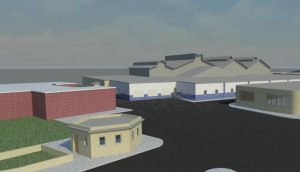
A rendering of the planned Millville Plastics facility in New Jersey.
A $20 million New Jersey plastics recycling facility is in development, and project leaders say it will process roughly 100 million pounds of scrap plastics per year for sale into a variety of end markets.
Recently formed Millville Plastics will process PET, HDPE and possibly PP, sourced both domestically and from overseas MRFs. The company is developing a 350,000-square-foot facility, and it will sell material to manufacturers of sheet and fiber-grade PET. The company will also produce preforms for FDA- and non-FDA-sanctioned applications.
The venture is led by a team of partners including Anthony DeSantis, who has more than two decades of experience in the plastics recycling industry, operating recycling centers as well as mixed-waste processing facilities.
The project has been in the works for over three years, with much of the planning stage focused on finding the right site. The company recently signed an agreement with Millville city officials to purchase property formerly home to a glass factory.
In an interview with Plastics Recycling Update, DeSantis said market turbulence in the wake of Chinese import restrictions is one factor pushing the project forward.
“When China closed its doors, it affected all the small counties,” DeSantis said, noting that prices have dropped considerably and transportation to processing facilities outside the area has become cost prohibitive.
The Daily Journal newspaper, which reported on the agreement to develop the facility, quoted local officials who have been supportive of the facility as a new outlet for materials in the region.
Operational specifics
The plant will hire about 50 employees working three shifts, and increase its employment proportionally as it scales up. It anticipates the facility coming on-line in about two years.
“It will take us about a year to renovate the property and about another year to put together all the equipment,” DeSantis said.
It will process recovered PET and HDPE, and may also process PP caps. The company will source its material partially from MRFs in Delaware, New Jersey, New York and Pennsylvania, but will also be importing scrap from overseas MRFs.
“That’s why we want to be close to the water,” DeSantis explained. “We have facilities overseas that we work with, they supply us with HDPE.” Milville is located in southern New Jersey, close to major ports.
The company will recycle the material into flake form, and from that point further processing will be dependent on the customer’s needs. Some customers will be purchasing the material as finished flake. In other cases, the recycling company will produce preforms, potentially including beverage container preforms. Processed HDPE will be injection grade, DeSantis said.
Millville Plastics is additionally looking into utilizing its own in-house scrap, potentially to make products such as flower pots or trays, DeSantis noted. Or could use it for thermoform production.
Facility site important
Because of the sizable property requirements and the need to have easy port access, “a major delay was finding a facility that had the infrastructure to support this,” DeSantis said. “Now we have rail, we have heavy electric, we have the water, we have the industrial sewers, we have a very friendly town.”
The group purchased approximately 13 acres for a 350,000-square-foot facility that can receive 2.5 megawatts of power. The site has rail access and will have the ability to store roughly 50 railcars on-site, DeSantis said.
Directly adjacent is another 1.3 million square feet of property owned by the plastics company, allowing for future integration or expansion, DeSantis explained. That could come in the form of a customer forming a joint manufacturing venture with the recycling company as a way to reduce transportation and associated costs.
“They are invited to lease space adjacent to the building where they have access to rail and the supply side of our raw material,” DeSantis said. “It gives us an opportunity to bring in some of our customers where we could offer horizontal integration.”
To receive the latest news and analysis about plastics recycling technologies, sign up now for our free monthly Plastics Recycling Update: Technology Edition e-newsletter.
More stories about processing