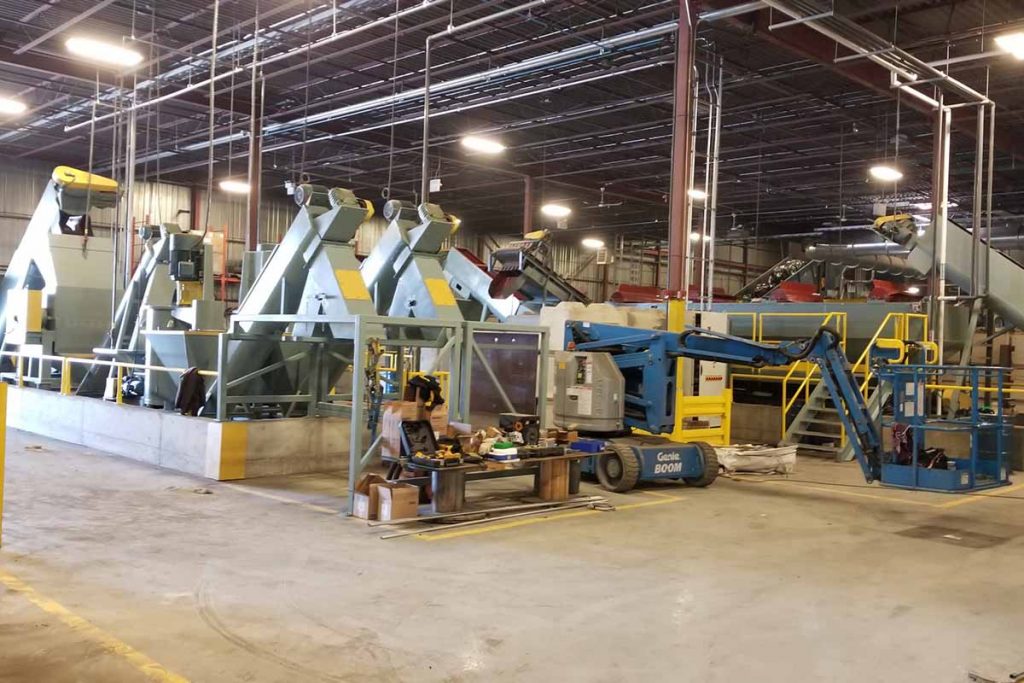
A view of the recently installed e-plastics sorting and washing line at eCycle Solutions. | Courtesy of eCycle Solutions
A major North American e-scrap company has invested approximately $1.5 million into a plastics cleanup line, partly to get ahead of tighter international rules on plastics exports.
Ontario-based eCycle Solutions installed and expects to begin full-scale use of the float-sink tank and related equipment this week. The system will remove contamination from the shredded e-plastics stream and recover valuable metals currently being lost in outbound plastics shipments.
The investment demonstrates “our commitment to the circular economy and providing our customers and the electronics recycling industry with closed-loop solutions for e-plastics,” said Scott Loughran, vice president of operations at eCycle Solutions.
He also noted the plan will create jobs and help the recycling sector adjust to a “changing global legislative landscape,” specifically updates to an international waste treaty that are expected to take effect next year and impose additional requirements on the movement of scrap plastics
The company isn’t alone in citing overseas scrap import laws as one reason for investing in domestic systems to process polymers from end-of-life electronics. Last year, Sims Recycling Solutions (now called Sims Lifecycle Services) installed a similar e-plastics cleanup system at its La Vergne, Tenn. facility. Sims leaders cited unreliable export markets as an impetus for the investment.
How the line works
Headquartered in Mississauga, a suburb of Toronto, eCycle Solutions has locations in the provinces of Alberta, British Columbia, Ontario and Quebec.
At the company’s headquarters it operates a shredding and separation line that it purchased from Sims Lifecycle Services when Sims shut down large-scale shredding operations at its Roseville, Calif. plant, Loughran said.
In addition to ferrous and nonferrous separation equipment, the shredding system includes an optical sorter to eject e-plastics from printed circuit board scrap. But Loughran noted the composition of the end-of-life electronics stream is evolving, with more plastics and fewer metals. As a result, it’s become more difficult to keep plastics out of the metal concentrate sold to refineries, he said. That’s an economic problem, because refineries don’t pay for the plastic weight but eCycle Solutions still pays freight charges for it.
Meanwhile, some metals are inevitably ejected by the optical sorter in the e-plastics stream. The company is having to run plastics through the optical sorter a couple of times to reduce the metals content, Loughran said. That presents a processing bottleneck.
The new system, which takes up about 15,000 square feet at the Mississauga facility, includes float-sink, washing and drying equipment. The company will run the optical sorters’ ejected and non-ejected fractions through the system.
In the float-sink tank, metals and other “heavies” will sink to the bottom, while the desired polymers will float. A variety of salts are used to increase the water’s density so that the styrene-based polymers HIPS, ABS and PS and the polyolefins PP and PE will all float, but non-target polymers such as PC and POM will sink. In unmodified water, the targeted styrene polymers would also sink. The company can regularly adjust the density, depending on the desired sorts.
The floating plastics will be size-reduced to 8 to 10 millimeters, washed and dried. The sinking fraction will be washed before the metals are sold.
The float-sink equipment has a capacity of about 20 metric tons per hour, and washing and drying equipment can handle up to 8 metric tons per hour. Loughran said eCycle Solutions won’t use anywhere near the full capacity with its internally generated plastics. The system will allow room for internal growth, and it’ll allow eCycle Solutions to sort and clean e-plastics as a service for other e-scrap companies, he said.
The company expects to add three staff positions on one shift to operate the line.
The benefits it brings
Loughran explained that the system will bring a number of advantages for eCycle Solutions.
Having the metals-plastics separation capability means the company won’t have to re-run plastics through the optical sorter to remove metals, allowing it to turn up the volume on the shredding system, he said. It will also reduce the plastics content of the printed circuit board shipments.
Having the system also helps eCycle Solutions adapt to a changing global legislative landscape, Loughran noted. In May 2019, countries that are parties to the Basel Convention on the Control of Transboundary Movements of Hazardous Wastes and Their Disposal voted to place new restrictions on the scrap plastics trade. At the 2020 Plastics Recycling Conference and Trade Show, the convention’s top staffer explained exporters should expect much more stringent controls on scrap plastics shipments.
Loughran noted how China’s National Sword campaign cut off e-plastic downstreams for his company and other North American processors, leaving companies sitting on e-plastics for a while before Southeast Asian outlets opened and they were able to move them again.
“That’s something that we definitely don’t want to contend with in the future, particularly with the Basel Amendment that’ll take effect in 2021,” he said.
Loughran’s company plans to continue sending its e-plastics to a partner company in Malaysia, he said. That company, which he declined to name without their permission, uses electrostatic separation equipment to further sort the mix of plastics by polymer type, including separating PS from ABS, for example. The plastics will be pelletized and sold.
Loughran said after talking with both Canadian and Malaysian consultants about the impact of the Basel amendment, eCycle Solutions doesn’t anticipate problems shipping to Malaysia as long as there’s consent from both governments. Malaysia’s concern is metals contamination in the plastics, but if it’s clean, Loughran said he doesn’t anticipate problems.
In general, having cleaner plastics will de-risk the company’s plastics chain by opening up downstream options.
“Giving us a cleaner product will allow us to access other markets,” he said.
A version of this story appeared in E-Scrap News on June 25.
More stories about e-plastics
- E-plastics processor expands line of recycled board
- 3R Technology working on first US e-plastics site
- Authors address error in black plastic additive study