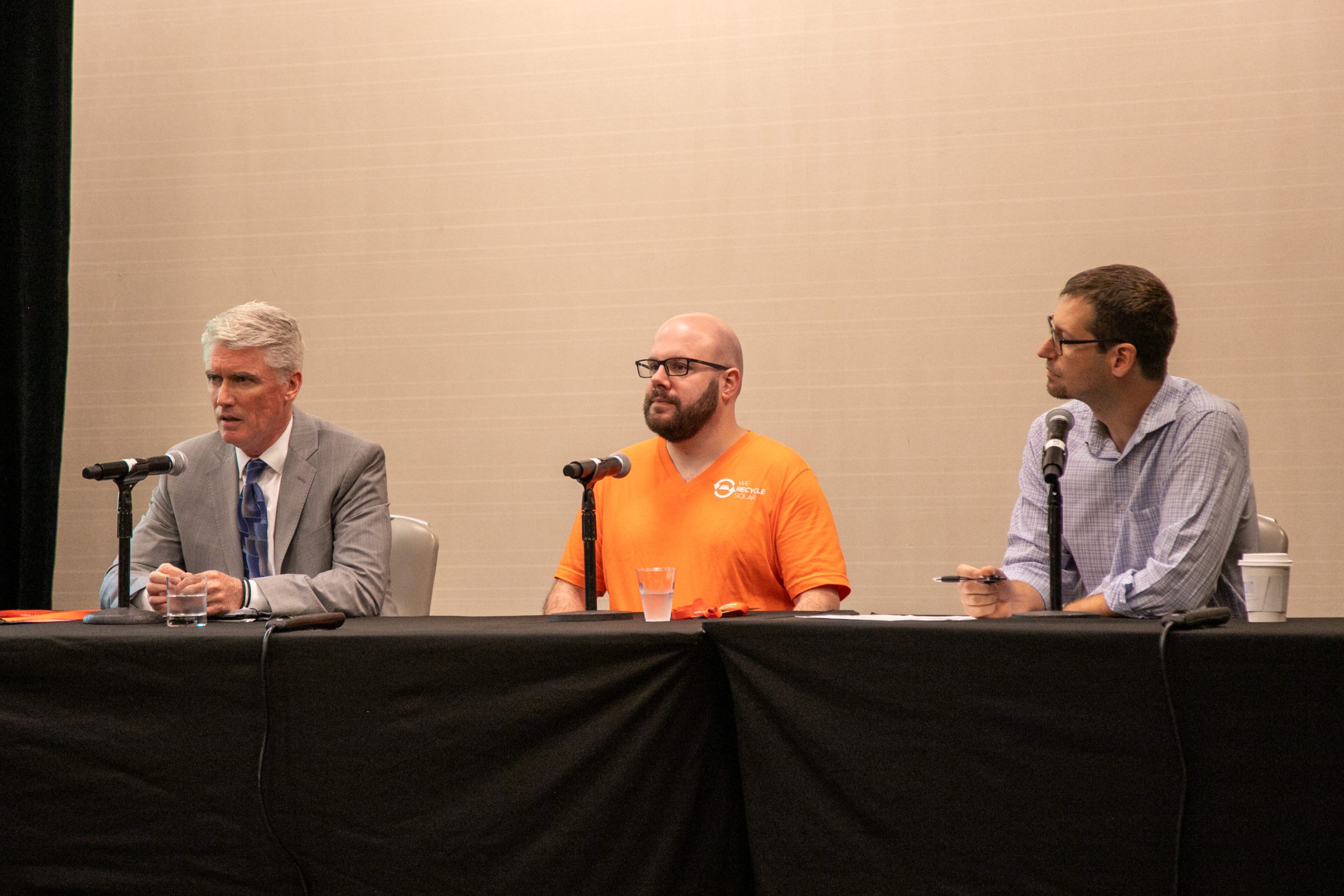
Bob Nicholson (left) and AJ Orben (middle) speak at the 2023 E-Scrap and E-Reuse Conference in New Orleans, with Jared Paben (right) moderating the session. | Big Wave Productions/E-Scrap News
Now is the time for interested parties to enter the solar panel recycling sector, but experts say there are plenty of challenges to navigate as well.
At the 2023 E-Scrap and E-Reuse Conference held in New Orleans, AJ Orben, vice president of We Recycle Solar, and Bob Nicholson, senior manager of photovoltaic recycling for the Solar Energy Industries Association, told attendees of the Sept. 20 session “Steps to Success in Solar Recovery” what to expect if trying to enter the field.
Jared Paben, associate editor of E-Scrap News, moderated the panel.
Nicholson said the solar industry is growing exponentially. The Solar Energy Industries Association (SEIA) represents 1,100 members from around the world in all aspects of the solar industry, and he noted that there’s a lot of attention on end of life right now.
That attention is being driven by local permitting authorities who want to hear end-of-life plans before they issue project permits and exert political pressure, Nicholson said. The scope often includes not just the panels themselves, but batteries, steel and site restoration.
At the beginning of 2023 there were approximately 375 million solar panels deployed in the U.S., Nicholson said, and approximately 7% (about 28 million) have been out in the field for 10 years or more. While that’s a small volume, he said he expects those numbers to double by 2030.
“From a future perspective, when you look at your business and you’re making decisions on whether or not to manage solar panels or recycle solar panels, the real growth is well in front of us,” he said.
Now is the time to make a plan and enter the sector, he said. Volume is low, but there are still panels coming off-line and some volumes available for recycling when panels get damaged during installation. Moreover, there are very few U.S. recyclers available to take them.
The conference session comes at a time when a number of e-scrap players have already entered – or are currently entering – the solar panel recycling business.
