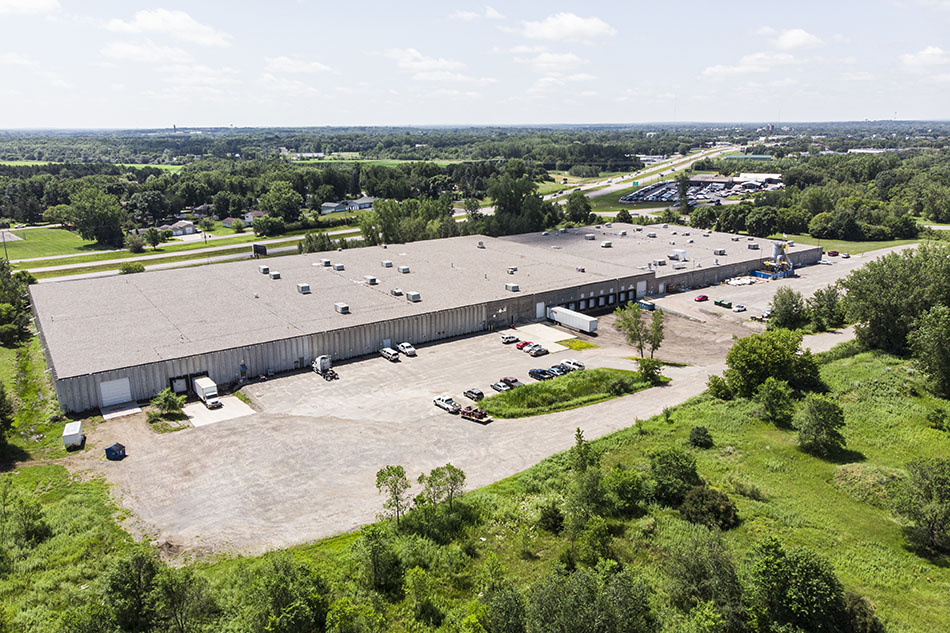
IRT is expanding and moving into this 230,000-square-foot building in St. Cloud, Minn. | Courtesy of IRT.
IRT is moving into a facility more than five times the size of the company’s current Minnesota site as its business model evolves.
Integrated Recycling Technologies (IRT) will move its Waite Park, Minn. operation, which is located in a 42,000-square-foot facility, to a 230,000-square-foot building in nearby St. Cloud, Minn., company leaders told E-Scrap News in an interview.
The move, slated for early September, comes just a couple years after the company expanded from Monticello, Minn. into the Waite Park building. After that previous expansion, IRT planned to wait five years before expanding again, but business growth drove that schedule up a few years.
The company is gearing up to increase its processing capacity from 32 million pounds per year to between 80 million and 100 million pounds per year within the next 18 months. And IRT plans to hit those volumes while avoiding the CRT glass market altogether, according to an announcement about the expansion.
The new facility will provide employees additional workspace to process incoming devices, which come in all shapes and sizes and can easily take up a significant amount of space. It will allow greater room for all processing operations and will also remove bottlenecks.
IRT is projecting the company will purchase upwards of 40 million pounds of electronics to process next year, anticipating overall sales of more than $50 million.
Growth in ITAD space
During its 2017 move into Waite Park, IRT emphasized that it was focusing its business on the electronics recycling field. IRT had recently sold multiple metals recycling divisions that did not process e-scrap.
Now, the company is pushing further into the ITAD sector, which has been growing as a component of IRT’s business over the past couple years.
Company President and CEO Steve Budd said the resale department has been “fully groomed and is ready to grow.” The ITAD division is led by an industry veteran with more than 18 years of experience in asset disposition. The company has nine employees in the ITAD and resale department.
With the new facility, IRT is planning to solidify “a more substantial presence in the ITAD and resale markets,” according to a company announcement about the expansion.
The shredding side of the business and the ITAD division complement each other, ensuring the company can extract value from devices no matter their age or condition, said Tony Celt, vice president of sales and marketing for IRT. If a device can’t be reused, IRT can still shred it and sell its commodity content.
“With our unique ability to shred things and use our metallurgical lab on-site, we’re able to know intrinsic values of things,” Celt explained.
With its capabilities, the company doesn’t have to worry about assets becoming obsolete.
“We know we’re going to be fine at the end of the day because of our capabilities in the precious metals market, as well,” he said.
Data security assurance
Along with the push into ITAD comes an emphasis on communicating to customers that proper data destruction procedures have been employed. IRT plans to use a software system that allows clients to monitor the status of their devices at any stage in the asset disposition process.
“When we’re taking in this material, data destruction is huge,” Celt said.
The system, called CycleLution, gives clients a login through which they can see everything that is done or remains to be done. That’s an important tool because, Celt explained, sometimes ITAD customers receive a certificate of destruction from their ITAD provider, even before the device has been processed. That type of system, he said, can lead to disorganization and confusion for both the customer and the ITAD provider.
With the CycleLution tracking and reporting system, devices receive a tag that, when scanned, displays information about where the device is going, what type of processing it needs and who the customer is.
The information is available to both the customer and IRT, which will be able to better track any specified device as it moves through the facility. Employees can sign in from anywhere in the world and immediately know the status of a given asset.
“It will just be better communication overall, within IRT and within IRT’s customers as well,” Celt said.
It also allows IRT to potentially serve larger customers who require that type of data reporting, such as big corporations.
More stories about processors
- E-scrap buyer launches AI to recognize circuit board grades
- Company debuts battery-containing device shredder
- Processor responds to e-Stewards eligibility suspension