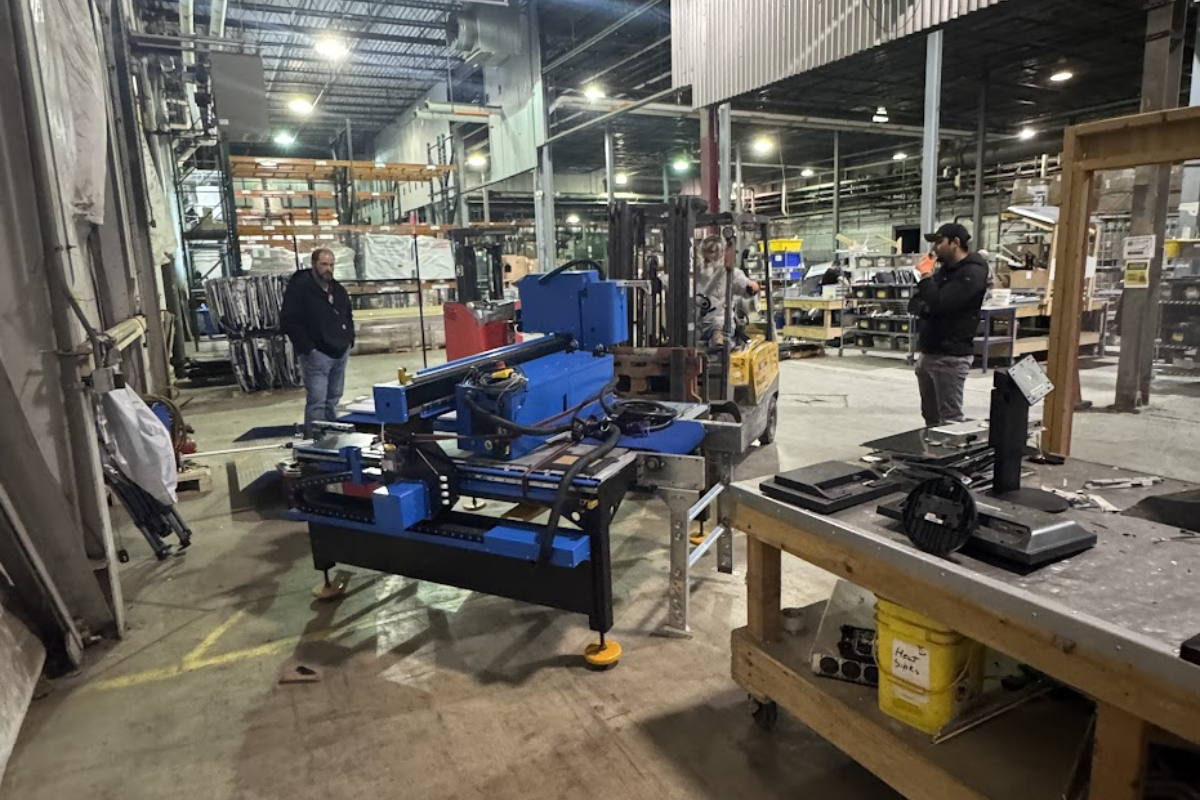
RoboLoop is a venture from Matt Travers, a senior systems scientist at Carnegie Mellon University, Ned Eldridge, CEO and founder of eLoop, and Scott Thayer, CEO and founder of Automap. | Courtesy of RoboLoop
A startup company is applying expertise from eLoop, Carnegie Mellon University and a past Apple partnership to speed up disassembly of flat-panel displays.
The company, roboLoop, is a collaboration between Matt Travers, a senior systems scientist at Carnegie Mellon University, Ned Eldridge, CEO and founder of eLoop, and Scott Thayer, CEO and founder of Automap.
Eldridge told E-Scrap News that during the COVID-19 pandemic, eLoop started to investigate ways to make its State College operation in Pennsylvania more efficient and profitable, and landed on robotics. He met Travers after first working with an Irish company, and “once we found that we had a little common thread there of robotics, Matt and I started putting our heads together about different things that might work in the industry.”
