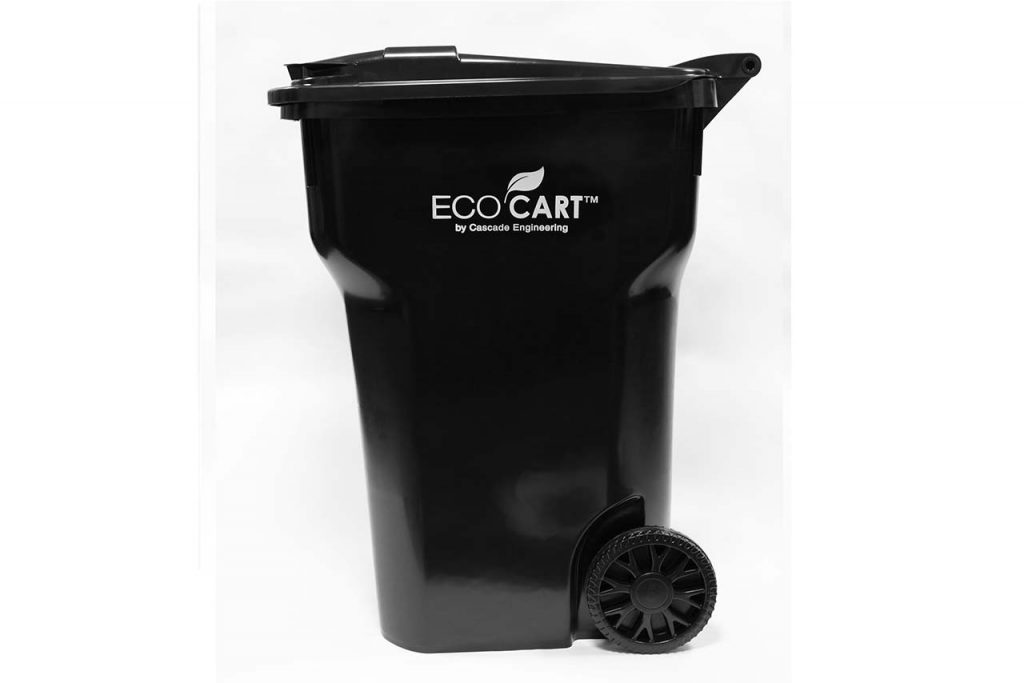
The EcoCart is made with 10% post-consumer HDPE derived from bulky rigids. | Courtesy of Cascade Cart Solutions
Cascade Cart Solutions has produced 22 million carts for Waste Management over three decades, but last week marked a milestone: the first time the company has deployed carts made with recycled curbside residential plastics.
Cascade Cart Solutions worked with Waste Management, the largest garbage and recyclables hauler in North America, to develop the EcoCart, which is made with 10% post-consumer HDPE derived from bulky rigids. Production of the cart will divert over 6 million pounds of post-consumer resin (PCR) from landfills this year.
EcoCart is the product of a year’s worth of development and testing.
“We’ve been able to accomplish something that a year ago I didn’t think was possible,” said Jo-Anne Perkins, vice president of environmental systems and services at Cascade Cart Solutions, based in Grand Rapids, Mich.
In an interview, Perkins provided more details on the development of EcoCart and the challenges the manufacturer faces using post-consumer resin (PCR) in products that need to be tough and long-lasting.
Sparking the idea
For a decade and a half, Cascade Cart Solutions, a division of Cascade Engineering, has recycled carts into new ones. But EcoCart is the first time Cascade has sourced the recycled resin from bulky rigids, a category that includes items such as post-consumer laundry baskets, pet containers, lawn furniture and more.
KW Plastics supplies the recycled HDPE pellets to Cascade Cart Solutions’ plants in Grand Rapids and Brownsville, Texas. KW acquires bales of bulky rigid plastics from materials recovery facilities (MRFs) run by Waste Management and other curbside haulers, Perkins said. At its Troy, Ala. recycling facility, KW sorts and processes the scrap plastic to produce dark gray HDPE pellets, which Cascade uses in its black EcoCart.
Perkins said she was attending the Waste Management Sustainability Forum in January 2019 when she heard Brent Bell, Waste Management’s vice president of recycling, emphasizing the importance of creating demand for recycled resins, particularly in light of scrap import restrictions in Asia. Afterward, Perkins began working with Liz Bedard of The Recycling Partnership and the Association of Plastic Recyclers (APR), as well as officials at KW and Waste Management, on a strategy to incorporate PCR from curbside bulky rigid plastics into carts. (APR owns Resource Recycling, Inc., publisher of Plastics Recycling Update.)
Development of the cart, which involved trial and error, took nearly all of 2019, Perkins said. Because the carts are exposed to the elements and frequent collection, yet they still have a 10-year warranty, robust testing was needed to ensure they could hold up. Testing involved loading 300 pounds into different cart iterations, heating the carts to approximate Arizona summer temperatures or freezing them to mimic Minnesota winter temperatures, and then dropping them down an elevator shaft, she said. The company also used a semi-automated arm to test their resilience during the collection process.
In November 2019, Cascade completed testing on a black 96-gallon cart that contained 10% PCR and still passed testing with flying colors, Perkins said. Jim Fish, Waste Management’s CEO, announced that his company would use the cart during the 2020 Waste Management Sustainability Forum.
Cascade’s first production run of EcoCart began on March 9. The carts began their roll-out in the northeast U.S. last week.
Waste Management is currently placing orders for EcoCarts for distribution all over the country, Perkins said.
Challenges with using PCR
Cascade Cart Solutions stores the PCR in silos. From there, the pellets go into a blender system that mixes in a UV protection additive and colorants before the material is weighed and dropped into the back of the mold, according to Perkins.
In general, using PCR comes with challenges and added costs, she said.
“As a large tonnage injection molder, we face big challenges in terms of designing our parts, and to have customers change mid-stream and go from virgin material to recycled material – it changes the parameters on everything we’ve done in terms of design and processing,” she explained.
Using it at the 10% level in EcoCart doesn’t require slowing the injection molding machines (the company did slow them during testing because of concerns about how the PCR might affect the multi-million-dollar pieces of equipment). But PCR use does increase the generation of production scrap, Perkins noted.
The PCR isn’t more expensive than the virgin plastic, but it brings Cascade added costs in the form of separate PCR handling systems, she said. Cascade is absorbing the extra costs, however, charging Waste Management the same price for the cart, guaranteeing the same performance and offering the same warranty, she said.
She also noted there’s a certain percentage of PP that remains in the HDPE pellets, and that PP has a tendency to make the HDPE product brittle. If Cascade didn’t struggle with PP content, it could probably boost the recycled content in the carts to 20% or 25% very quickly, she said. She noted the supply of bulky rigid plastic scrap is ample across the country.
“Our next goal is to work with suppliers to get a cleaner HDPE recycled stream and start boosting the percentage in the cart,” Perkins said.
More stories about rigid plastics
- Bottle cap design: No need to ‘reinvent the wheel’
- Mondelez, General Mills, Cotopaxi report progress
- Procurement tactics adapt to new supply realities