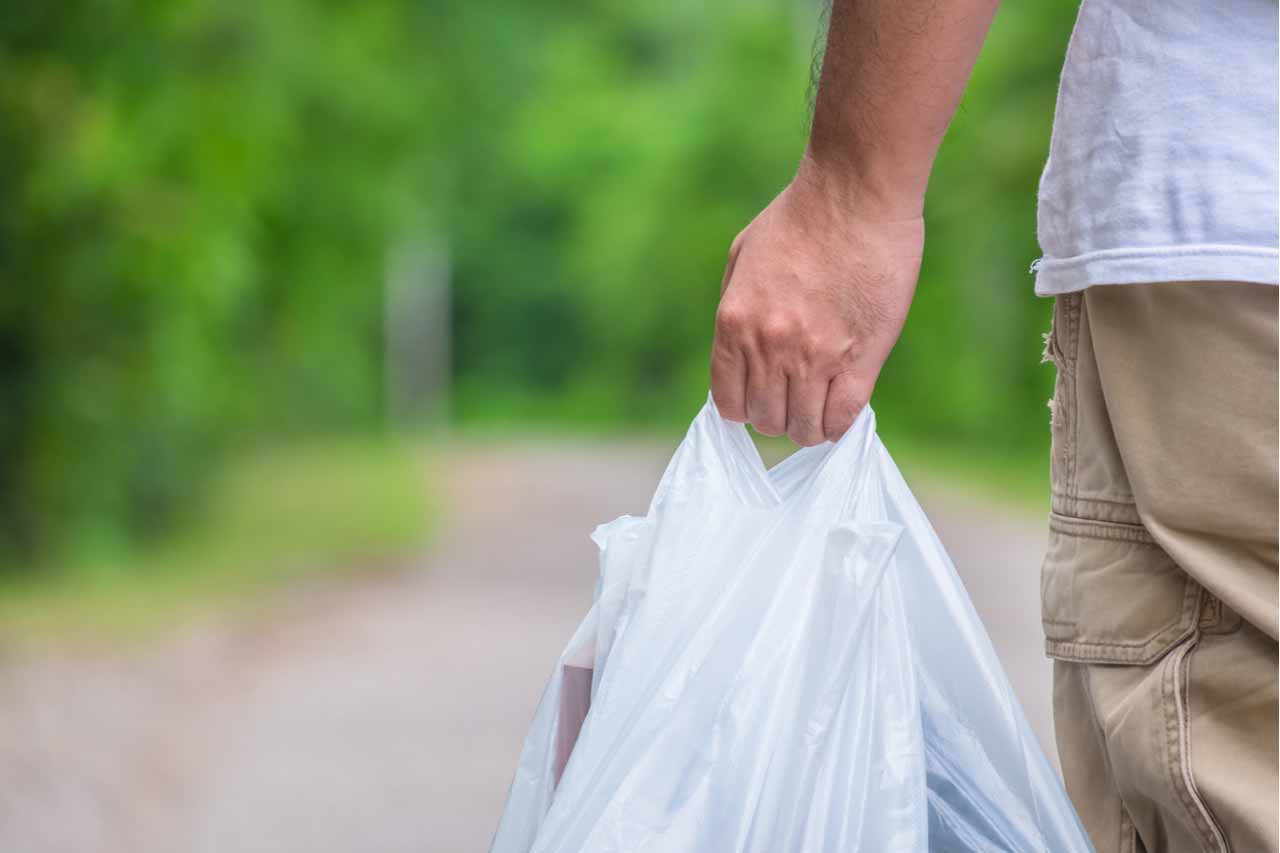
A group of Canadian packaging stakeholders are exploring ways to optimize the recycling system for flexible plastics. | Patpitchaya
Results from the first phase of a study into Canada’s recycling system found that flexible materials account for 47% of the plastic packaging put on the Canadian market.
The PRFLEX initiative, which aims to optimize the recycling system for flexible plastic packaging (FPP), was spearheaded by the Canada Plastics Pact, the Circular Plastics Task Force, Circular Materials, the Chemistry Industry Association of Canada, Recycle BC, the Film and Flexibles Recycling Coalition of the The Recycling Partnership, and Eco Enterprise Quebec.
The goals of the PRFLEX study are to improve upstream innovation, design for circularity, collection, consumer education, sorting, recycling and end market development. The first phase of the study assessed collection and recycling rates for flexible plastic packaging in each province, and did a gap analysis of the infrastructure and technologies in MRFs.
During a Dec. 13 webinar on the results, moderator Charles David Mathieu-Poulin, strategic adviser for the Circular Plastics Taskforce, said the research found that not only does FPP make up just under half of the plastic packaging that is put on the Canadian market, but there’s an estimated growth rate of 4.2% year to year through 2030.
“Everything that we’re going to be talking about today is going to become even more and more important as years come along,” he said, especially with increasing voluntary and regulatory pressure on recycling FPP: Under the country’s extended producer responsibility law for packaging, Quebec has a target of a 40% recycling rate for FPP by 2027, and Ontario a 25% rate by 2026.
Collection largely centered on PE
The first phase of the study gathered baseline data, identified infrastructure gaps and proposed new technologies to help increase recycling rates. The research was carried out between March and June of 2023.
