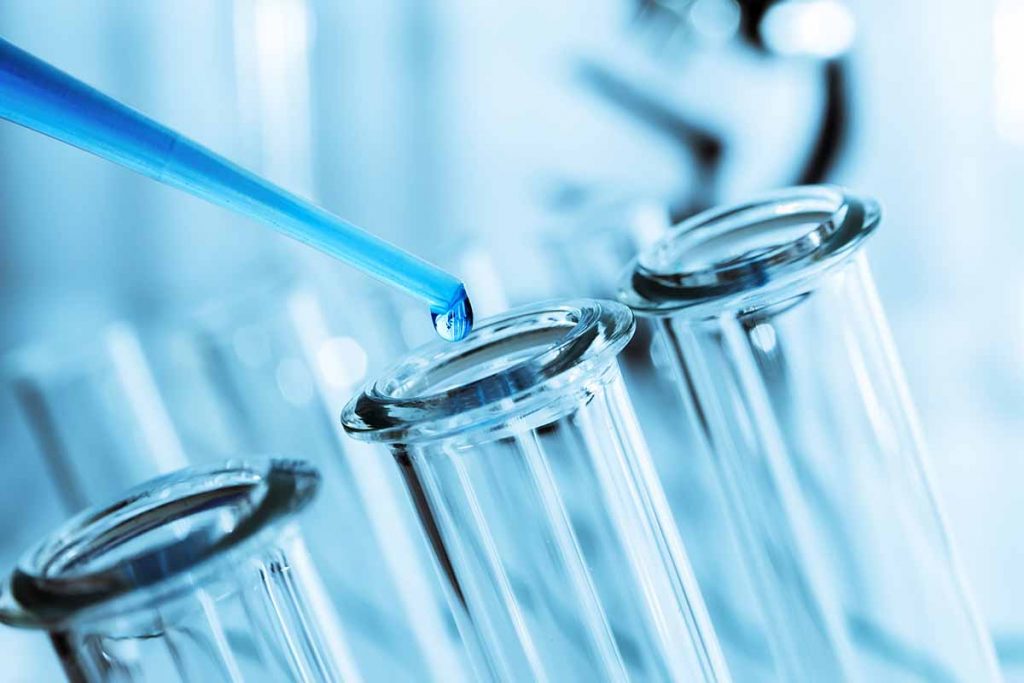
New developments in film and resin technology advance efficiency and circularity goals. | Alex Traksel/Shutterstock
Several companies have released new products that are pushing plastics recycling forward, including PCR-specific additives and 83% recycled content films. Here’s a roundup of innovation news.
Additives for PCR
Avient Corporation recently introduced a PCR Color Prediction Service for polyolefins and PET resins and a polyolefin antioxidant called Cesa Nox A4R Additives for Recycling.
The additives are specifically designed to make it easier to work with PCR in packaging, while the color service helps brands figure out what colors are possible based on the amount of PCR used in the product. This includes calculating how much PCR can be added to an existing application without affecting the signature color.
“Avient is fully committed to increasing opportunities to expand the use of recycled polymers, addressing any barriers that arise either during the recycling process or when customers want to incorporate PCR content into existing or new applications,” said Norbert Merklein, vice president and general manager for the Europe, Middle East and Africa regions of Color, Additives and Inks at Avient.
The color service uses a proprietary software to measure resin characteristics, “avoiding time-consuming trial and error,” a press release said.
“By speeding the evaluation process, the service also gives greater flexibility to customers that may need to switch from one PCR content source to another, which is especially important due to today’s supply variability,” the press release said.
The additive helps protect post-consumer polyolefins against oxidation and can either be added early in the recycling process or incorporated into virgin resin to prepare it for future recycling, the press release said.
Teknor Apex adds products
Teknor Apex launched a new thermoplastic vulcanizate, Sarlink R2 3180B TPV, that has 25% post-industrial recycled content.
The product is intended for use in applications that require elasticity and long-term performance, such as extruded seals and hoses or molded gaskets. It is also recyclable.
The new grade is a pre-colored black, high-durometer multi-purpose TPV “that is essentially the functional equivalent of its virgin counterpart in terms of processing and performance,” a press release said.
“The use of recycled content helps to promote a circular economy while decreasing reliance on virgin fossil-based resources and energy,” the press release said. “This allows brands to meet consumer and regulatory demands for enhanced sustainability of their products and contributes toward a lower carbon footprint.”
Teknor Apex plans to launch softer grades and more specialty TPV formulations with sustainable content later this year.
Recycled content packaging for food contact
Grounded Packaging launched RE: MONO, a recyclable, flexible film laminate made of 83% recycled materials.
According to a press release, the product contains the highest volume of post-consumer recycled content currently available in the world for food contact pouches and other flexible packaging formats. It’s a mono-material LDPE that is circular, meaning it can be recycled into the same material.
“For years, converting a high percentage of post-consumer recycled content into film and having it meet food contact certification standards has been thought to be unachievable – particularly so while maintaining quality and cost,” the press release said. “Grounded has been working with partners to control sourcing, material sortation and blending within their post-consumer recycled material to achieve a higher quality product fit for food contact within all their products.”
A new gasification process
Scientists at the Chalmers University of Technology in Sweden have developed a new gasification process that could replace all fossil raw materials in the production of new plastic.
Henrik Thunman, professor of energy technology at Chalmers and one of the authors of the study, said there are enough carbon atoms in waste to meet the needs of all global plastic production.
“Using these atoms, we can decouple new plastic products from the supply of virgin fossil raw materials,” he said in a press release. “If the process is powered by renewable energy, we also get plastic products with more than 95% lower climate impact than those produced today, which effectively means negative emissions for the entire system.”
The study targeted carbon in plastic, paper and wood, with or without food residues, and heated it to 600-800 degrees Celsius. Hydrogen is then added to the resulting gas. This process “can replace the building blocks of plastics,” the press release said.
“The key to more extensive recycling is to look at residual waste in a whole new way: as a raw material full of useful carbon atoms,” Thunman said. “The waste then acquires value, and you can create economic structures to collect and use the material as a raw material worldwide.”
The researchers calculated that if the energy to power the process can be taken from renewable sources, they will be more energy-efficient than the systems in use today. There is also the possibility of using the excess heat from recycling processes in a circular system for other projects.
The study was published in the Journal of Cleaner Production. It was funded by the FUTNERC project, in collaboration with Swedish plastics manufacturer Borealis.
More stories about film
- Major plastic initiative sets sights on system change
- Research, programs improve film recycling access
- Google, Dow partner on AI to identify recyclables