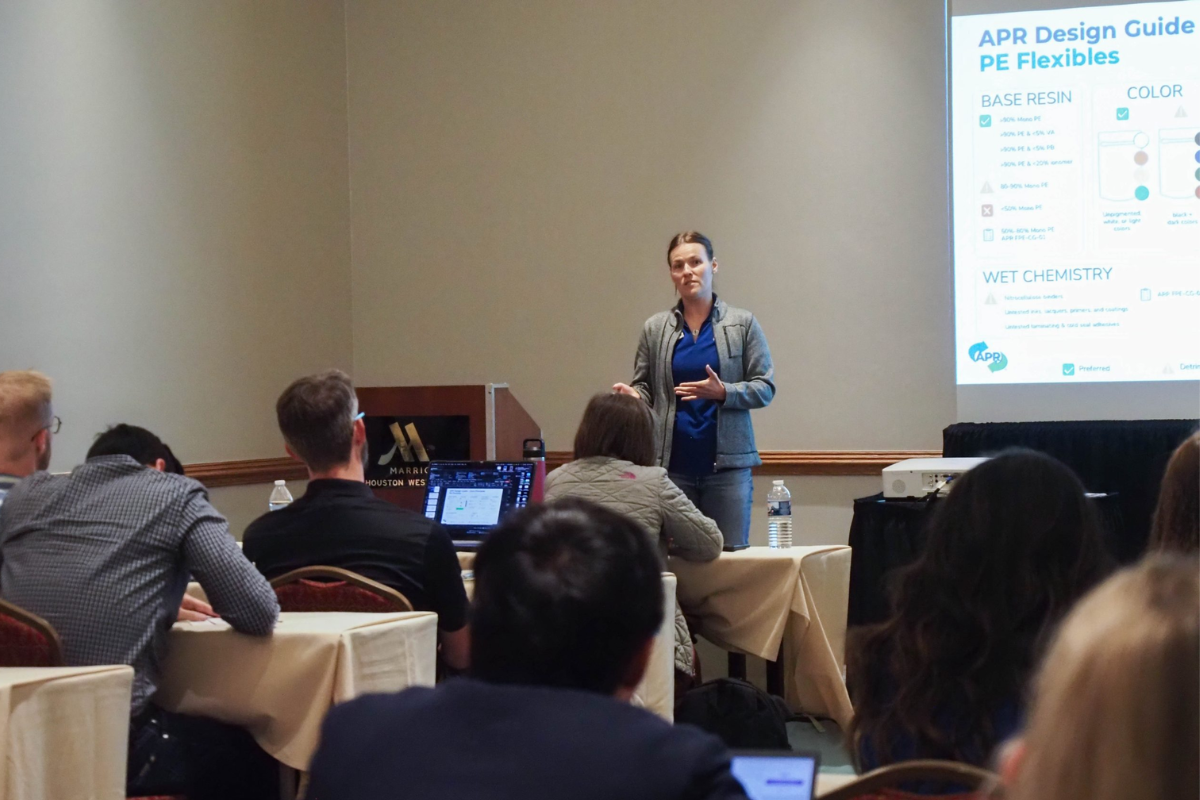
Rebecca Mick, program director of film and packaging innovation for APR, presented design guidance at a recent training session. | Tan Sackett/APR
Industry leaders and packaging design engineers explored the challenges to recycling film and flexible plastics during an inaugural packaging design training session recently in Houston.
The Association of Plastic Recyclers conducted the training on April 29. APR owns Resource Recycling, Inc., publisher of Plastics Recycling Update.
Film and flexible packaging, or FFP, encompasses a broad array of materials, from PE pallet wrap to multi-material pouches that may include metallic layers. This complexity adds to the difficulty in identifying viable and cost-effective recycling solutions with sustainable end markets, according to a 2024 report prepared by consultant Eunomia for APR.
The training session featured highlights from the report, “How to Scale the Recycling of Flexible Film Packaging,” which explores the economic case for using pyrolysis to help increase processing of polyolefin FFP collected from households, and ultimately to incentivize MRFs to collect plastic film.