Mathieu-Poulin noted that around 70% of Canadians have access to a collection system for FPP, but the vast majority of those systems only accept PE-based films. Those systems bring in between 46,000 and 59,000 tons of FPP per year, and between 3% and 4% of that is ultimately recycled.
“There’s a bit of a lack of of reliability in some of the data that we have right now, so we’re still figuring that out, but we can see between 15% and 20% is actually collected, which is quite low compared to other materials, and then it’s even it’s even lower when you consider the recycling rate,” Mathieu-Poulin said.
One easy way to increase the rate is to start accepting more resin types and multi-material structures, he noted.
The report also included a waste audit. Looking at 31 samples from Ontario, Mathieu-Poulin said results showed that the majority of the FPP in both the waste and recycling stream is mono-material, typically PE. Another 30% was other FPP, including metalized films, PVDC, nylon and multi-material.
Panelist Sam Baker, vice president of operations for Western Canada at Recycle BC, noted that his organization has been piloting depot film collection for years. BC has collected plastic bags and overwrap, segregated, since 2014 through a network of over 200 depots.
In 2018, Recycle BC started collecting other FPP, such as multi-laminate material for use in research and development by its plastics end market Merlin Plastics and for conversion into an engineered fuel. In 2022, Merlin found a way to recycle the material, so in 2023 Recycle BC combined all three collection categories into one stream.
“This has made it much easier and more convenient for residents to recycle,” Baker said. “In the depot you’d be faced with one bin and you no longer have to make that differentiation.”
The depot network has captured just under 25% of the flexible plastics placed into the marketplace in BC for residential purposes, he noted, which is “an unprecedented average across North America, but still a long way off from these aggressive targets” EPR laws have in place.
To try to increase the rate, Recycle BC ran a pilot project in 2021 in West Vancouver to collect flexible plastic curbside in its own bin.
“The pilot was a success because it showed the advantages of this convenience,” Baker said. “When we looked at the per-household capture rate, it was over three times what we get through our depot network.”
Based on that pilot, Recycle BC has committed to curbside collection in two metro Vancouver municipalities, rolling out in mid- to late-2024 and 2025.
“We haven’t committed to any trials where the material is co-mingled in with other streams because this places significant risk on our commodity revenue and marketability, but we continue to pursue these types of solutions in conjunction with the PRFLEX partners because the cost advantages would be significant if we could make it work properly,” Baker added.
Actionable steps
Paul Shorthouse, director of strategic initiatives at the Canada Plastics Pact, said the data calls for better harmonization and adoption of the Canadian Golden Design Rules to make collection and processing easier. The Golden Design Rules include removing problematic elements, eliminating excessive headspace, reducing plastic overwrap and virgin plastic use and moving to mono-material PE where possible.
“We’re also working with the Association of Plastic Recyclers out of the U.S. and more broadly to really align our guidance around the Golden Design Rules with the APR guidance and clarifying any gray areas,” Shorthouse said.
Another panelist, Sara-Emmanuelle Dubois, president of NovAxia, said there’s multiple ways MRFs could be built or retrofitted to handle FPP more effectively.
There are common methods designed for FPP capture such as air sorting, which separates FPP based on density, and film grabbers, film extractors and film hood screens which separate the material based on mechanical properties. Optics are also an option, Dubois said.
However, “although those technologies are all very efficient and they’ve proven to be efficient in capturing FPP, it seems that FPP doesn’t even get to these equipment once they’re installed in a MRF,” she added.
“They’re lost in the process. They get blended with other types of material, especially paper, and when they’re found in those streams FPP becomes a contaminant and manual sorting is then inevitable,” Dubois said. “We can’t avoid it. We have to provide resources to manually remove them and that often happens at the quality control conveyors and it becomes very expensive. It’s among the most expensive activities in the MRF these days.”
There are two main schools of thought on optimizing FPP capture at a single stream MRF, Dubois noted. Early catch aims to remove FPP from the start of the line, while a “catch all” process picks the most valuable material out first, then positively sorts the low value material, including FPP, at the end.
“Both models are, however, very hard to adapt in an existing MRF,” she said. “The catch all process strategy appears to be the best option in such a case … but only if the space is available.”
For dual stream MRFs, FPP that’s collected with packaging in one stream and fiber collected in another stream “simplifies the process, because we have a 2D material – the FPP – and a 3D material – the packaging – and it’s very easy for mechanical equipment to isolate the FPP,” Dubois said.
Panelist Pierre Benabidès, general manager for the Circular Plastics Taskforce, added that another step in the process is improving sortation and feedstock preparation by reclaimers.
“We are asking the MRF to produce a bale that is a mix of flexibles, so capturing the flexibles, but that would mean someone needs to do a more detailed sortation and feedstock preparation of it,” he said. “I think the report clearly assesses that there are several end markets that could be reached, but would require that feedstock preparation and a feedstock preparation that maybe only a reclaimer would be able to do.”
Mathieu-Poulin said looking ahead, the report recommends better harmonization, dedicated collection of FPP in the industrial and business sectors, gaining a better understanding of composition and markets, acceptance of all FPP curbside, finding solutions for existing MRFs to reduce loose FPP and improving the capability of MRFs to process FPP through technology upgrades.
Shorthouse added that the task force is “talking about putting together a steering committee of some sort or a governance body to drive these recommendations forward, so that it’s not just a report on the shelf but it does continue to engage the stakeholders and the partners that are needed to actually mobilize these recommendations.”