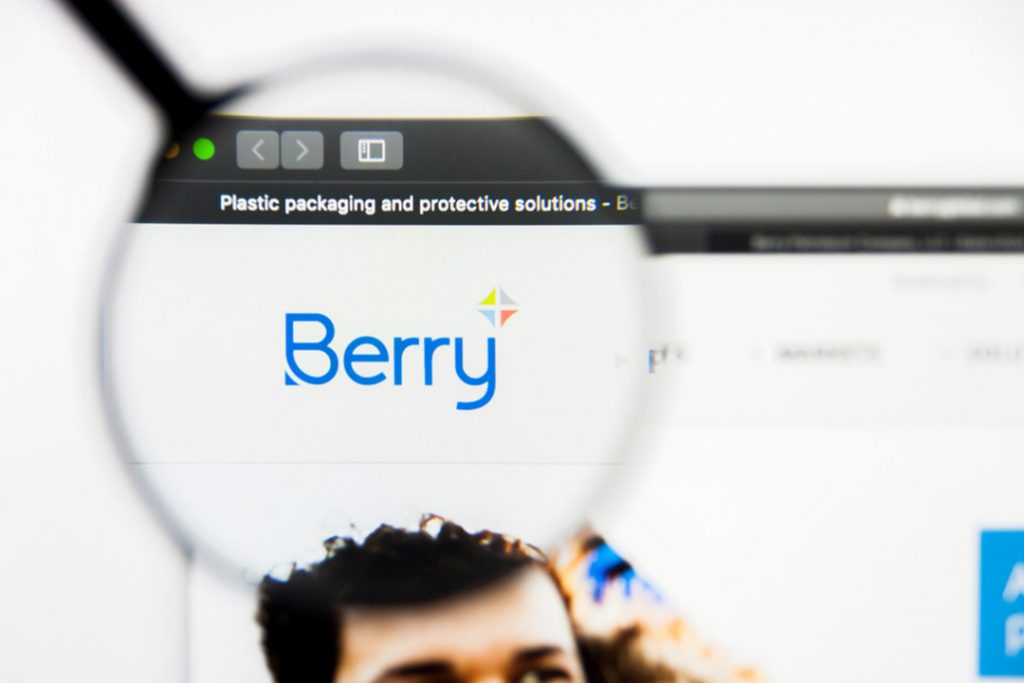
A leader with Berry said the company will use more chemically recycled polyolefins as supply increases. | Pavel Kapysh/Shutterstock
Berry Global’s use of chemically recycled LLDPE in demonstration pouches is only the beginning of the company’s embrace of post-consumer plastic recycled via pyrolysis.
“We look forward to expanding our usage of chemically recycled resin both in Europe and North America as the use of this technology further develops and expands,” said Robert Flores, vice president of sustainability for Berry, a worldwide packaging producer.
In November, Evansville, Ind.-headquartered Berry Global announced it used chemically recycled plastic from Saudi Basic Industries Corp. (SABIC) to produce co-extruded stand-up pouches. Flores recently provided more details on the partnership and its potential.
Recovering low-value mixed plastics
The non-barrier all-polyethylene pouches created by Berry BPI in Europe include 30% recycled LLDPE, with the remainder being virgin plastic. The post-consumer plastic came from low-value, mixed plastics that had been processed by Plastic Energy. The U.K.-headquartered company used a patented pyrolysis process it calls thermal anaerobic conversion (TAC) to produce TACOIL, which was fed into SABIC’s plastics production facility in Geleen, Netherlands (SABIC first signed an agreement with Plastic Energy to use TACOIL in June 2018.)
Plastic Energy currently operates two industrial facilities in Spain, and it is working with SABIC to open a facility to refine and upgrade TACOIL in the Netherlands – currently, the TACOIL must be refined before it can be fed into SABIC’s crackers. The Netherlands TACOIL plant is expected to enter commercial production in 2021.
“SABIC’s timeline for beginning semi-commercial production is one of the fastest we have seen in the industry and we were eager to join with them in initiatives that support circular economy,” Tom Salmon, Berry’s chairman and CEO, stated in the November press release.
Flores said Berry will use more chemically recycled polyolefins as supply increases.
“We have thus far started with fairly modest quantities and look forward to growing our usage as SABIC scales up their production,” he said.
Berry isn’t the only company that has used SABIC’s chemically recycled polyolefins. Tupperware Brands and Unilever are among the brand owners using the plastic.
No replacement for mechanical recycling
Berry sees chemical recycling as a complement to mechanical recycling technologies, one that can recover the difficult-to-recycle scrap otherwise bound for disposal.
Flores noted that Berry BPI, which produced the demonstration pouches, is also one of the largest film recycling companies in Europe. The company sells many films with post-consumer content reclaimed by Berry via mechanical recycling processes. Those products include X-EnviroShrink shrink film with up to 75% recycled content and The Green Sack trash bags with 100% recycled content.
When asked whether Berry has to pay more for chemically recycled plastic given the additional processing costs, Flores said Berry anticipates chemically recycled plastic will have a premium as the technology scales up, “but that is not to imply it won’t be economical.”
“We see mechanical recycling continuing to focus on high volume, high consistency waste streams that command a higher price in the market,” he said. “Chemical recycling is targeting waste streams that are typically being landfilled or incinerated today. The hope is that as chemical recycling scales, the lower raw material cost will be able to offset a higher processing cost.”
To receive the latest news and analysis about plastics recycling technologies, sign up now for our free monthly Plastics Recycling Update: Technology Edition e-newsletter.