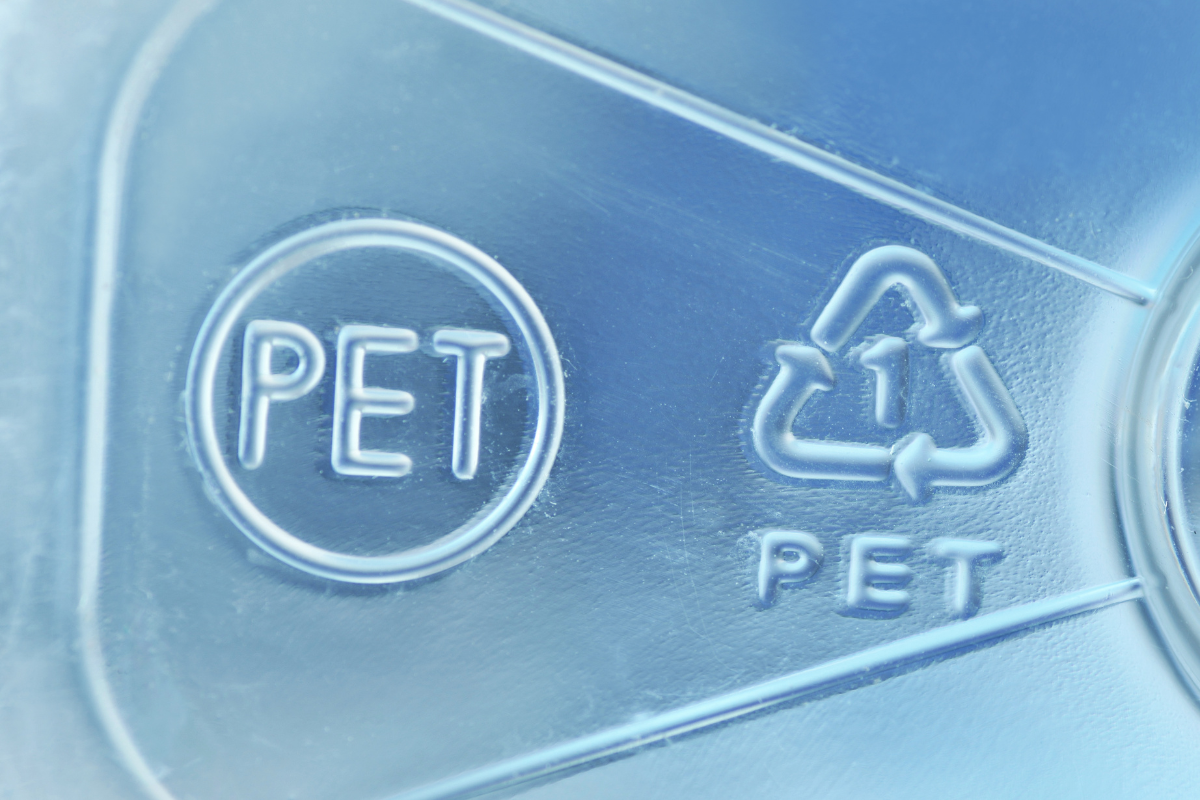
A European Food Safety Authority panel reviewed over two dozen applications to recycle post-consumer PET into food and drink packaging during the past six months. | CalypsoArt/Shutterstock
A food safety scientific panel has approved the use of post-consumer PET recycling technologies from Bandera, Erema, Gneuss, NGR, Polymetrix, Starlinger and others.
Over the past six months, the European Food Safety Authority’s (EFSA) Panel on Food Contact Materials, Enzymes and Processing Aids (CEP) gave the OK to 26 applications to recycle PET for use in new food and drink packaging. In all cases, the input materials are hot washed and dried PET flakes from post-consumer packaging.
In the European Union, recycled plastics can only be used in food and beverage packaging if they’re first reviewed by the EFSA for safety. In that way, the EFSA serves the same role the FDA does in North America.
Twice a year, Plastics Recycling Update covers the CEP’s opinions. The most recent roundup was published in June 2023. The following are CEP determinations that have been published since the last roundup.
NGR technology
The panel approved three applications to use NGR technology to recycle post-consumer PET in 100% RPET packaging.