Powerhouse Recycling of North Carolina has launched a solar panel recycling affiliate, First America recently announced it’s entering the sector, Echo Environmental shreds and separates PV materials, and ERI has been sending shredded solar panel scrap to Redwood Materials for recycling.
More recently, COM2 Recycling Solutions told E-Scrap News it has begun accepting both intact solar panels and soon, just solar glass, to turn into frit product for tile manufacturing. So far, the e-scrap company, which has long processed CRT glass for use by ceramics manufacturers, has used a few thousand pounds of solar panel glass, in partnership with METech. It is running pilot programs for accepting glass only, with a tentative launch date of the beginning of 2024. I
Policy developments
In terms of policy, Nicholson said there are discussions happening at the federal level on whether to manage solar panels as universal waste. Currently, California is the only state that does so, and most states do not have landfill bans on solar panels.
“We do everything in our power to support the industry and get end-of-life panels into the recycling stream when we can, but things at the federal level are moving very slowly,” Nicholson said. “We don’t anticipate any movement on the universal waste rule for at least another 12 months.”
There has also been state-level discussion around extended producer responsibility for solar panels in California, and Washington state passed a solar panel EPR law in 2017, along with Niagara County, N.Y. in 2021.
Nicholson said SEIA’s position is that EPR is not the best method for handling solar panels. Commercial-level installations typically have decommissioning plans and funds built in, which takes care of that side, he noted.
As for residential installations, SEIA prefers an advanced recovery fee method, “where it’s really a cooperative effort between the community and the industry” and a recovery fee is paid up front, Nicholson said.
Orben of solar panel recycling company We Recycle Solar said it makes sense that California is considering regulating solar panels at their end of life, because most of the demand for solar is in California. He agreed that an advanced recovery fee method is a logical solution.
“From an individual consumer perspective, it’s such a small quantity per household, running somewhere between probably 10 and 40 panels,” Orben said. “In totality, it’s a massive issue, but there’s the consolidation element that you need to consider.”
The economics
Orben said the first thing to know about the economics of processing solar panels is “you’re going to be upside-down on recycling.” The majority of the value comes from the aluminum frame and the copper cables, he said, but 80% of the weight of a panel is glass that may or may not have traces of elements such as lead and cadmium.
“It’s really dependent on the actual panel that you’re processing, and again the hope is that you’re processing these in bulk in batch and that you have many of the same panel to do,” he said.
It can cost anywhere from $15.00 to $30.00 per panel to dismantle, shred, mill and separate out the materials, he said, with a return on average of between $2.00 and $4.00 in aluminum, copper, glass, lead, silver and tin.
“If we had to rely on recycling, we wouldn’t be in business because it is something that has to be subsidized by the customer,” Orben said.
Different panels from different manufacturers – and of different ages – all vary widely in what they may contain. For example, many panels produced in the 1990s used more silver, Orben said.
Historically, reuse and repair has provided the bulk of the revenue, Orben said. Last year, a government investigation into tariffs on imported panels briefly halted many imports, driving up the value of reused panels, but this year the issue was resolved. As a result, an influx of stockpiled imported panels drove the price of new, efficient panels far lower than used ones, reversing the market.
Orben noted that in the solar industry, prices are calculated as a cost per watt. Traditionally, a large-scale developer would pay between 25 cents per watt and 40 cents per watt for new panels, but now the cost is only 13 cents per watt.
“If you can buy a brand new panel with two times the efficiency and a full 30-year warranty for 13 cents a watt, why would you purchase a used panel with no manufacturer warranty for, say, 5 cents a watt?” Orben said. “In the last several months, the resale market has started to take a significant hit. Again, not to say that you can’t make some money in that way on a smaller scale, but long-term viability right now is really a question.”
There is also some money to be made in providing repair parts for older panels, but Orben said the cost and space to store those replacement parts can be prohibitive.
“You’re talking about assets that each weigh somewhere between 40 and 70 pounds and take up a much larger footprint” than laptop repair parts, he said. “The cost of storage is a huge issue.”
Meeting the challenges
Nicholson said there’s research going into more efficient ways to process the panels, and he’s having plenty of conversations with manufacturers about designing for recyclability.
“They’re trying to build equipment that needs to sit outside for three to four decades, so that has to be some pretty robust equipment,” he said. “It’s a delicate balance between the lifetime of the panel and then the ability to easily separate those materials.”
Industry standards would also help, both panelists said. Nicholson noted that SEIA will likely develop some, and is also pushing for solar to be included in other certification systems. Sustainable Electronics Recycling International (SERI) is currently working to add solar panels to its R2v3 standard.
Orben noted that another big challenge is logistics, because there are a small number of recyclers across the country and solar panels are bulky and difficult to transport, all of which drives up cost.
“They’re not laptops, they’re not cell phones. You can’t ship them with the post office,” he said. “You can’t throw them on pallets and fit 1,000 phones per pallet. This is something where, at best, you’ll probably get 500 to 600 on a truck. They also take up quite a bit of warehousing space, so processing is pretty paramount to make sure that you’re not spending money on storage.”
Nicholson added that another challenge to overcome is finding end markets for the glass especially.
“Eighty percent of the weight of a solar panel is glass, and finding homes for that glass can be challenging and there aren’t a lot of markets to make a return on the glass,” he said. “I can say that there are a number of organizations and universities working on research plans and programs to address those issues, but I think we’re still a year or two away from having any solid answers and improving that market.”
We Recycle Solar is also investing internally on research into leaching to better clean glass, Orben added. Right now, it can clean some manufacturer’s glass well enough to be used for other purposes, such as sandblasting, but “it’s not something that we’re capable of doing with all of them at this time.”