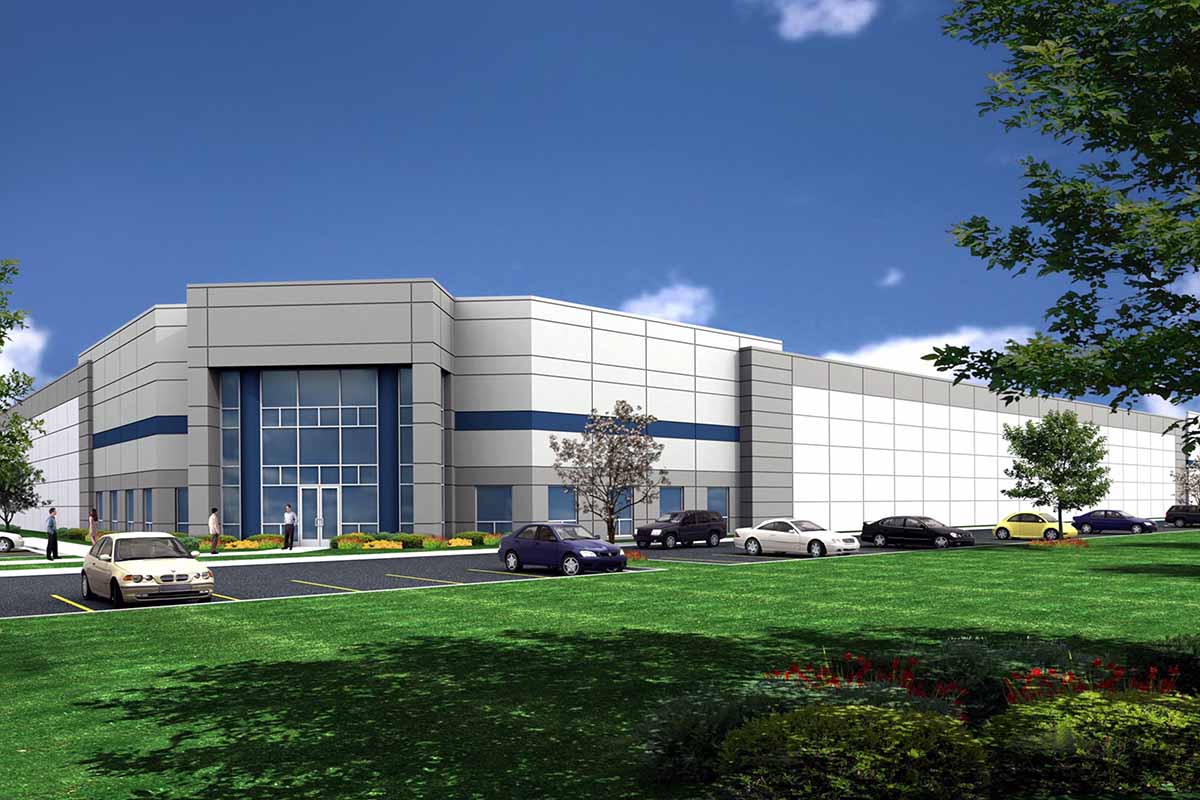
Rendering of the planned “SuperPRF” courtesy of International Recycling Group.
International Recycling Group hopes to finish financing a $150 million plastics recovery facility by the end of the year, with the massive plant scheduled to come on-line in 2023.
Mitch Hecht, founder and chairman of Erie, Pa.-based International Recycling Group (IRG), recently provided Plastics Recycling Update with an update on the company’s “SuperPRF” project, first announced last summer.
The plastics recovery facility (PRF), to be located in Erie, will bring in hundreds of millions of pounds of mixed plastics per year. At full production, within five years, the plant is expected to process about 500 million pounds of material. An automated system will sort out PET, HDPE and PP polymers that will be processed on-site into washed flakes. The remaining plastics will be processed into an iron-reducing fuel agent to replace coal in steelmaking processes.
Eventually, the PRF’s scrap appetite will be met by a sister company using a gig-economy model to collect plastics from homes and businesses, side-stepping traditional haulers and materials recovery facilities (MRFs), according to Hecht. He sees that approach as recovering more scrap plastic than today’s curbside collection systems can.
