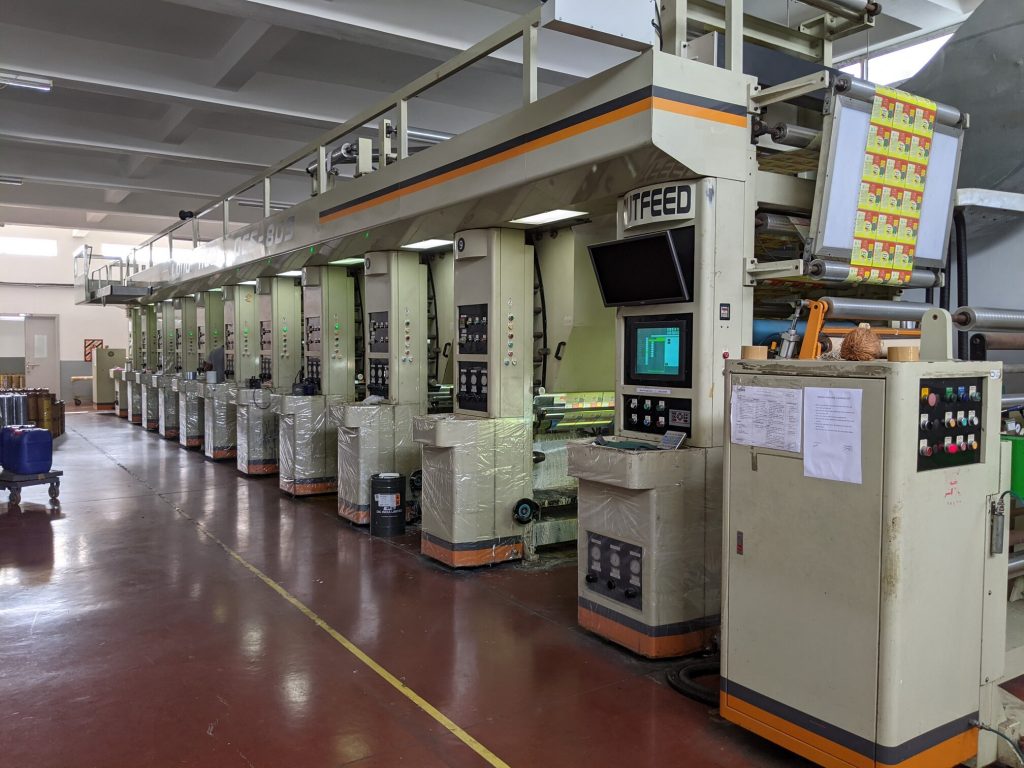
As part of the pilot project, Magnomer’s magnetizable inks were printed on shrink labels in collaboration with American Fuji Seal. | Courtesy of Magnomer
A startup that supplies an ink allowing shrink sleeve labels to be separated from PET flakes with a magnet has successfully completed early testing of the innovation.
Ravish Majithia, founder and CEO of Watertown, Mass.-based Magnomer, told Plastics Recycling Update his company completed the first phase of a pilot project involving labels company American Fuji Seal, a major beverage brand, and independent testing lab Plastics Forming Enterprises (PFE). He could not disclose the name of the beverage brand.
Magnomer developed magnetizable inks that allow reclaimers to remove labels with magnets, which are already used to ensure ferrous metals don’t contaminate flakes or get into extruders. Magnomer’s inks can be produced in various colors or as a transparent ink, and are applied with standard label printing equipment, Majithia said.
Well-suited to existing label systems
While the technology has the potential to enable separation of any types of material for recycling, Majithia said, this particular project tested the ink on shrink sleeve labels on PET bottles.
Most shrink sleeve films are made of PETG, which sinks with PET flakes in float-sink tanks. The PETG can cause flake clumping in dryers, and inks on the labels can bleed and stain the clear flakes.
Companies have developed label films to address those issues, including polyolefin films that float, crystallizable films that can be recycled along with the bottle, and de-seaming labels that separate in the whole bottle pre-wash.
Still, adoption of recycling-friendly labels has been slow in some cases. Majithia said the label industry is familiar with and has equipment set up for PETG, which has good shrink properties.
“There’s a host of reasons why the industry isn’t able to move away from PETG and move to some of those other label technologies,” he said.
In the pilot project, several thousand bottles with PETG shrink sleeve labels were produced by American Fuji Seal for the unnamed beverage brand using Magnomer’s ink.
“On the printing and integration side, we used all high-volume commercial equipment to showcase … this can be done at commercial grade without any issues,” Majithia said. “So the scalability has been proven.”
Then, PFE took the bottles through the recycling process, confirming the labels don’t harm the recycling process. Majithia said that the inks are bleed resistant, so they don’t affect the quality of the wash water.
Commercial-scale trials
The first phase of the pilot project kicked off in late spring 2019 and concluded in November 2019. The recycling testing results were submitted to the Association of Plastic Recyclers (APR) in January 2020, he said.
Phase two of the project will involve trials with a commercial PET reclaimer, Majithia said. His company is currently negotiating with multiple reclaimers. The ultimate goal is for commercial PET reclaimers to provide testimonials to APR validating the technology, so that Magnomer can achieve APR’s Responsible Innovation Recognition, he said.
While Magnomer has gotten significant traction with using its inks in shrink sleeve labels on PET bottles, the company is also working to push its technology to other applications, including recycling HDPE bottles, sorting multilayer films, and recycling aluminum cans.
“The technology has applicability in various aspects,” he said.
In terms of HDPE bottles, Magnomer is working with an Australian label manufacturer to showcase the use of the ink in pressure-sensitive labels on HDPE bottles. The labels are often BOPP, which floats with HDPE in float-sink tanks. Using Magnomer’s ink, a magnet can separate HDPE flakes with stuck-on label from clean HDPE flakes. The technology negates the need for an abrasive wash to remove the labels, he said.
The technology could also allow a materials recovery facility (MRF) to separate laminated films, such as chips bags, with a magnet, which is cheaper and more dependable than other types of sorting equipment. That would help remove plastic contamination from paper bales, where films often end up today, he noted.
Additionally, Magnomer is exploring the use of its inks in aluminum can full-body shrink labels. Those labels, along with pressure-sensitive labels, are often used on smaller drink runs, as opposed to the lacquered cans used for huge drink runs.
In aluminum recycling plants, cans are shredded and sent under a magnet to remove ferrous contamination before the aluminum goes into a furnace. When shredded, shrink labels can get tangled together and gum up equipment, according to a report from The Recycling Partnership and the Sustainable Packaging Coalition. In the kiln, they burn, raising the risk of fires and increases the creation of dross, which must be then sent out for additional processing.
To receive the latest news and analysis about plastics recycling technologies, sign up now for our free monthly Plastics Recycling Update: Technology Edition e-newsletter.