On Sept. 13, it approved an application from Umincorp Polymers of The Netherlands. Earlier, on June 7, it gave the thumbs up to applications from Coca-Cola HBC of Romania and CCH CIRCULARPET of Italy.
In the NGR process, the PET flakes are dried, melted, mitered and then pumped to a reactor. There, the melt is decontaminated during a melt-state polycondensation process, which includes a vertical reactor and a horizontal reactor (details of the reactor conditions were redacted from the publicly available document). Finally, the melt is cooled and pelletized.
Gneuss processes
The CEP approved a few applications using different PET recycling technologies from Gneuss. On Sept. 12, the panel OK’d an application from Concept Plastics Packaging (CPP) of the United Kingdom.
That CPP application was to use what was dubbed the Gneuss 2 technology. In that process, the flakes are fed into an extruder, where they’re melted, decontaminated and processed into sheets. The MRS extruder has what’s called a vacuum section. The panel’s opinion notes that, in the extruder equipment, the temperature, pressure, throughput rate, rotor speed and satellite screws speed are important to the decontamination, but details of those conditions were not published in the publicly available documentation. The RPET produced can be used at up to 100% recycled content for food and drink packaging, except for drinking water bottles, which would be limited to 90% recycled content.
On July 5, the panel greenlighted two applications to use what’s called the Gneuss 4 process. The submittals were from Sanko Teksti̇l İşletmeleri̇ Sanayi̇ Ve Ticaret A.Ş ISKO ŞB (ISKO) of Turkey and RE–PET Kunststoffrecycling of Germany.
The Gneuss 4 process melts and exposes the plastic to a vacuum, before it is melt filtered and pumped to another reactor. There, melt-state polycondensation occurs and the plastic is decontaminated while exposed to a vacuum. In this step, the amount of surface area exposed to the vacuum, residence time, pressure and temperature are key to decontamination, but details of those conditions weren’t disclosed to the public. Finally, the plastic is extruded and pelletized.
In the Gneuss 4 process, the output RPET can be used at 100% recycled content in any packaging, including drinking water.
Battenfeld’s approach
On Sept. 13, the CEP approved an application from Battenfeld-Cincinnati Germany of Germany to recycle PET into thermoformed packaging.
In the company’s process, the flakes are dried and decontaminated before they’re extruded into sheets. According to a diagram included in the opinion, the flakes are first dried and crystallized in an infrared dryer, where they’re heated and exposed to air circulation. Then, they’re sent to an extruder with a degassing section, followed by melt filtration and extrusion into sheet. Both the drying/crystallization and the degassing steps remove contaminants. The resulting RPET could be used at varying levels, depending on the product in the packaging and the length of time it’s stored. For fruits and vegetables stored up to 30 days at room temperature or cooler, the packaging could contain up to 45% RPET. For soft drinks and beer stored for up to one day (to-go drinks served at public events, restaurants, etc.) the cups could contain 100% RPET. Finally, for trays holding meat for up to 30 days at 6 degrees Celsius (43 degree Fahrenheit), the trays could be made of 100% RPET.
Bandera PURe 15
CEP on Sept. 13 approved an application from Arcoplastica of Italy to use the Bandera PURe 15 technology to recycle PET into 100% RPET packaging.
Very little information was disclosed to the public about that process, but a schematic shows the system does use a hopper, two microwave devices, a heating chamber, decontamination reactors, a vacuum pump and separate silos for food-grade and non-food-grade recycled plastic.
Reifenhäuser technology
The panel on July 6 approved an application from Silver Plastics of Germany to recycle post-consumer PET into packaging with blends of 15% to 100% PCR, depending on the intended application.
Silver Plastics plans to use what’s called Reifenhäuser technology, which involves feeling flakes into an extruder where there is atmospheric degassing and a vacuum pump. The process is called “super-clean recycling,” and the output is sheet.
The intended uses and blends of PCR and virgin PET vary, according to the application. For packaging for meat, fish, marinated grilled food, vegetables and fruit sales kept up to 30 days at 50 Fahrenheit, the thermoforms could be made with 100% PCR. The same is the case for packaging for meat and dairy products held for up to 90 days at 50 degrees Fahrenheit.
