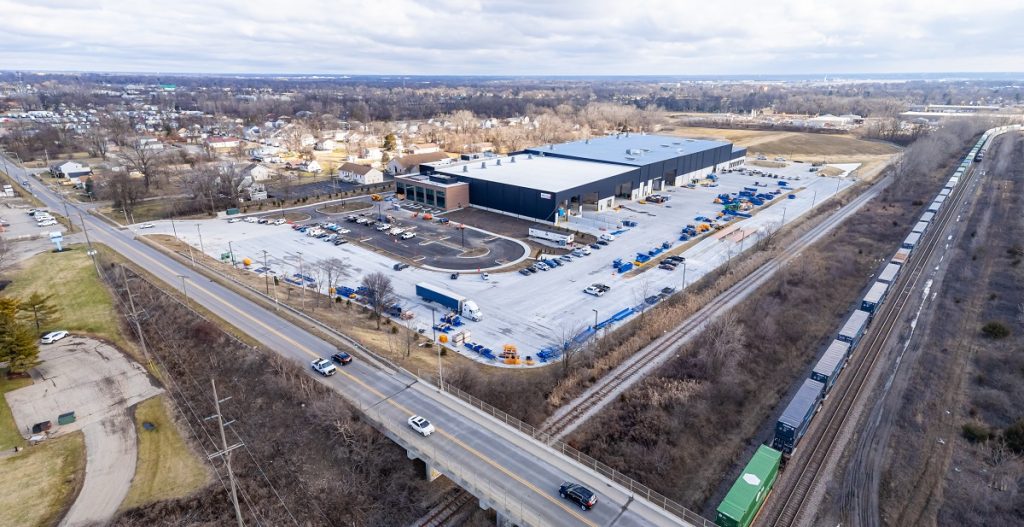
Rumpke’s new Columbus, Ohio MRF is key to a partnership with Eastman Chemical that will create an end market for opaque PET materials, among other hard-to-recycle products. | Courtesy of Rumpke
A partnership between midwest recycling processor Rumpke and resin giant Eastman Chemical will create an end market for opaque and otherwise hard-to-recycle PET materials, driven by state-of-the-art sortation capabilities at Rumpke’s Columbus, Ohio MRF.
The companies in February announced that Rumpke will begin collecting and sorting hard-to-recycle PET products – specifically opaque and colored PET materials – and will bale and sell them to Eastman, which will process the feedstock using its methanolysis technology.
The project was driven as much by the ability to effectively sort different PET streams as it was by Eastman’s emerging demand for PE feedstock, which has increased significantly with the company’s U.S. processing facility, which started up last year in Kingsport, Tennessee.
On the sortation side, the project is tied to Rumpke’s new Columbus MRF, which has been in development for over two years and is slated to start up in June this year. With that facility’s impressive sorting capabilities – particularly its 19 optical sorters – Jeff Snyder, Rumpke’s director of recycling, said the facility is well-outfitted to make new types of bales, like opaque PET.
In an interview, Snyder said Rumpke has no concerns about the project introducing contamination into the recycling stream, because it has the infrastructure and equipment in place to make it work. Quite the contrary, project stakeholders view the supply deal as a way to market and make use of what is currently a contaminant.
“We’re already getting the materials, even though we don’t accept them,” Snyder said.
That will change, as Rumpke prepares to approach the numerous communities it serves in the areas about new materials that it’ll accept through the new MRF.
Sorting technology plants the seed
Rumpke in 2022 decided to build a new MRF replacing its existing Columbus facility. While planning that replacement, company officials determined installing the best-available sorting technology meant the MRF could go deeper into the waste stream, targeting new materials, while also improving the quality of output bales.
Snyder said Rumpke installed 19 optical sorters in the new MRF, performing 34 different sorts. Instead of manual sorters cleaning up the line after the optical sort, “we’re using an optic, after an optic, after an optic, to clean up material,” he said.
But a key component allowing for targeting hard-to-recycle material streams is artificial intelligence. Rumpke installed AI systems in front of nine of the optical sorters. Snyder noted oftentimes AI is associated primarily with robots in the recycling equipment sector, but that it has much larger applications.
Paired with an optical sorter, the AI identifies the plastic product on the belt, and the optical sorter uses its air jets to blow the product into a specified stream. The combination of AI and optical sorters allows Rumpke to identify materials based on shape, color and size, rather than based on the wavelength of the plastic as in a near-infrared (NIR) sorter on its own.
“It takes a NIR optic to the next level, because it’s not just seeing the outside substrate of the material,” Snyder said. “That is the new development in the optical world.”
The Rumpke MRF will use AI to control optical sorters and to collect data, not to control robotic arms. Snyder opted away from robotic sorting in part because the facility receives so much of the currently contaminating PET products, he wasn’t sure the robots’ pick rate would keep up.
In effect, the technology upgrades created an opportunity to market what is currently a contaminant, Snyder explained. The inbound PET stream at Rumpke – and nationwide, for that matter – generally include far more than the clear PET bottles accepted in municipal programs. It includes opaque PET bottles, for example, that end up as contamination in the output bale.