Pyrolysis is a form of chemical recycling that uses high heat and pressure to break apart chemical bonds in plastic to create pyrolysis oil, which can then be used in place of virgin fossil fuel either to create plastics or in other applications.
Processing hurdles are many and varied
The most problematic contaminant is paper labels, said Curt Cozart, chief operating officer at APR, who led the training session. Paper impacts the quality of recycled film by causing higher incidences of tiny imperfections called gels, enhancing undesirable odors and affecting color of the final product. Although polymer labels are available, they increase costs for source materials.
Collection of post-use plastic film presents a challenge, with many MRFs unable to accept the material because it quickly tangles in sorting equipment. This endangers workers tasked with resolving the snags and leads to costly equipment downtime.
In addition, post-use film is among the lower-value recycled commodities. Since 2018, B-grade film bales — typically consisting of about 80% film — have averaged 2-8 cents per pound. And during that time C-grade bales, also known as MRF bales, have been no higher than 2 cents per pound, according to historical pricing data from RecyclingMarkets.net. With trucking costs typically running about 3-5 cents per pound, transportation from collection point to processor can easily turn margins negative for film recycling, even before secondary sorting costs are factored in.
In comparison, PET bales have been as high as 39.56 cents, in May 2022, and HDPE natural bales hit a record high of 108.44 cents in April 2025.
Despite the challenges, WM-owned Natura PCR as well as Nova Chemicals feature mechanical recycling for LDPE and LLDPE films. Both tend to focus on A-grade film bales, which typically consist of 95-99% clear film, and Natura and Nova each have received no-objection letters from the U.S. Food and Drug Administration for food-grade applications for LLDPE.
The training included a tour of a new facility at Natura PCR’s site in Waller, Texas, northwest of Houston.
Plastic film also has been the subject of local or state bans. While well-intentioned, such bans can have unintended consequences, according to a study at the University of California-Riverside and an industry-backed report. Before California voted to expand its ban on plastic bags, an industry coalition lobbied against it, arguing that paper bags consume more water and energy to produce and that a ban would harm the state’s recycling industry.
One alternative to bans that the industry has suggested is behavior-focused campaigns to reduce use of plastic bags. A pilot project by an industry-led group found that when retail stores encouraged consumers to bring their own bags or opt out of using one, nearly 5% fewer single-use plastic bags were used.
Chemical recycling as an end use
Although it seems to be emerging as a key outlet for films and flexible packaging and a complement to mechanical recycling, the nascent chemical recycling industry itself has struggled to find footing. The most common method, pyrolysis, can break down multilayer packaging into a reusable feedstock, but such projects are costly and as such must target large volumes of inexpensive feedstocks to ensure profitability.
By 2030, the residential FFP stream is expected to grow to about 7.1 million tons, according to the Eunomia study. Of those volumes, 5.6 million tons could be available for pyrolysis, the report estimates, with about 40% of those available volumes becoming suitable as the result of packaging design adapted for recyclability, using techniques such as those detailed in the APR training.
US, Canadian approaches differ
Elena Mantagaris, senior advisor for Canadian initiatives at APR, noted during the training session that Canada has taken a different approach to extended producer responsibility legislation for packaging than in the United States.
In several new provincial EPR programs taking effect this year, Canada approaches residential recycling by collecting a wide variety of consumer packaging materials and figuring out what to do with it later, in a consumer-driven approach, Mantagaris said.
In contrast, the U.S. tends to build recycling infrastructure based on existing end markets, as evidenced by the predominance of rigid plastics recycling, and works to get consumers to adapt their behavior to the established structure, said APR’s Cozart. He added that introducing money into the system could incentivize development of a mono-material approach.
In general, however, there’s only so much consumer education that can yield net positive results, Mantagaris said, adding that some nuances are too complex for consumers to understand, such as polymer type, additives and so on. “So just put it in the box and let us sort it out,” she said of Canada’s approach.
In addition, a 2024 study found flexible materials account for 47% of the plastic packaging put into the Canadian market.
About 40 people attended the inaugural event. APR has long provided packaging design training but only recently introduced the film and flexibles track.