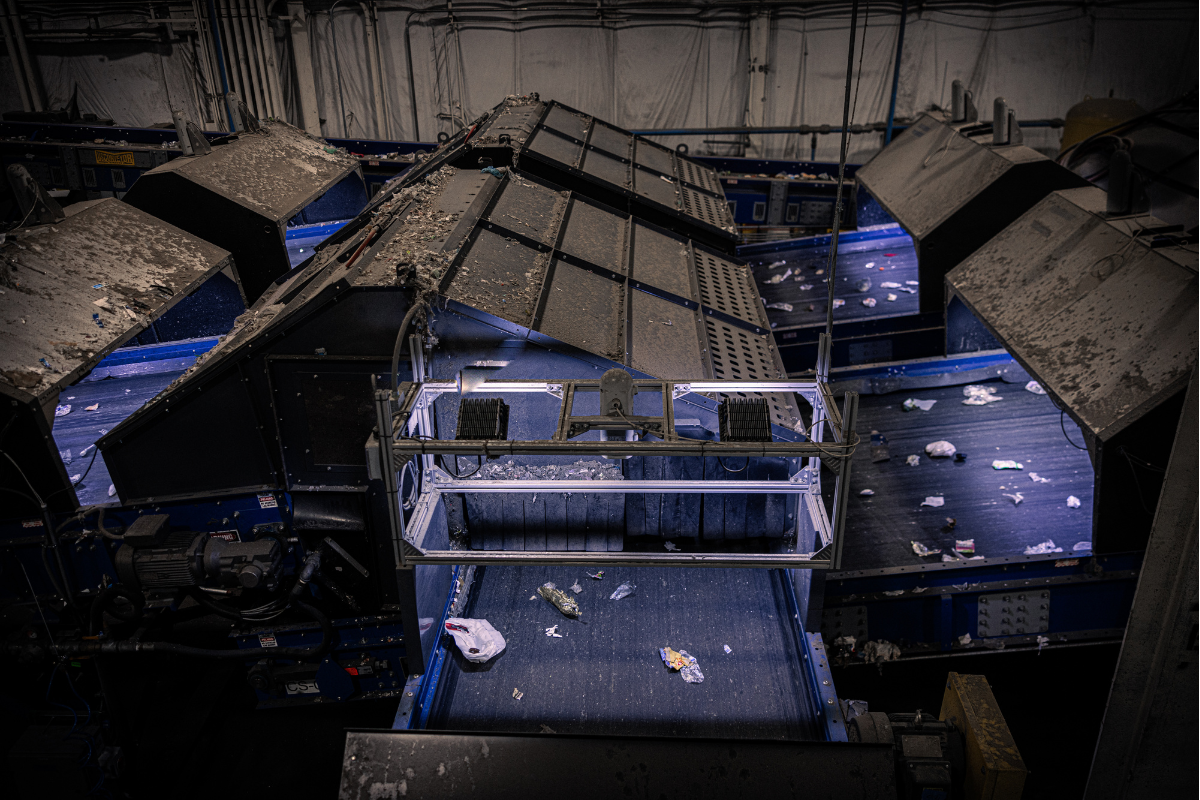
An AMP One fully automated AI sorting system operating at the company’s Cleveland, Ohio secondary sortation facility. | Courtesy of AMP
After 10 years helping materials recovery facilities retrofit with innovative robotics equipment, AMP Robotics has dropped the latter part of its name, reflecting an emerging focus on building recycling centers from scratch with AI-equipped sorting systems.
Based in Louisville, Colorado, AMP has expanded over the past decade from its roots as a fledgling tech startup piloting equipment in a local MRF to a major equipment supplier with units in facilities throughout North America. The company’s artificial intelligence (AI) and robotic sorting equipment is capable of processing all manner of municipal recyclables – including most plastic resins, fiber grades and metals – as well as e-scrap and even municipal solid waste (MSW).