Enough of the contamination, and big U.S. recovered PET buyers – companies synch as Indorama, DAK Americas, or Evergreen – may reject them. Those companies want clear, bottle PET.
Snyder saw an opportunity to use the new equipment to target those contaminants and create separate bales. All he needed was a buyer.
“Now I have the technology to do that, and the next step was, where is that material going to go,” Snyder said.
That’s when he began talking with Eastman Chemical, where representatives quickly indicated the company would take all the hard-to-recycle PET that Rumpke could supply.
Feedstock going to chemical recycling process
Sandeep Bangaru, vice president of circular economy platforms at Eastman, explained that the PET feedstocks the company is after are not currently highly recycled. Many of them have single-digit recycling rates. Eastman is after opaque bottles, used in products like dairy drinks, shampoo and other household goods.
“There’s not traditionally, historically, a great way for recycling technologies to get that back into food-grade,” he told Plastics Recycling Update. It can go into markets like strapping and carpet fiber, but those lower-value markets don’t always provide enough financial incentive for companies to start sorting out these products.
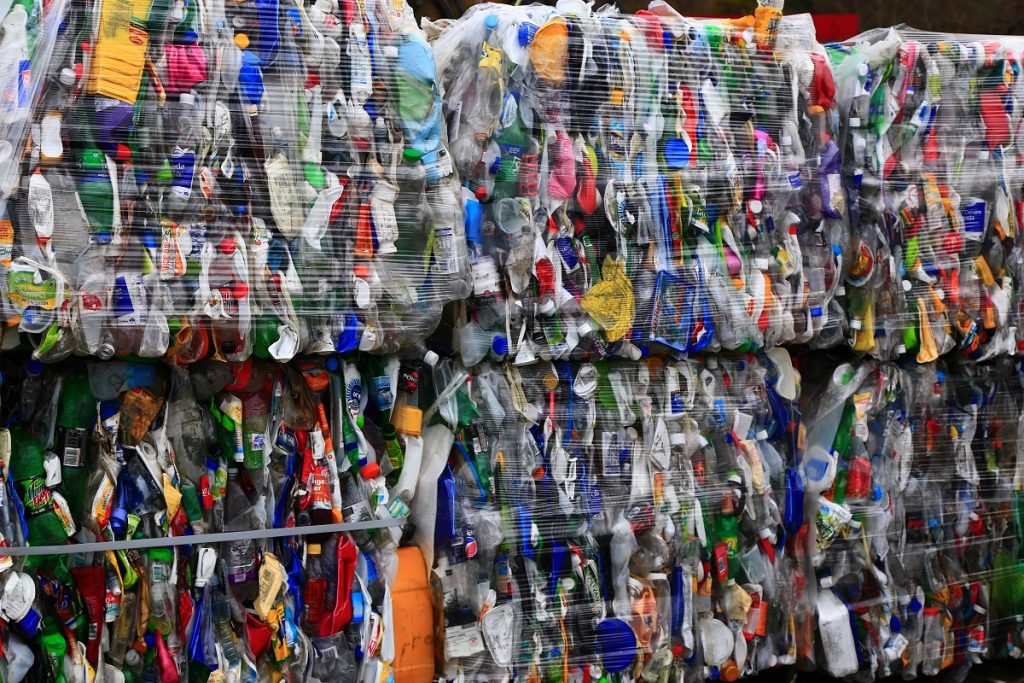
Eastman will buy bales from Rumpke to be processed at a methanolysis plant in Kingsport, Tennessee. | Courtesy of Eastman
Eastman will process the materials using its methanolysis technology, a chemical recycling process that takes in scrap plastic and reduces it to its component monomers using methanol at high temperatures. The company’s Kingsport facility is one of the world’s largest methanolysis facilities, with an estimated full-scale capacity of more than 100,000 metric tons per year.
The output, which Eastman has branded its “Renew” resin line, is attractive to consumer packaged goods companies because it can go into any type of packaging, including food-grade. PepsiCo, for instance, has signed an offtake agreement for Eastman’s Renew resin.
“Really, you have the whole gambit available,” Bangaru said. “We’re creating a market for this material that historically didn’t have a stable end market.”
And it is indeed a marketed commodity – Eastman will buy the scrap plastic from Rumpke, similar to any other baled recyclable. The volume to be sold and contract details are not being publicly disclosed, but Snyder said the deal indeed provides a financial benefit to Rumpke.
Bangaru said it is important to Eastman that its process is not disrupting existing outlets for commonly-recycled plastics, like clear PET bottles, and he emphasized the contamination-reducing effect of the Rumpke-Eastman deal. For reclaimers, opaque PET in clear bales becomes yield loss and residue the reclaimer has to deal with, and the Rumpke facility is sorting that out upstream.
“You end up with a cleaner clear bale for mechanical reclaimers, and you end up with recycling more of the non-clear stuff back into food-grade packaging,” Bangaru said.
To start, Rumpke will send the baled plastic to Eastman’s Kingsport facility. In the future the material will be processed at an additional Eastman processing facility, targeted for a 2026 or 2027 start-up. The location hasn’t yet been publicly announced.