For vegetables and fruit stored up to 90 days at 77 degrees Fahrenheit, the packages could contain up to 55% PCR.
For cakes, doughnuts and chocolates held for up to a year at 77 degrees Fahrenheit, the packaging could contain up to 15% PCR.
Finally, for other confections held up to about three years at 77 degrees Fahrenheit, the allowed PCR percentage is 75%.
Slew of Erema and Polymetrix offerings
Over the past six months, the CEP has approved applications to use different recycling offerings from Erema.
First, the panel on June 7 approved one application to use the Erema Basic process, from Dutch company Cirrec Netherlands. In the Erema Basic process, hot caustic washed and dried flakes are fed into a reactor with a rotating device. There, exposed to heat and a vacuum, they are crystallized and decontaminated. The flakes are then moved into an extruder, where they’re melted and the melt is filtered and extruded into pellets. The pellets can be used in 100% PCR packaging, including for drinking water.
The panel also approved four applications that seek to use a line made up of Erema Basic and Polymetrix equipment. Those approvals were for applications from ENVICCO Limited of Thailand (Sept. 12 approval), Loreco Plast Recyclage of France (July 4), Veolia Huafei Polymer Technology (Zhejiang) of China (July 4), and CPE-Contek-Pfeiffer Entsorgungsgesellschaft of Germany (July 4).
The process involves the Erema Basic, as described above, as well as the Polymetrix SSP leaN technology. The output pellets from the Erema extruder are crystallized and fed into the Polyetrix system. Then, they’re preheated under inert gas flow before they’re sent into the solid-state polycondensation (SSP) reactor (the SSP reactor operating conditions, such as temperature and pressure were redacted from the public document). The resulting pellets can be used in 100% PCR packaging, including bottles for drinking water.
On Sept. 13, CEP approved four applications to use what’s called Vacurema Prime. They were from Ambiental de Plasticos Recyclapet of Colombia, Acepolymer of South Korea, Shangrao Bisource Technology of China and Poly Recycling of Switzerland.
In the Vacurema Prime process, the flakes are crystallized and decontaminated under high temperature and in a vacuum in twin batch reactors. Then, the reactors alternate feeding flakes into a continuous reactor using high temperatures and a vacuum. Finally, the flakes are melted in an extruder, solid contaminants are filtered out and the plastic is extruded into pellets. The resulting pellets can be used in 100% PCR packaging.
Finally, the panel approved two applications seeking to use Polymetrix technology alone. Those July 4 approvals were from Plastrec of Canada and PT Veolia Services Indonesia of Indonesia.
In this process, the flakes are extruded to pellets, which are fed to a reactor in which they’re crystallized and heated up to the temperature of the SSP reactor. Then, the crystallized pellets are fed into the SSP and exposed to high temperatures and a counter-current of inert gas flow for a set time period. The application notes that two different combinations of temperature and residence time can be applied, depending on the desired intrinsic viscosity of the RPET. The resulting pellets can be used in 100% RPET packaging.
Two different Starlinger technologies
On July 4 and July 5, the CEP approved applications from PT Langgeng Jaya Plastindo of Indonesia and CERSA–Compañia Ecuatoriana de Reciclaje of Ecuador, respectively, to use Starlinger deCON technology.
The deCOn process involves preheating flakes in batch reactors up to the temperature of the next step, the SSP. There, the flakes are exposed to high temperatures and a combination of vacuum and gas flow. In this process, the output is decontaminated flakes, which can be used at up to 100% PCR in packaging.
Finally, the CEP considered applications to use the Starlinger IV+ technology. The applications, which were all approved on July 4, came from PCR Ambalaj of Turkey, Tanrikulu Plastik Sanayi Ticaret of Turkey, Dialog Diyou PCR of Malaysia and Lerg-Pet of Poland.
In this process, flakes are dried and crystallized in a reactor under high temperature and air flow. Then, the flakes are fed into an extruder, where they’re heated, exposed to a vacuum and pelletized. The pellets are then sent into a continuous reactor, where they’re crystallized under high temperature under atmospheric pressure. Finally, the crystallized pellets are preheated in a reactor before they are introduced into a semi-continuous SSP reactor, which is running under vacuum and high temperature. The resulting pellets can be used in 100% RPET packaging.