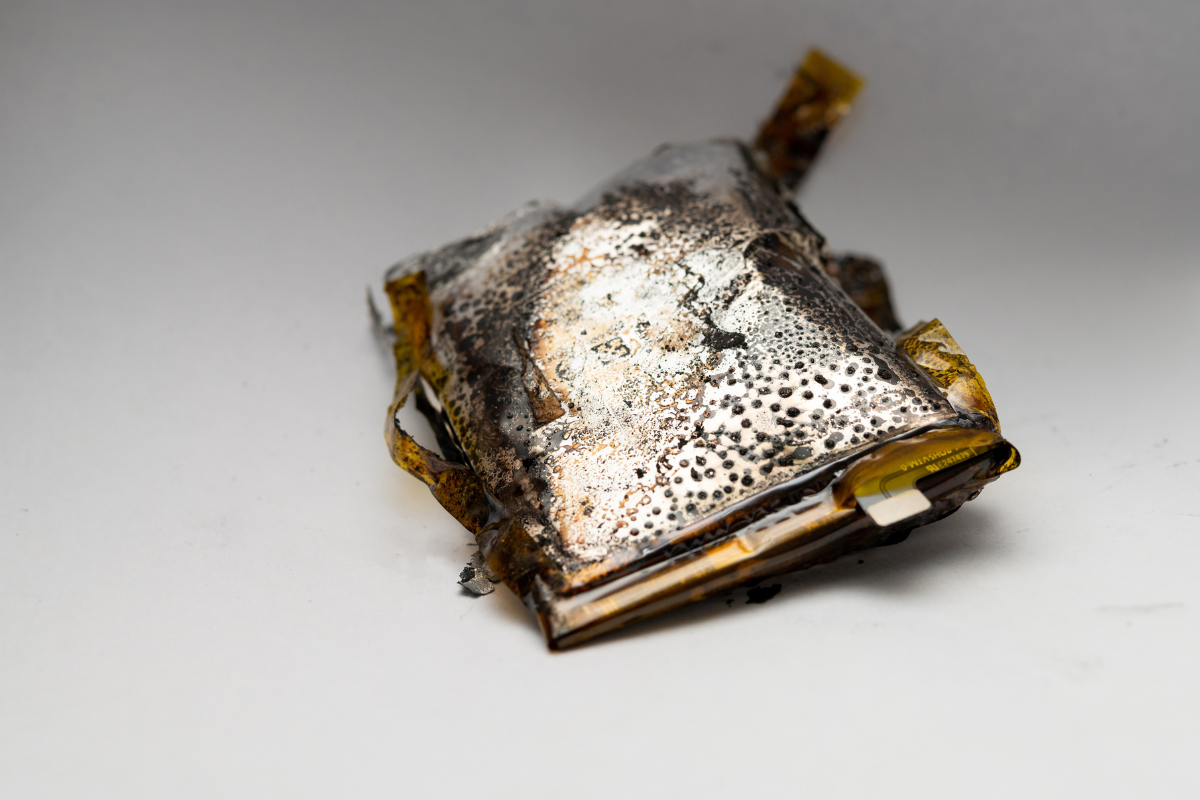
Electronics recycling facility fires have fluctuated widely over the years, but 2024 brought a new high, according to one tally. | PK Studio/Shutterstock
There were 14 publicly reported fires at North American electronics recycling facilities in 2024, representing a 56% increase over the prior year, according to an annual review by fire detection equipment supplier Fire Rover. It’s the highest yearly figure since the company began tracking fire statistics. Continue Reading