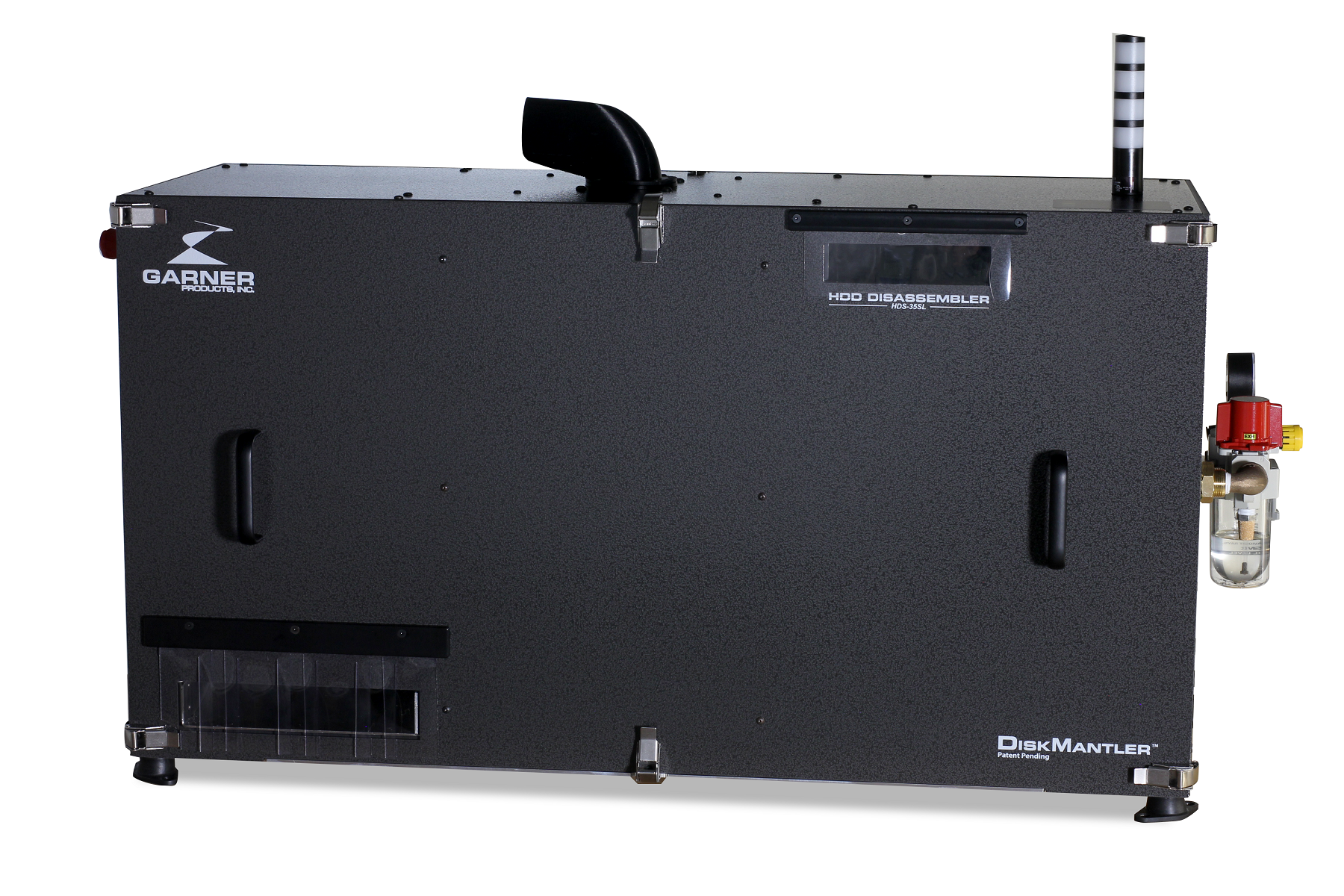
The DiskMantler vibrates hard drives into their component parts. | Courtesy of Garner Products
Recently unveiled equipment from Garner Products dismantles hard drives in roughly one minute using strong vibration, which the company frames as an alternative to shredding in asset recovery.
The DiskMantler is designed to process about 500 hard drives per day, taking in a full drive and separating it into its printed circuit board, rare earth magnet assembly, hard drive actuator and drive assembly. It keeps the plastic, contained primarily within the circuit board, separate from the metals rather than creating a single commingled stream.
Michael Harstrick, chief global development officer for Garner, said the economics will vary, but more separation in general means higher value recovery.
“If I take the drive and separate the PCB board only, I’ve doubled the value,” Harstrick said. Removing the drive assembly and actuator increases that even more, he added.
The rare earth magnet removal – which requires the drive to be demagnetized before dismantling – has the potential to further increase the value recovery. The market for domestic recycled rare earth magnets has yet to mature, but a number of federal initiatives have identified this material stream as high-priority “critical materials.”
Garner manufactures the patent-pending dismantling equipment at its Roseville, California, headquarters. The company released the first production unit that went into a commercial operation at the end of February. Harstrick says the DiskMantler has applications both in ITAD facilities and on-site in data centers. Essentially, it can be installed anywhere it has a stable and large supply of hard drives ready for dismantling.
Developed through an experiment
The concept began when Garner was asked by a client to develop equipment that would just separate the circuit board, attached with sometimes proprietary screws, from hard drives at a data center.
The goal was to be able to remove the component at the customer’s facility. Manual removal, such as prying, was out because of the potential to damage other nearby equipment and for worker safety. So Garner engineers began experimenting with using vibration to jostle the component apart from the drive.
The basic principle, Harstrick said, comes from the studies of German engineer Gerhard Junker, who researched how vibration loosens bolts over time. Junker’s findings led to what’s now known as the Junker test, a standard method to test bolt self-loosening.
For Garner, the principle led engineers to explore vibration as a means to remove hard drive components, taking a different route from previous industry efforts that have used robotics. They built a small box that would vibrate the hard drive, and they discovered vibrating it for as little as 8 seconds at a specified power level would free the component desired by the client.
The client was satisfied, but the engineers decided to experiment with the hard drive being vibrated for longer. “Lo and behold, a minute later, the whole thing came apart,” Harstrick said.
Garner has tested a number of brands of hard drives in the dismantling machine, and despite many variations in product design, the company has found success tackling most drives. It’s a matter of modifying how long the device is left in the dismantler, Harstrick explained.
Most of the variation comes from newer technology leading to design changes. For example, when hard drives shifted from using air to being filled with helium, they no longer needed air vents, and they added a rubber seal that covered the screws. In newer devices, components that were once screwed in are sometimes welded.
“They still come apart,” Harstrick said. “It just takes a little bit.”
A video of the DiskMantler in action is available on Garner’s website.