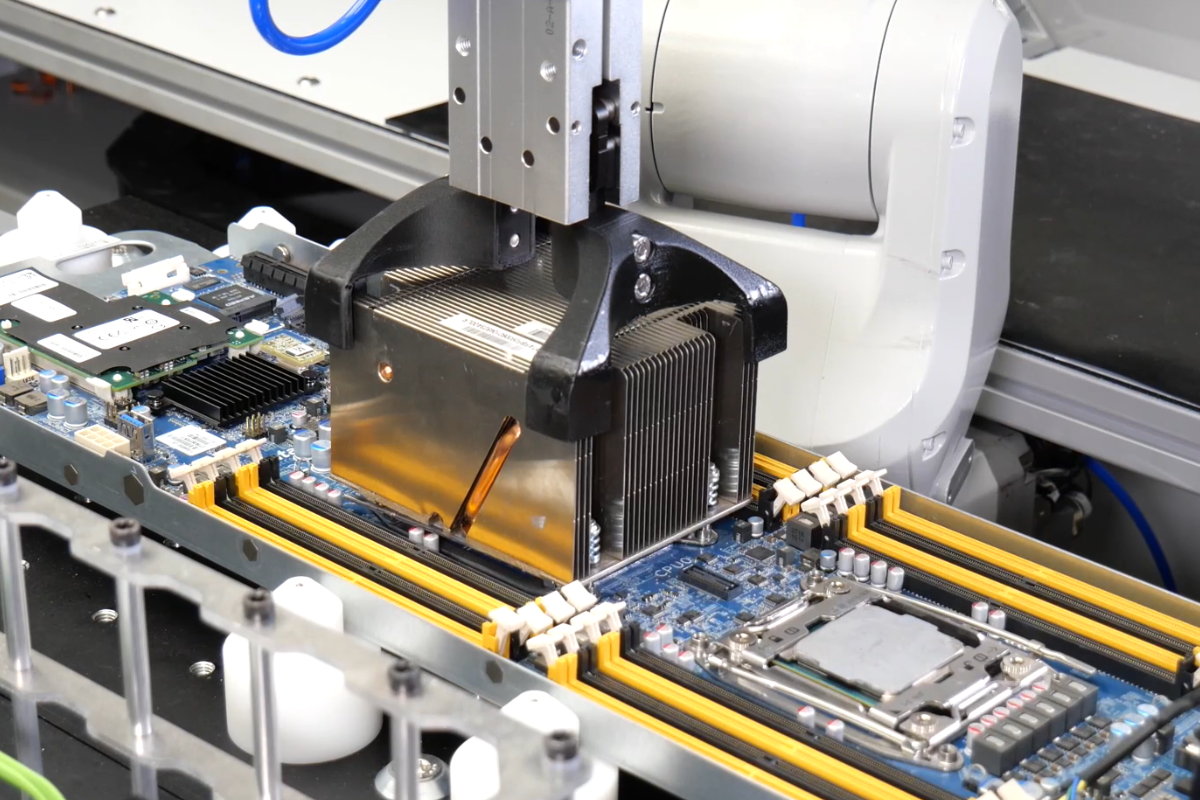
MOLG’s robotic disassembly equipment adds automation to Sims Lifecycle Services’ data center decommissioning segment. | Photo courtesy MOLG
Looking to automate its demanufacturing process, Sims Lifecycle Services has installed robotic disassembly equipment at its data center decommissioning operations.
Sims Lifecycle Services (SLS) last month announced it has installed equipment produced by MOLG, an equipment developer that is focused on automated robotic manufacturing and disassembly systems for electronic devices.
SLS is using the robotic equipment to process hardware retired from data centers. The company has made data center decommissioning a priority business segment in recent years, a move that has proven profitable for the global ITAD firm. It now performs data center processing services at multiple facilities in the U.S.
Data center decommissioning involves retiring IT equipment, performing data destruction and refurbishing, redeploying or recycling the assets depending on their condition.
The MOLG system will provide automation in the disassembly and refurbishment of data center equipment. It uses robotic arms to remove components from devices, and features artificial intelligence and proprietary software to learn from the devices it processes.
Launched in 2021, MOLG features a staff of designers, engineers and other stakeholders who previously worked at consumer electronics companies. In 2023, the company received investment funding from Closed Loop Partners’ Ventures Group, which praised MOLG for “moving the needle on critical mineral recovery through advancing design-for-disassembly and deconstruction.”
Chris Fox, chief operating officer of SLS, said in an interview that the robotic technology will help SLS meet the increasing rate at which equipment is being installed and retired from data centers.
“The challenge the industry faces is scale,” Fox said. “Automation across any industry is there to provide scale.”
Besides being an emerging focus area for SLS, the data center space also presents fewer challenges for an automated demanufacturing process than the traditional electronics recycling stream, which can feature a wide array of device types.
“You get a lot of material coming in that you don’t necessarily have control of,” Fox said of the general electronics recycling stream. The data center world, by contrast, provides a more predictable flow of devices. Starting with a predictable stream will also help MOLG fine-tune its demanufacturing process.
“Automation of demanufacturing is very different than automation of manufacturing,” Rob Lawson-Shanks, CEO of MOLG, told E-Scrap News.
He noted that beginning with data center equipment provides an “infrastructure base of automation” that can be used to further develop automated device disassembly systems for the wider ITAD landscape.