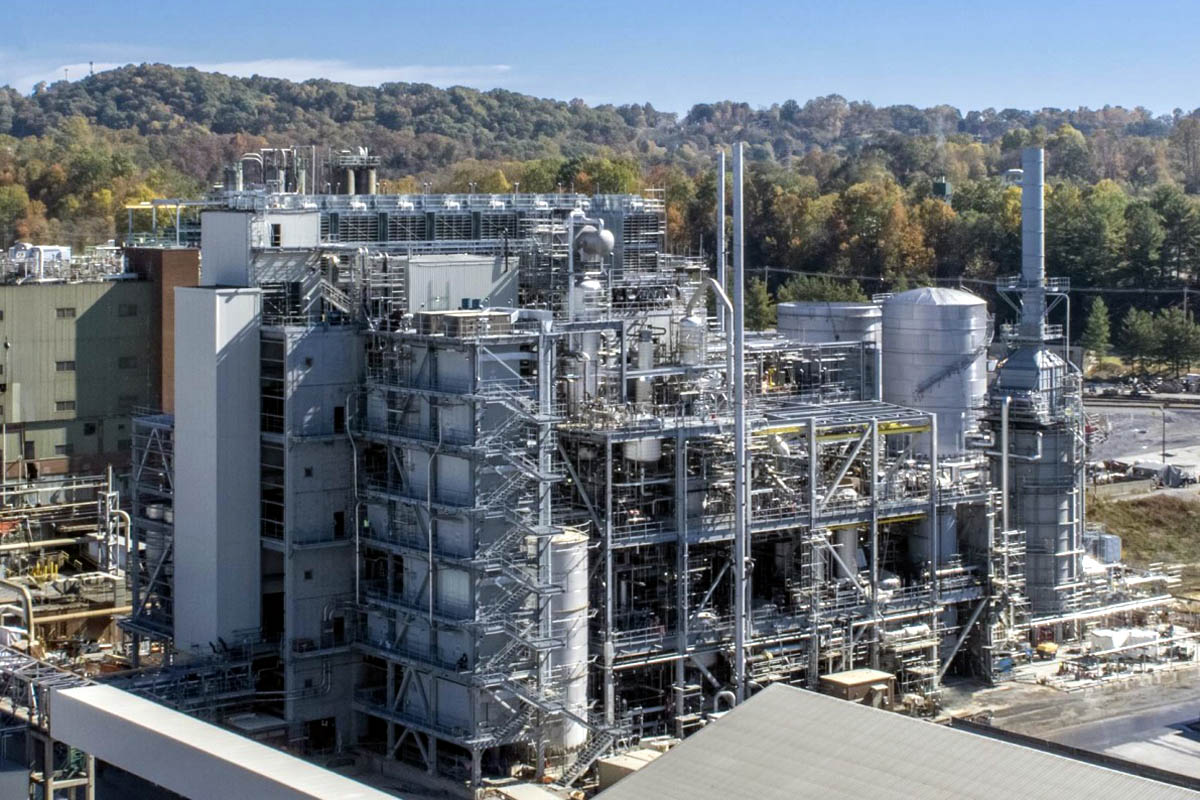
The methanolysis unit at Eastman’s Kingsport, Tenn. campus. | Courtesy of Eastman Chemical
Eastman Chemical says about 25,000 metric tons of scrap polyester have been preprocessed and are ready for recycling in the company’s new chemical recycling unit, which is slated to come on-line in coming weeks.
In recent presentations to investors, leaders at the chemical giant say they’re on track for a fourth-quarter 2023 start-up of the massive polyester depolymerization unit in Kingsport, Tenn., near the company’s headquarters.
The unit will use methanolysis technology to break down polyester scrap into PET precursor chemicals, which will be used to produce Renew-branded plastics.
According to an Oct. 26 presentation that accompanied Eastman’s third-quarter earning results, the newly built plant was to be turned over to the company’s operations teams in about three weeks. That would make it ready for handoff any time now. Officials reiterated what they said during the second quarter financial disclosure: that the plant will begin generating revenue before the end of the year.
In a quarterly financial report, Eastman reported it spent about $649 million in capital expenditures during the first nine months of the year, or about $236 million during the third quarter alone. Most of the spending went to the methanolysis plant “and other targeted growth initiatives and site modernization projects.” Eastman expects 2023 capital expenditures to total about $800 million.
All told, the methanolysis alone could cost up to $800 million. Eastman estimates the Kingsport molecular recycling unit will generate roughly $75 million of earnings before interest, taxes, depreciation and amortization (EBITDA) in 2024.
Eastman is also planning to build a similar chemical recycling plant in France and a second one in the U.S.
‘Feeling really good on the feedstock side’
During an Oct. 27 conference call with investors, an analyst asked about any lessons learned and costs involved with preprocessing the polyester scrap materials.
Eastman CEO Mark Costa described the front-end process as a “proprietary new process that we developed that takes a lot of steps out of the sortation compared to a mechanical recycler.” He said it’s up and running and working well.
He acknowledged that “feedstock was a big question in the beginning of this whole process as a risk. We’ve actually managed that one reasonably well.” The company already has about 70% of the feedstock for the France plant under long-term contracts, he said.
In terms of feedstock purchasing and preprocessing costs in Tennessee, he said, they have been a little better than Eastman expected. “So we’re feeling really good on the feedstock side here,” he said.
Methanolysis breaks PET into the chemicals dimethyl terephthalate (DMT) and ethylene glycol (EG).
During the call, Costa discussed how Eastman has the ability to use the DMT produced in different Eastman products, giving it flexibility to sell into different markets. He noted that the company’s Triton products are typically sold for use in durable goods, a market that’s down right now.
“The good news around our assets in Tennessee is, they’re flexible, right? We can swing our Triton lines between Triton and making copolyester. We can make PET. We can assign that recycled content to whatever products we want across our integrated system,” Costa said.
If the durables market is down, the DMT can be processed into copolyesters and PET used in packaging, he noted.
“So we’ll be monetizing the full value of all the DMT as fast as we can make it and driving that utilization rate up as fast as we possibly can,” Costa said. “And then, as higher-value markets like Triton come back, we’ll shift the mix in how we assign the recycled content to the higher value markets.”
Later, in response to a question about pricing, Costa said Eastman has been able to fetch the premiums it needs for its recycled-content specialty products, and it’s having good conversations with customers about paying premium prices for recycled-content PET.
“Customers are very surprised and impressed by the low-quality material that we’re using that is headed to – cannot be reused with mechanical recyclers at all,” Costa said. “This is going to go to landfill or incineration or really low-end applications. And they’re just very impressed that we can take that garbage and turn it into a clear, food-grade-quality pellet.”
The company is targeting applications, especially in PET packaging, where mechanical recycling can’t produce a high-enough quality pellet, he said.
“So we are really targeting those applications where mechanical is not a choice,” Costa said. “That allows us to command a better premium than mechanical and support our economics.”