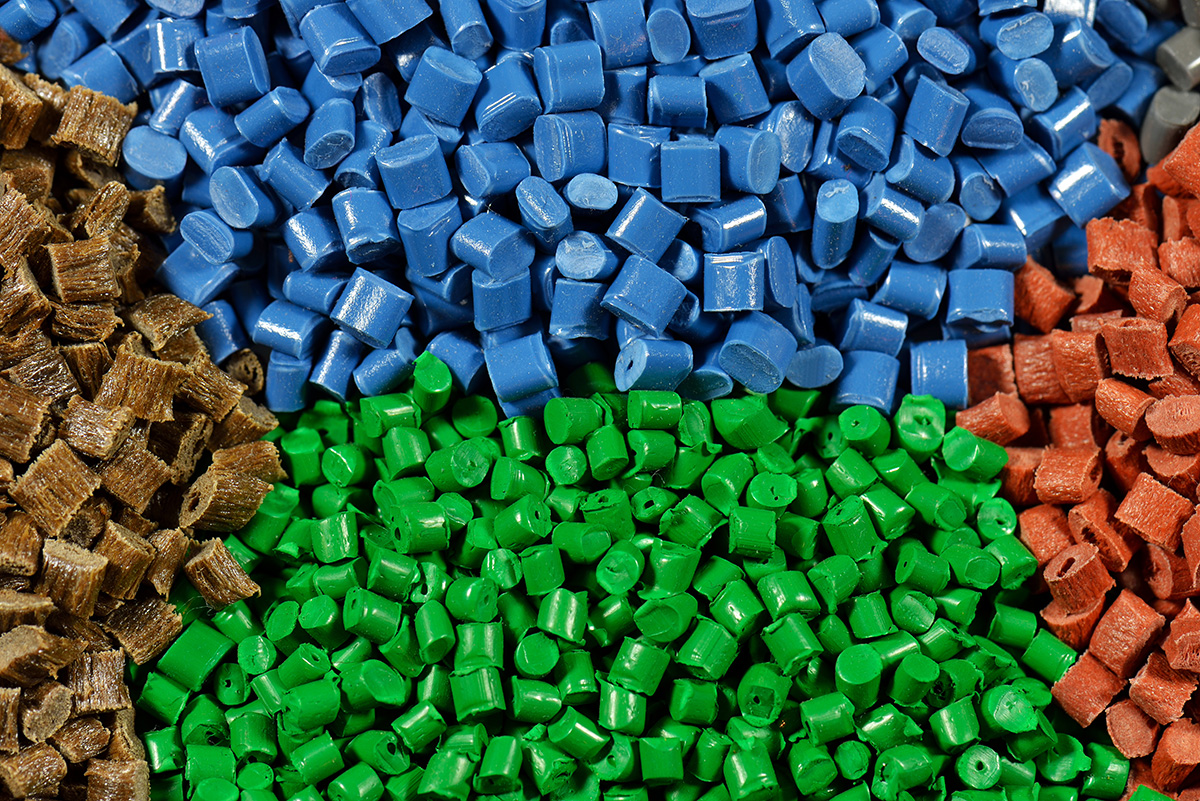
The company’s flagship plant in Ironton, Ohio, is experiencing fewer and less serious issues, amid rapidly growing interest in the chemically recycled resin. | XXL Photo/Shutterstock
Editor’s note: Learn more about food-grade recycled PP and many other topics at the 2025 Plastics Recycling Conference on March 24-26 in National Harbor, Maryland.
Despite recent volatility in the virgin resin market, PureCycle has not adjusted pricing expectations for its recycled PP, CEO Dustin Olson said in the company’s quarterly earnings call.
Olson said the company still expects to sell its R-PP at $1.36 per pound. He cited lower utility costs at the Ironton site in Ohio, and startup of the company’s new plastics sorting facility in Pennsylvania for helping offset the challenge of competitively priced virgin resin and rising prices for post-consumer PP bales.
In the end, Olson said pricing for PureCycle’s output is disconnected from virgin resin pricing. “I feel really good about our pricing, really, regardless of where the virgin pricing goes.”
In addition, the company expects to generate revenue from the site’s two co-products, which comprise about 5% of the plant’s feedstock, Olson said. The first, a waxy material consisting primarily of low-molecular weight PP, has received interest from companies producing adhesives for roofing materials and asphalt applications.
The second co-product is a pelletized mixture of PE and ash content. Spokesperson Christian Bruey said in an email that the PE pellets have attracted interest from companies that use black or gray mechanically recycled resin.
In the earnings call, Olson said sales prices for these co-products were in the 22-55 cent per pound range, and proceeds would help lower overall feedstock costs.
Olson called the potential market for recycled PP “enormous,” with the virgin market nearing 200 billion pounds a year globally.
Rigid packaging is the largest North American market for PP, at about 3.8 billion pounds each year, Olson said. Servicing this segment can help PureCycle ramp up production at “attractive unit margins.”
