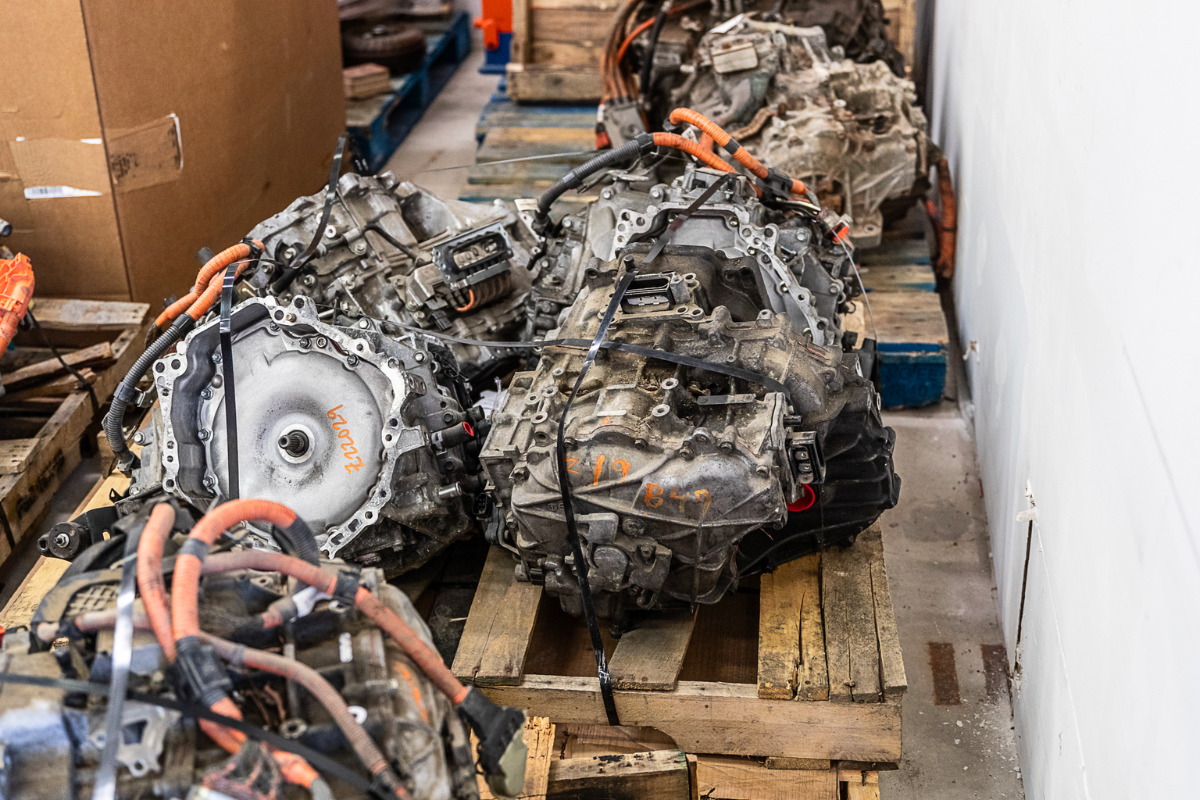
Cyclic Materials is looking to expand the capabilities of its two technologies to recycle magnets. | Courtesy Cyclic Materials
Ontario-headquartered Cyclic Materials is actively sourcing hard disks from ITAD firms for its magnet extraction and rare earth processing operations. The company is planning to expand with multiple facilities in the U.S. and Canada in the coming years.
The Kingston, Ontario-based company brings in end-of-life hard drives and a variety of other magnet-containing products, extracts the magnets and uses a hydrometallurgical process to convert them into mixed rare earth oxides and other substances.
“That mixed rare earth oxide is the raw material that you would need to make a magnet again and put it back into the economy for different applications,” said Ahmad Ghahreman, CEO of Cyclic Materials, in an interview with E-Scrap News.
Cyclic’s first facility, commissioned in September 2023, is capable of processing about 2,200 pounds of devices per hour, or nearly 18 million pounds per year, using the magnet removal process the company calls Mag-Xtract. The company’s separate hydrometallurgical process, which completed a trial run in 2022, has an early capacity of 22,000 pounds per year.
“Our next step is to scale up both technologies to the next level, in the next one year,” Ghahreman said. Cyclic anticipates starting up a commercial demonstration plant for the hydrometallurgical process in the second quarter of 2024. Ghahreman estimates Cyclic will develop five or six locations in the U.S. and Canada, where the Mag-Xtract equipment will be deployed. He anticipates the company will operate one large hub where the hydrometallurgical process will be centralized.
Ghahreman launched Cyclic in 2021, and the company has since raised $33 million (U.S. dollars) in funding, largely from private investment and venture funds, with about $3 million from Sustainable Technology Development Canada, a Canadian government agency. Its advisory team currently includes Adam Shine, CEO of e-scrap processor Sunnking, as well as multiple current and former executives at battery recycling firm Li-Cycle.
Magnets processed into multiple streams
Besides hard drives, Cyclic’s input stream includes a range of electric motors, particularly those sourced from electric vehicles and traditional automobiles. These are valuable to the company for their size and rare earth concentration. Cyclic isn’t currently focusing on smaller devices, like smartphones, due to the lesser magnet material quantity and therefore lesser dollar value.
As a hard disk enters the Mag-Xtract process, Cyclic’s proprietary equipment removes the magnet and generates multiple output streams, Ghahreman explained. Typically, this includes the scrap metals from the device, such as copper, aluminum and steel, and the magnet. The scrap commodities are sold to metals buyers and the extracted magnets can be sent for processing using Cyclic’s hydrometallurgical technology.
This process refines the extracted magnets into multiple streams: Mixed rare earth oxide, cobalt-nickel hydroxide and other mineral byproducts. These substances will be sold to a variety of customers including OEMs making hard drives and other producers of magnet-bearing products. The company is also selling the resulting substances to chemical companies – one early customer is chemicals giant Solvay – that can use those feedstocks in chemical products.
Geo-political backdrop
Rare earth recovery has been a growing area of interest in North America and has drawn attention from the highest levels of government. That’s largely because the vast majority of rare earth elements for manufacturing are supplied by China, which in 2019 threatened to cut off exports to the U.S. due to trade tensions between the two nations.
“They’re attached to some geopolitical challenges,” Ghahreman said of the rare earth materials. And at the same time, they’re likely to grow in importance: Ghahreman noted a lot of the applications of rare earth magnets are relevant to the clean energy transition, including in wind turbines, electric vehicles and more.
“Those metals are critical for our electrified society,” Ghahreman said.
The U.S. Department of Commerce under the Trump Administration in 2018 deemed rare earth elements to be critical materials that the U.S. should increase its domestic supply of, and in 2020 the U.S. Department of Defense provided $28 million in funding to a Texas-based rare earth recycling operation. The Biden Administration has continued to emphasize the importance of rare earth recovery from hard drives, issuing a report in 2021 that called for federal support for new technologies that recover target materials from end-of-life electronics.
The Canadian government has a similar interest in rare earth recovery. The government’s Critical Minerals Strategy identifies rare earth elements as one of six priority materials that are needed as inputs for priority supply chains. When Sustainable Technology Development Canada issued grant funding to Cyclic in early 2023, the agency highlighted the company’s focus on recovering “rare earth elements from magnetic waste, reducing landfill and boosting the domestic supply of these essential elements.”