The outcome is a robot that uses largely off-the-shelf parts to keep costs down and improve build time, which sits at about three months. The focus now is on locating and removing screws from the backs of the flat-panel displays, one of the most time-consuming parts for human employees. In the future, the creators hope to remove internal screws and recover rare materials using the robots.
Travers, who works at the School of Computer Science’s Robotics Institute, said instead of unscrewing each screw, the robot “punches” it out using a modified pneumatic nail gun.
The robot uses AI to identify the brand of flat panel display and therefore know where the screws on each one are. The AI portion draws inspiration from Travers’ work with Apple; his partnership with the OEM launched six years ago and focused on developing machine learning models to enable robots to learn how to disassemble an unfamiliar device.
However, Apple does not produce very many monitor displays, Travers said, “which is why we’re just taking inspiration” from that shared work.
A first-version model is installed at a facility in State College that used to be owned by eLoop. Travers is working on new robot iterations that are four to five times faster.
It takes about 15 minutes for a human being to go through and break down a panel, Travers said, and the “sweet spot starts to happen anywhere under 10 minutes.” Once that time drops to 8 minutes per unit, the financial projections start to improve. Travers said roboLoop has financial targets tied to five-, three- and two-minute times.
RoboLoop is currently processing 200,000 pounds a month, Eldridge said, but in June the company expects that to increase to 500,000 pounds per month as the second robot comes online. In total for 2025, the company expects to process a total of 4.2 million pounds, with feedstock coming from partner companies, he noted.
Part of the appeal of automation, Travers added, is not just moving 80% faster than humans but maintaining that speed and accuracy over longer periods of time.
“At the end of an 8-hour shift, a robot can maintain speed and accuracy. It does not get tired or need a break,” he said. Automation also frees human employees up to take more interesting jobs than running a screw gun, Eldridge said, because “the people who work here like to be around the technology.”
Eventually, automation could also allow the e-scrap industry to move away from shredding as a first step: Shredding lowers labor costs and speeds up processing but also makes the recovery of specific metals difficult due to contamination, Eldridge said.
Cleaner and faster device breakdown means more optimized feedstocks moving to downstream partners, Eldridge added, and he sees flat-panel displays as a sector with high growth potential.
“You can only imagine how many of them are actually being recycled each year,” he said. “They have a very short lifespan, and innovation plays a part in that, because people like cool things. And if something cool comes out, they’re going to take that TV off the wall and put it in the bedroom and take the one in the bedroom and throw it in the trash. Someone has to be out there scooping them up and recycling them.”
Several states near roboLoop’s current facility have extended producer responsibility laws for e-scrap, Eldridge said, meaning a robust collection system is already in place.
“From my research, you have approximately 200 million pounds of TVs that will come out of that network, just including all states contiguous to Pennsylvania and 300-mile radius from State College,” Eldridge said. “These are good sized metropolitan areas, roughly 21.7% of the nation’s population’s right in that groove, so we’re hoping that we’re going to be successful in attracting and recycling a lot of flat panels.”
Eldridge anticipates needing to build several more robots but said it will “put us in a position where we are taking advantage of technology to make this a profitable venture.”
There’s also the potential to expand the technology into identifying and recovering different materials, such as e-plastics, which opens up another potential revenue stream as changes to the Basel Convention alter where those materials can go, Eldridge noted.
Travers’ short-term goal is to get both robots up and running so he can collect data and make more improvements. In the future, roboLoop is considering licensing out the technology and expanding what material streams the robots target.
“I’m a robot guy at the end of the day,” Travers said. “The magic has to happen downstream,” at the partner recycling companies.
Eldridge said with so many opportunities, the trick now is to stay focused and grounded.
“Matt’s mind never stops designing,” he said.”There are so many ways we can go with it.”