As the company has neared the 10-year mark in the business of developing and supplying recycling industry equipment, it has begun a new focus on supplying facilities with a complete sorting system. It’s an evolution from installing one or two units on a sorting line, and it drove the company to remove “Robotics” from its name. A new website, AMPSortation.com, also reflects the focus on delivering full sortation systems.
“The story of the company has been this continual expansion of scope of AI in the industry and what’s possible,” said Matanya Horowitz, founder and CEO of AMP, in an interview. “But the transition to system levels, we think, is a bit of a seminal moment for the company.”
The rebrand comes shortly after a round of layoffs at AMP late last year. Horowitz said the job cuts were unfortunate and were a response to broad macroeconomic trends that the company has to plan for, which guide its forecasts on purchasing and fundraising patterns. He noted the layoffs weren’t directly connected to the rebrand.
Entering new industry sectors
AMP began in late 2013 as a small operation, consisting of a workbench in Horowitz’s garage. “It was me buying stuff from Home Depot, smashing it up and putting it beneath the camera,” he recalls.
It steadily expanded from there, aided by multiple rounds of grant funding that enabled a small team of a half-dozen employees and a slightly larger workshop. By 2016, the company launched a pilot project installing one of its early robotic arms at a Denver-area MRF, Alpine Waste & Recycling. The project focused on carton recovery, with the AMP Cortex robotic arm plucking cartons off a sorting line and AMP learning about how to fine-tune the process.
“As I saw it, the first and most obvious opportunity was to help the industry with this problem of manual sorting in MRFs,” Horowitz said.
In the years that followed, AMP’s units were installed in numerous MRFs across North America, not only improving sortation but also enabling facilities to collect new data and analyze changes in the inbound stream.
By 2021, AMP itself entered the sortation sector, starting up multiple secondary-sortation facilities around the country. These centers began bringing in bales of mixed plastics and residual materials from MRFs and other suppliers, sorting them using the company’s AI and growing suite of sorting equipment, and producing plastics and fiber grades for sale into end markets.
Integrating AI from the onset
Also in the last few years, the company began to follow two emerging tracks that have led to the rebrand: First, AMP leaders began to explore the possibility of building MRFs from the ground up, with artificial intelligence incorporated from the very beginning at the design phase; and second, AMP continued expanding the types of sorting equipment it produces.
Beyond the company’s robotic arms, it has branched out into its own version of optical sorters (the Jet and MicroJet), which use visioning technology combined with AI to identify, and dozens of air nozzles to direct, recyclables on the sort line. AMP also produces a belt-mounted vacuum sortation system targeted for removing thin plastic film from sort lines.
The interest in supplying entire facilities, mixed with the expanded equipment offering, led to AMP One, which the company bills as “the first zero-manual-sortation MRF.” It’s a modular facility capable of achieving anywhere from 15,000 to 100,000 tons per year of throughput, using entirely automated equipment. The system “autonomously transforms single-stream, municipal solid waste, MRF residue, mixed plastics and other infeeds into valuable bales,” the company states on its website. AMP says its MRFs can be ready in less than nine months from order date.
“Building AI in at the facility level really is a transformative step,” Horowitz said, adding that it opened up new conversations with customers: “We were talking to folks in a really different way than we were talking to them about just one or two robots in a MRF.”
The idea of entirely automated, tailor-scaled, AI-driven MRFs also opens new doors: For example, it might make a rural MRF feasible where it was previously too expensive or logistically challenging, Horowitz said.
Because the company was having different conversations, and talking with a wider range of customers beyond MRF operators doing retrofits, AMP officially rebranded on Feb. 1. Horowitz expanded on the name change in a post on AMP’s website.
For his part, Horowitz says the shift to supplying sorting systems on a facility level is fulfilling an early vision he had for AMP.
“This is kind of what I really wanted to be doing when I started the company 10 years ago,” he said. “Really move the economics of recycling, so that recycling access can be expanded, so that places where recycling centers didn’t make sense before, now make sense. It’s kind of like, ‘We’ve got all the tools we needed. We’re starting to make the sort of change we were hoping for.'”