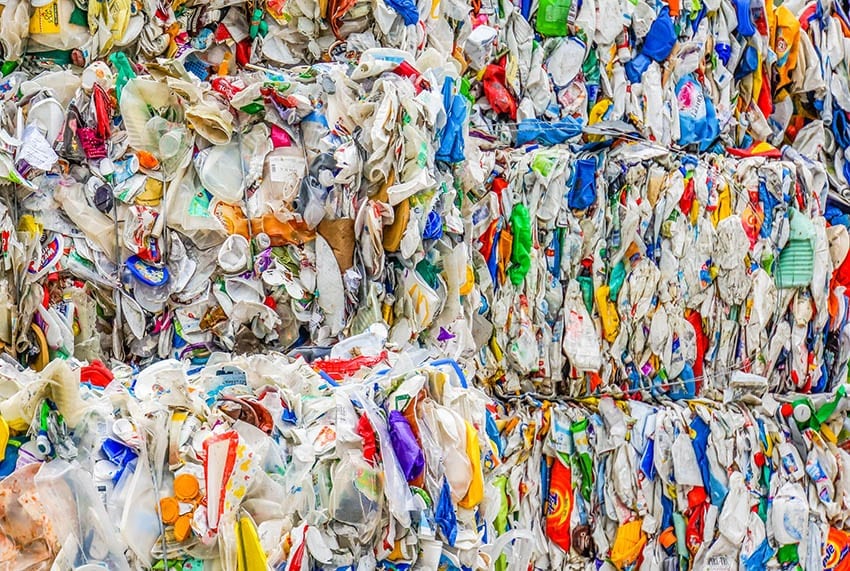
EFS-plastics described how virgin resin pricing and other factors are impacting the recycling sector. | Ann Moore / Shutterstock
The mixed-plastics processing sector is seeing supply challenges from product labeling changes and could be significantly disrupted by chemical recycling initiatives, according to one processor.
During a recent virtual event held by the Northeast Resource Recovery Association (NRRA), Eadaoin Quinn, director of business development and procurement at EFS-plastics, described factors impacting the mixed-plastics industry.
EFS-plastics is a reclaimer with locations in Hazleton, Pa. and Listowel, Ontario that processes mixed-plastic bales and is a significant player in the North American reclamation landscape.
Supply and demand dynamics
Several external factors are currently influencing the mixed plastics sector.
Quinn referenced the 2020 change to how PP is labeled in the How2Recycle labeling program – the resin was downgraded from “widely recyclable” to “check locally.” That was due to a decrease in collection access nationally, but also due to uncertainty in how much PP was truly being reprocessed after leaving the MRF.
Quinn said the change was made for valid reasons, but she added it has made things difficult difficult for reclaimers.
“We’re looking for more polypropylene, and now the public might be receiving the message that, their yogurt cups, they should be landfilling them,” Quinn said. “And even if your community is encouraging people to recycle yogurt cups, they might just be looking at the label and disposing of it.”
EFS-plastics is also paying close attention to extended producer responsibility (EPR) legislation being considered in states in the U.S. Quinn said that type of policy could inject more funding into the recycling system and increase diversion rates.
Additionally, the company is monitoring the chemical recycling sector, which has begun sourcing huge quantities of mixed plastic.
“We’re seeing more and more attention given to chemical recyclers, which could potentially drain some of the feedstock that we’re looking for. [It] might be going off to chemical recyclers, and none of them are yet operating at industrial scale,” Quinn said.
On the demand side, Quinn noted prices for post-consumer PE and PP are high right now. But the factors behind that price dynamic may not keep values high for long.
“Unfortunately, that does not seem to be driven by the demand for specifically post-consumer material. It seems to be driven by the price of virgin plastic having increased,” Quinn said. Virgin pricing has increased, in part, because of the production downtime spurred by massive winter storms in Texas, she added.
“People are now willing to pay more for recycled plastic because they can’t get their hands on the virgin material,” Quinn said. “So when production goes fully back up to speed again on the virgin plastic side, we do anticipate that the price of the post-consumer plastic will decline again.”
Finally, Quinn touched on the common question of whether there is enough recycled resin supply to meet the projected demand from major brands increasing their PCR consumption. In general, industry experts say there is not enough PCR currently to meet incoming demand. But Quinn offered a different take.
“Often they’re talking about, is there enough clear, food-grade material so that they can make packaging out of it?” Quinn said, and she acknowledged there is not enough of that specific PCR for packaging. “But from my perspective, is there the right demand to meet the supply?”
Residential recycling programs supply a great deal of colored, non-food-grade plastic, Quinn said, and that is not typically what brands are looking for in their recycled plastic use.
“What are we going to do with all this material that currently is collected, that we would like to see recycled, if the end market demand doesn’t match what is currently available?” she asked. “I don’t have the answer, but I think that is the question that needs to be posed, and we all need to be thinking about, how do we connect these two problems.”
On the hunt for ‘Goldilocks bales’
Quinn also described the material EFS-plastics is looking to source.
The company produces HDPE, LDPE and PP pellets, which are sold to some 45 different markets each month, Quinn said. They go into recycling containers, industrial corrugated piping, furniture, garbage bags, reusable grocery bags and more.
EFS-plastics is currently processing 45,000 metric tons of plastics per year. In any given month, EFS-plastics buys 100 different truckloads of 3-7 plastics in North America, Quinn said.
“We’re not recovering polystyrene or PVC, so the 3-7 is a really bad name,” she said. “We’re really looking for polypropylene and polyethylene, not all those random types of materials that could be in there.”
Quinn said the company is looking for “Goldilocks bales,” meaning those that are right in the middle between extremely contaminated and extremely clean.
“We don’t need the bales to be perfect,” she said. Some reclaimers are pushing for very clean PP bales, she noted, and those companies are willing to pay premiums to bring in that material. EFS-plastics has a different strategy.
“That’s really not how we’re set up,” she said. “We are anticipating quite a bit of contamination to be in there and we have very efficient ways to remove that contamination.”
Still, the company does not want to bring in the more serious contaminants that show up in MRFs, such as batteries or tanglers. EFS-plastics is looking for bales that have those major residual items removed, but that have not gone through the cleaning processes that raise their price.
“It’s surprisingly hard to find that middle ground,” Quinn said.
More and more MRFs are installing optical sorters to separate out PP and create specific bales for that resin. At the same time, others are producing a 3-7 bale that “truly is just the residue coming out of the MRF,” Quinns said.
EFS-plastics has different requirements for suppliers, based on where the supplying MRF is located. For example, for facilities that are closer to the company’s processing plants, EFS might accept bales with higher contamination levels, she said. But for suppliers farther away, on the West Coast, for example, “it really doesn’t make sense to ship a lot of waste all the way across the country, so we ask them to clean it up a bit more.”
A version of this story appeared in Resource Recycling on May 18.
More stories about plastics
- Colorado Summit covers chemical recycling, EPR trends
- News from Association of Plastic Recyclers, Dock 7 Materials Group and more
- MRFs, reclaimers finding added value from AI