Flexibles and film also present opportunities, he said, and PureCycle has developed a 30% R-PP compound for flexible applications, with two pilot trials in progress and more expected to begin soon. “This is a massive largely undersupplied market with very high demand,” he added.
These and numerous other developments give the company a “tremendous amount of confidence that we can sell out Ironton in the near future,” Olson said. “Success in these trials should accelerate the need for a global expansion as our ability to supply our customers’ stated needs will be constrained.”
Company sees smoother operations
The Ironton facility produced 3.6 million pounds of resin in Q4, with December operating time at a historical high of nearly 70%, with outage frequency as well as severity both decreasing, Olson said.
The Ironton plant recently achieved a sustained feed rate 12,500 pounds per hour, which is 88% of nameplate capacity, but Olson said commercial demand will determine overall run rates and the company currently will not produce excess resin to keep as inventory. “Running ahead of the customer requirements is premature for us,” he said.
The resin quality – both opacity and odor – also is improving, which Olson attributed to the startup of the company’s sorting facility in second-half 2024. He added that Ironton is using “almost exclusively very challenging PCR feedstocks.” The company previously had been using higher-quality curbside PP bales as it worked to refine the new technology.
Third-party certification is in progress, expected to be completed toward the end of the first quarter. The company expects it to apply retroactively to the 7.2 million pounds of finished product and inventory.
Procter & Gamble expands exclusivity licensing
Massive CPG company Procter & Gamble recently granted PureCycle exclusive licensing for its North American operations, and extended exclusivity periods for all other regions. “It’s a pretty strong vote of confidence by Procter & Gamble to us,” Olson said.
P&G developed the PP purification technology and licensed it to PureCycle.
Five P&G applications are currently in the industrial trial stage, and PureCycle aims for full approval in the second quarter, Olson said. PureCycle would then ramp up sales volumes through the end of the year, with an expected 2.5 million pounds of resin in the fourth quarter for use in packaging components of such brands as Old Spice, Tide, Metamucil, Febreze and Cascade. Olson added that there are more than 10 additional applications that are in earlier trial stages.
Automotive sector accelerates
Access to the huge automotive market has traditionally eluded recyclers, even as proposed regulations in Europe and Japan look to include 25% recycled content per vehicle by 2030, Olson said. The high performance and consistency requirements of automotive equipment, as well as paint adhesion, are among the traditional limitations for recycled resin.
To this end, PureCycle recently worked with compounder Washington Penn to make a bumper fascia containing 60-70% recycled PP, currently undergoing safety testing that is expected to be completed later in the year.
Olson said global demand for just one bumper fascia on one vehicle model would account for about 30 million pounds per year, about half of which would be consumed in North America.
In addition to the bumper, PureCycle is fielding other automotive inquiries about interior products such as fiber backing behind the dashboard and carpet fiber, Olson said.
Fiber, souvenir cups adopt PureFive resin
In January, Drake Extrusion placed its first order of nearly 500,000 pounds of the company’s PureFive resin, for making staple fibers and continuous filament yarns used to produce textiles with approximate recycled content of 50%, Olson said. The Virginia facility using the material currently purchases 60 million to 70 million pounds of PP each year, he added, providing opportunity for PureCycle to scale up in the fiber sector.
Fiber applications are especially challenging due to the low tolerance for contaminants, when recycled resins typically contain excessive ash and other contaminants, Olson said.
And in February, PureCycle announced its first commercial product line with Churchill Container, which makes souvenir cups and containers. Olson said professional sports teams in football, baseball, soccer and basketball each use about 50,000-100,000 pounds of resin in souvenir vessels each season. Churchill has received a commitment from one professional sports team and inquiries from more than 10 others, Olson said.
Importantly, “Churchill has seen no pushback from their customers on premium resin pricing,” Olson added.
Expansion plans
Plans for the company’s Augusta site in Georgia – the first to feature two production lines, with potential for eight – were less clear, though Olson acknowledged that the site is “ready to go” and the company had purchased equipment for the two 130,000 ton lines that had long lead times.
“We continue to stand by the time line that we’ve discussed in the past,” he said, adding that success at the Ohio site would lead to better long-term financing rates as well as cash to move the Georgia plant forward.
PureCycle broke ground on the Augusta site in March 2022, expecting to complete the first production line by fourth-quarter 2023, but in August 2023 said it expected to start construction activity by the end of that year.
In January 2023, the company also announced plans for its first commercial-scale plant in Europe, located in Antwerp, Belgium. Olson did not provide an update on the site during the most recent call.
In addition, the company is working on growth opportunities in Asia, he said. In October 2022, the company announced a joint venture with SK geo centric for a PP recycling plant in South Korea, though in October 2024 the arrangement was ended.
“The more commercial success that we can show across a wide variety of applications, the more opportunity we’re going to have to sell to higher value creation customers that can afford to spend a bit more on the product,” Olson said. “And that’s going to give us a lot of flexibility going forward as well as fuel the growth plan for the company.”