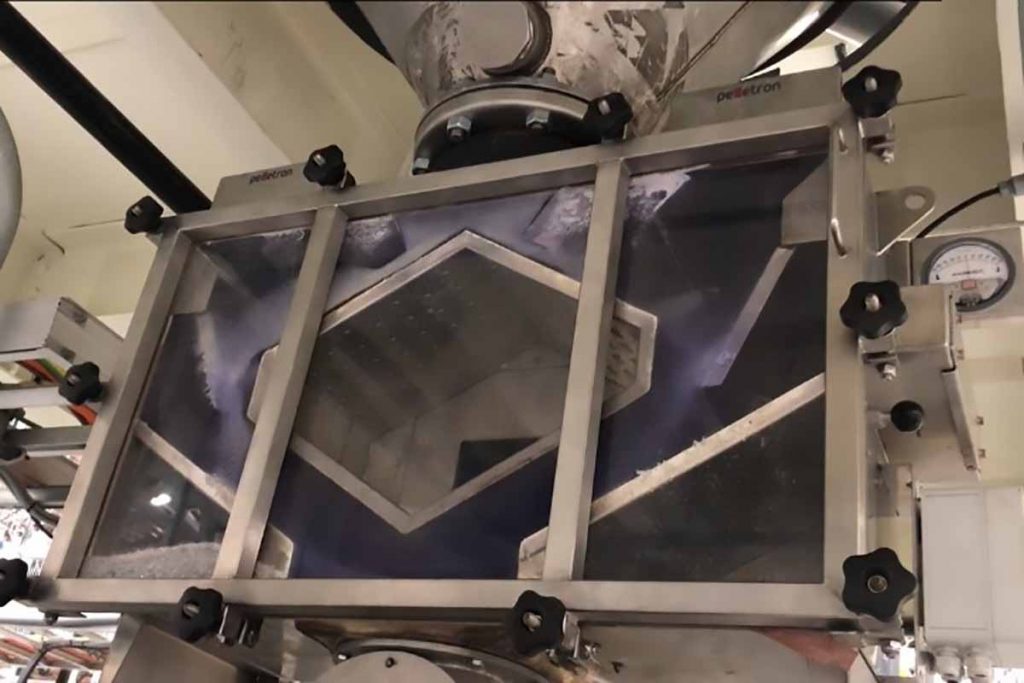
The three XP45 DeDusters that Pelletron sold to rPlanet Earth each have a capacity of 2 metric tons per hour. | Courtesy of Pelletron
Specialized equipment is reducing the presence of gels in rPlanet Earth’s RPET sheets, allowing the Southern California-based reclaimer to sell them for higher prices.
Equipment supplier Pelletron wrote about how its DeDuster system, which removes dust from RPET flakes before they enter the extruder, cleaned up rPlanet Earths’ sheets, which are sold for use in thermoformed packaging.
Located in Vernon, Calif., rPlanet Earth opened a 300,000-square-foot-plus integrated PET bottle recycling plant in late 2018. The facility processes flakes directly into extruded sheets and injection-molded bottle preforms, sidestepping the PET flake or pellet markets altogether.
Lancaster, Pa.-based Pelletron supplied the material-handling systems that move flakes from the wash line to the extruder and injection-molding machines. Soon after the plant opened, the problem of gels in extruded sheets began to emerge, according to the release, which noted that rolls of sheet with too many gels must either be recycled internally or sold at discounted off-spec rates.
Pelletron installed a DeDuster system that uses an electromagnetic flux field coil, which disturbs the fine dust that sticks to flakes due to static electricity, then employs a counterflow air current to remove it. The three XP45 DeDusters sold to rPlanet Earth each have a capacity of 2 metric tons per hour. They were installed on each of the company’s three Welex sheet extruders, right at the extruders’ inlets below the feeders.
A post-installation study on one line found the system reduced the incidence of gels from 1 per 1 meter of sheet to 0.17 per 1 meter of sheet. “That was on spec so the material could be sold at prime rate,” the release notes.
More stories about technology
- RIT researchers develop AI-based textile recycling system
- Industry nuance is key in adopting emerging technology
- Google, Dow partner on AI to identify recyclables