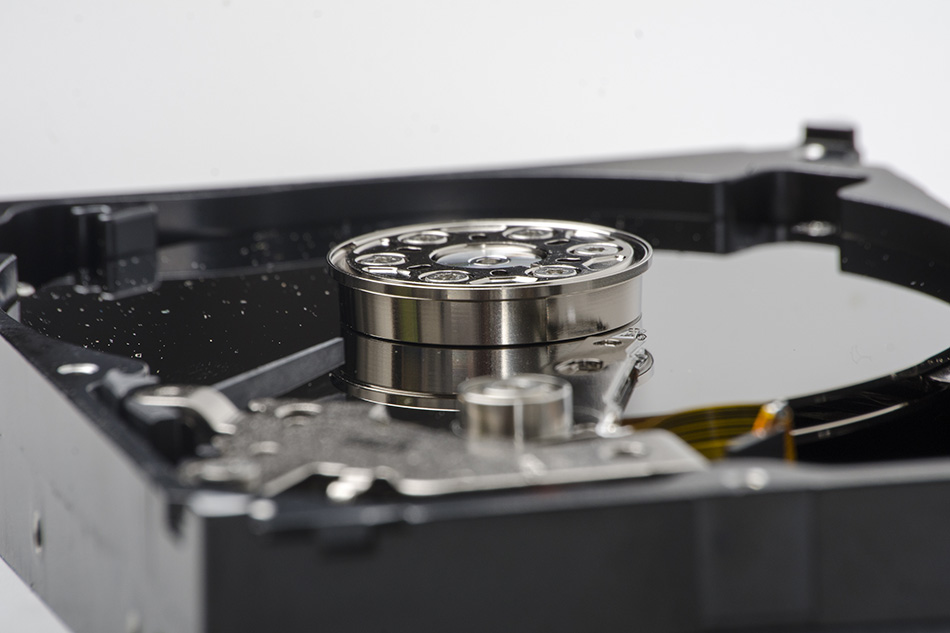
Many of the awarded companies are exploring new ways of recovering rare earth magnets from end-of-life electronics. | stuphipps/Shutterstock
The Department of Energy’s aptly named E-SCRAP prize program has awarded funds to companies engaged in hard drive disassembly, rare earth magnet recovery, hydrometallurgy and e-plastics recycling. More companies are invited to apply this year.
E-SCRAP, a backronym that stands for the Electronics Scrap Recycling Advancement Prize, launched in early 2024 with a goal to help “defragment” the electronics recycling sector. A program representative told E-Scrap News the project fit closely into the federal government’s material sourcing and climate goals.
Last week, the program announced the first round of prize winners, each of whom will receive $50,000 in cash and $30,000 in technical assistance from one of the national laboratories. The awarded projects are:
El Paso, Texas-based Infinite Elements, which has developed “a multistep process, including granulation, mechanical sorting and bioleaching, that allows for maximum recovery and recycling of e-waste that’s made up of mixed materials.” In a description of its process, Infinite wrote that it “uses metal binding peptides to selectively capture” rare earth elements and critical metals from complex mixtures of e-scrap.
Roseville, California-based Garner, which developed the DiskMantler equipment for dismantling hard drives. E-Scrap News previously wrote about the DiskMantler when it was first released for sale. In describing its process, Garner wrote that the equipment “utilizes shock, harmonics and vibration to efficiently disassemble hard drives and SSDs into their critical rare earth components, such as neodymium magnets, printed circuit boards, disk platters, aluminum casings and voice coils.”
Chicago-based Tikal Industries, which was awarded for its Bluerock Filtration system. The company describes it as a technology that can be retrofitted into existing e-scrap processing facilities. Bluerock is “an advanced technology based on a derivative of capacitive deionization designed to optimize the selective recovery of critical materials” from e-scrap, focused on neodymium, praseodymium, cobalt and lithium.
Berkeley, California-based RareTerra, which is developing a bioleaching process to separate rare earth elements from e-scrap in a way that reduces sorting requirements and doesn’t rely on harsh acids. RareTerra says its technology achieves rare earth element separation “without organic solvents through selective bioaccumulation and biomineralization.”
Rancho Palos Verdes, California-based Insource Materials Collective, which was awarded for a project that will recover neodymium-iron-boron magnet powder from e-scrap and have it be recovered in a condition that’s ready for new magnet manufacturing without any additional processing.
Boone, Iowa-based Critical Materials Recycling, which is using acid-free dissolution recycling technology to recover rare earth elements specifically from lower-value e-scrap. Providing a downstream rare earth recovery option for these materials increases their value and incentivizes e-scrap processors to handle more of these feedstocks, the company wrote. Critical Materials Recycling noted it is partnering with e-scrap processors EvTerra Recycling and RecycleForce.
West Lafayette, Indiana-based GaCycle, which has “developed a microorganism-based solution to extract gallium” from common e-scrap materials that contain gallium arsenic or gallium nitride. “The method will yield higher gallium recovery rates than traditional acid-leaching processes,” according to a project description. These substances are included in LEDs, 5G smartphones, 6th-generation wi-fi routers and other products, the team wrote.
The Urbana, Illinois-based University of Illinois at Urbana-Champaign, where a professor and a group of students are exploring electrochemical separation for recovering platinum group metals from e-scrap. The team wrote that its method recovers more than 90% of PGMs and gold from e-scrap and does so with a 99% energy reduction compared to alternative methods.
State College, Pennsylvania-based Intel-E-Waste, for developing a process it calls Recycling E-Scrap with Adaptive Capacity Technology, or REACT. According to a project description, REACT “offers a low-cost, chemical-free and scalable recycling process to maximize recovery of critical materials and plastics from e-scrap.” The project involves partnerships with e-scrap processor Sunnking Sustainable Solutions and PennState.
Cleveland, Ohio-based Galvanix, which is using a “selective leaching process followed by a sustainable molten salt electrolysis process” to recover rare earth elements from hard drive magnets and prepare them for use in manufacturing new hard drives, according to a project description.
This first round of awards make up the program’s incubation phase, which will be followed by a prototype phase of five selected winners receiving $150,000 in cash each and additional technical assistance, then a final demonstration phase of three winners receiving $600,000.
The prize is administered through the department’s Advanced Materials and Manufacturing Technologies Office. In a statement, that agency’s director, Chris Saldaña, said the country’s “current surplus of unrecycled electronics carries valuable potential that can be realized through improving our ability to convert and repurpose those materials.
Saldaña added that supporting new methods of recovering critical minerals from e-scrap “will increase the industrial competitiveness of America’s energy industrial base, fortify America’s energy supply chains, and address the environmental sustainability concerns for a rapidly growing waste stream.”
The second round of funding availability has opened, with applications due in September and the winners announced in October. Both first-round winners and new companies are encouraged to apply.
An informational webinar about the second funding round will be held on Feb. 18.
More stories about research