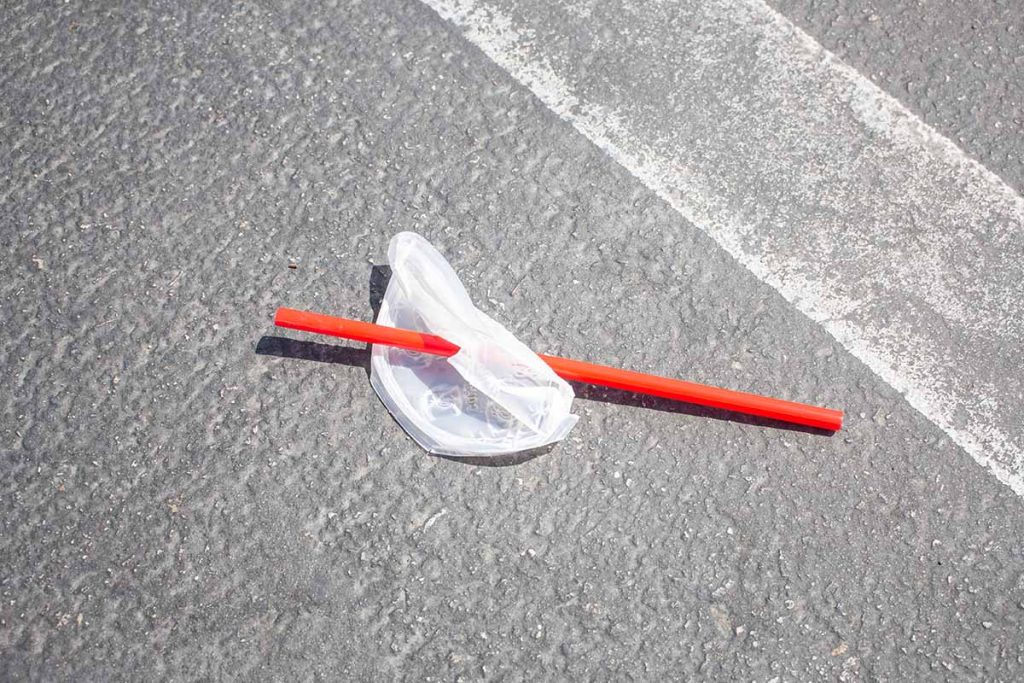
Founded in Costa Rica in 2018, CRDC now operates in Pennsylvania, New Jersey, South Africa, Mexico, the U.K., New Zealand and Hong Kong. | The Image Party/Shutterstock
CRDC Global is turning hard-to-recycle plastic into a concrete additive in Pennsylvania and plans to expand across the country as quickly as it can.
The company in mid-October brought its first commercial-scale facility in the United States on-line in York, Pa. Ross Gibby, CRDC chief operating officer, told Plastics Recycling Update that while the company has “some pretty aggressive goals,” the plastics issue merits such aims.
“We feel very fortunate that we have a solution that can give a benign end of life to plastics that are currently not able to be recycled and are ending up in landfill,” he said.
CRDC takes plastics and turns them into an additive for structural concrete called RESIN8, which reduces weight, slows water absorption and improves insulation.
Building the base
CRDC was founded in Costa Rica in 2018 and now operates in New Jersey, South Africa, Mexico, the U.K., New Zealand and Hong Kong. The Pennsylvania facility is CRDC’s second commercial-scale plant, Gibby said, but there are three others slated to come on-line soon in Samoa, South Africa and Australia.
The company partnered with the Alliance to End Plastic Waste in 2021 to help scale up operations. In a press release, Steve Sikra, vice president and head of the Americas at the group, said “plastic waste is a resource with value that can be unlocked with the right technologies and solutions,” and RESIN8 is one such solution.
“From the time we began working with CRDC Global, they have made tremendous strides in improving their process and perfecting their new technology,” Sikra added. “We are proud to be journeying with them to scale up their technology around the world.”
Gibby said CRDC is also focused on reducing transportation as much as possible, and estimated that to cover the “massive geographical area” of the U.S., the company will likely need around 75 plants.
York, Pa. was selected as the first large-scale location due to its easy access to markets for both construction products and construction projects.
“It’s got the main highway arteries that make it very accessible,” Gibby said. “The other advantage is York is widely considered an industrial region, I think because of its location, so we knew the infrastructure was going to be there to support our needs.”
The York facility is a little smaller than CRDC originally planned for due to available building space. Gibby said CRDC did not want to build out a new structure, and the lead time to upgrade the building it chose with more power capacity was nearly a year due to supply chain slowdowns.
The plant will have a capacity of 1 ton per hour, and so should be able to do about 20 tons a day. Originally, CRDC was hoping to do 25-30 tons a day.
“We decided to go with the lower capacity and max out what we could in this location, and continue to talk to the mayor about expansion,” he said.
The company already has a few offtake agreements in place for its additive, with Fizzano Brothers Concrete Products and York Building Products, and is in discussions with several other local and national companies, Gibby said.
In addition, CRDC has a partnership with Georgia-Pacific, which acts as a broker to get the company feedstock, so CRDC can “focus more on the conversion and transformation of the plastic.”
Georgia-Pacific has strong ties to MRFs in the area, Gibby said, which made York a strong option when the company was in the early planning stages. Since then, however, CRDC has realized that mixed bales from MRFs often contain too many contaminants like glass and metal to be usable.
“Once it’s baled up with all those others, it’s not extractable for us at that point,” he said.
Instead, a large portion of the feedstock for the York facility is coming from nearby industrial sources. Gibby said CRDC is also currently getting some cleanup event plastic from as far away as Alaska, but “that’s temporary because our objective is to have plants everywhere.”
The additive can be made with plastics 1-7, including multilayer polymers, Gibby said, and can handle some level of organic contamination – such as sand off beaches, slime out of rivers, food out of municipal waste streams or paper labels.
The third stream of feedstock comes from CRDC’s “Bag that Builds” program, which allows residents to turn in plastics to the facility. York residents have responded enthusiastically to that program, Gibby said.
“We’ve been pleasantly surprised by how much engagement we’ve gotten from the community itself,” he said. “If we had gone to a much larger city we wouldn’t have necessarily been able to make as much of an impact in the community or had so much engagement and enthusiasm and passion for what we’re doing.”
Gibby said CRDC never really promoted the bags program, but the local Rotary Club learned of it and got involved, spreading the message to other local groups and businesses.
A local business decided it would become a bag collection point, then the mayor set up three more collection points around the city. Schools got involved, and Gibby said people have embraced it.
“It’s really taken off,” Gibby said. “We have people stopping by all day long and they don’t just want to drop off the bags, they want to talk and understand what we’re doing with the material, how it works. Some still are doubtful we can take everything they can put in the bag, and we educate them.”
Looking to expand
Gibby’s goals are to expand across the United States and globally, because there’s “considerable interest from island countries that have limited landfill space that inherit a lot of plastic washing up on beaches, and are tourist areas with a lot of visitors that create waste.”
Right now, CRDC is developing national partners to help the company expand in the U.S. “as quickly as possible.” Gibby said the company is currently developing a strategic plan for which locations will come next.
“It’s been kind of mind-blowing, to tell you the truth,” Gibby said. “I think it’s going to get bigger. It gives people hope. None of the plastic is going to landfill, none is getting burned and it won’t end up in the environment … it’s going into concrete that will help build their own community.”
More stories about technology
- RIT researchers develop AI-based textile recycling system
- Industry nuance is key in adopting emerging technology
- Google, Dow partner on AI to identify recyclables