“That is the future of plastic curbside collection,” he said.
Financing a $150M project
Hecht said IRG has a contract to buy a 26-acre parcel in Erie that was a former International Paper site. Next month, IRG will begin the permitting process. RRT Design and Construction has been hired to handle design, engineering and project management.
The project is currently estimated to cost about $150 million, Hecht said. The plan is to pursue about $50 million in equity investments from impact investment funds and strategic partners, he said. IRG can finance the remaining $100 million with either tax-advantaged bonds or bank loans that could be guaranteed through environmentally advantageous loan programs, he said.
Hecht said he thinks ample impact investment and infrastructure funding is sitting on the sidelines waiting for good green-tech projects.
“There’s enormous demand in post-consumer resin, and investors who understand the industry realize that there’s really enormous tailwinds towards having a large-scale regional sorting facility, or PRF,” he said.
So far, IRG has received a combined $9 million commitment from the founding members of injection-molding company Plastek Group, which would use recycled PP flakes produced by IRG’s plant, and Erie Insurance, which established a $50 million fund to spur economic development in economically distressed parts of the Rust Belt city.
A number of other plastics recovery facilities (PRFs) have failed in recent years, including those owned by QRS Recycling and Titus MRF Services. Hecht said one of the advantages his company enjoys is its steelmaking additive, called “Clean Red,” which allows IRG to find value in “everything but the squeal,” a hog-farming expression that means wasting none of the animal.
“The name of the game is yield loss. You need to minimize your yield loss,” Hecht said. “The beauty of our model is we have a non-landfill, not-tip-fee home for absolutely every pound of plastic that comes in the door.”
Hecht said that if IRG can close on financing by the end of 2021, the company can break ground during the first quarter of 2021, with commissioning expected in mid-2023.
The project has been criticized by local activists, including the local Sierra Club chapter, who circulated a list of pointed questions to local leaders in March.
Hecht insisted the letter includes nine inaccurate or misleading statements about the project and recycling in general. “The letter does not even accurately reflect the national Sierra Club’s position on recycling, which is that all three ‘Rs’ – reduce, reuse and recycle – are essential to the fight against pollution,” he said.
Side-stepping traditional collection
Hecht and his associates plan to launch a separate sister company, called New Bin, to collect material for the plant directly from generators.
The existing curbside system has suffered from the chicken-and-egg conundrum, Hecht explained: Processors aren’t creating markets for many post-consumer mixed plastics because haulers aren’t collecting them, but haulers aren’t producing those bales because viable markets are lacking, he said.
Using an Uber-like gig-economy model, New Bin will rely on individuals with pickup trucks earning extra money by fulfilling app-based requests to collect recyclables from homes and businesses. They’ll bring material to New Bin collection sites, where material will be aggregated and shipped to Erie either loose or baled. For the technology, IRG signed an agreement with the Dubai-based developers of the ZeLoop app.
Hecht said he expects the collection strategy to particularly grow in states without deposit programs and in communities where recycling programs have been cut back or discontinued. He sees the strategy as accessing the majority of plastic that never lands in a recycling bin.
“Our vision is that we really need to break the log jam in available supply of recycled materials,” he said, “and the best way to do that is to go direct to the plastic generators.”
New Bin will be piloted starting in late summer or early fall 2021, Hecht said. It will be financed as a separate tech company, relying initially on crowd funding and then likely venture capital funding, he said. He expects that, within three years, New Bin will supply 100% of the scrap entering the Erie plant.
Until then, IRG will be buying baled plastics Nos. 1-7 and 3-7 from MRFs, he said.
Hecht previously worked on Wall Street, mostly covering the metals and mining industries as managing director of investment banking for Deutsche Bank and PaineWebber. Later, he became chief financial officer for International Steel Group, a startup that grew within a year to become the second largest integrated steel producer in North America.
“I have a window on how you can transform an old legacy industry and make it profitable,” he said, “and that’s exactly what we’re hoping to do with the current recycling industry.”
More stories about processors
- Major plastic initiative sets sights on system change
- California will fund mixed plastics facility, other projects
- E-plastics processor expands line of recycled board