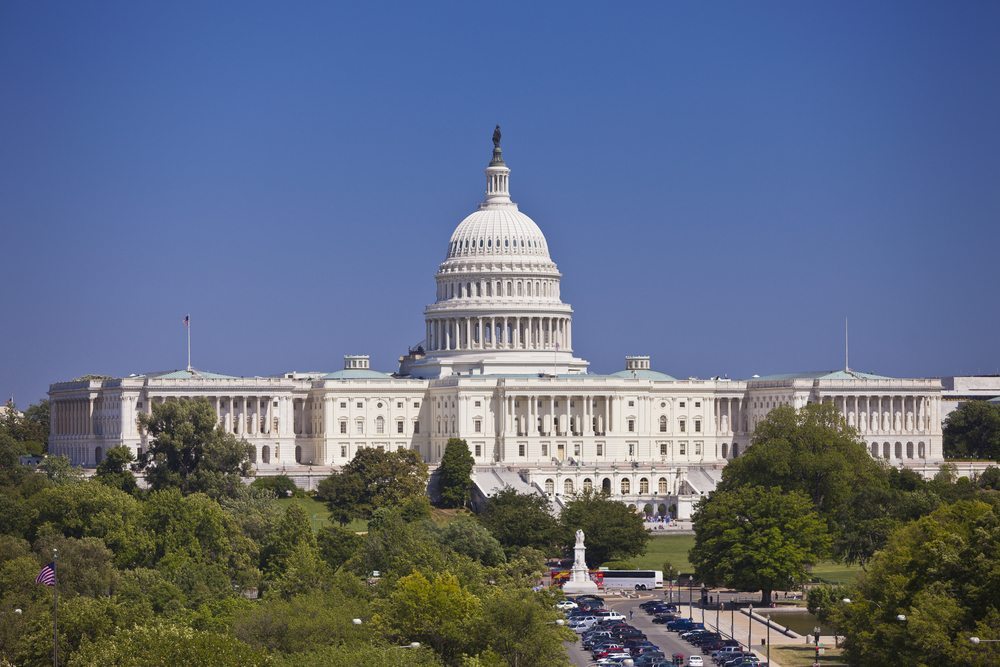
A recent Senate hearing featured discussion around e-scrap metals recovery. | Rob Crandall/Shutterstock
A recent hearing in the U.S. Senate explored the opportunities and barriers in recovering rare earths and other essential components for the next generation of American manufacturing.
Committee on Energy and Natural Resources chairman Sen. Joe Manchin opened the Feb. 7 hearing by saying while government support and intervention are necessary, “industry truly needs to be the leader in securing reliable and ethically sourced supplies for the materials that make up their products.”
Many speakers focused on batteries for electric vehicles, with Manchin noting the International Energy Agency found that stationary and electric vehicle batteries will account for about half of the mineral demand growth from clean energy technologies over the next 20 years.
Duncan Wood, vice president for strategy and new initiatives at the Woodrow Wilson International Center for Scholars, called for policymakers and industry to “work together to find an adequate response to this daunting reality, with priority given to the development of new resources.”
“The recycling of critical minerals has been identified by many, including some in the current administration, as an essential factor in the future of critical minerals supply,” Wood said, but added that “although recycling will play an increasingly important role, materials can only be recycled once they have entered the system.”
JB Straubel, CEO of Redwood Materials and co-founder of Tesla, called for the federal government to reinstate the 48C tax credit to support clean energy manufacturing and for the country to support the collection of lithium-ion batteries for recycling and decrease the export of old battery-powered products.
Straubel said he started Redwood Materials to develop a fully closed-loop, domestic supply chain for lithium-ion battery materials.
While Redwood Materials already gets about 20,000 metric tons of end-of-life lithium-ion batteries annually, or about 60,000 to 80,000 electric vehicles worth, he said if “we were to limit our production to what is available today for recycling, we would not be able to create nearly enough critical battery materials.”
The company focuses on remanufacturing anode and cathode components, and it plans to build U.S.-based production facilities for cathode active materials and battery copper foils. Straubel said Redwood will be able to manufacture enough battery copper foil and cathode active materials by 2025 to domestically produce more than 1 million electric vehicles a year. That number will jump to enough material to supply over 5 million electric vehicles by 2030, he told the committee.
“The transition to electric transportation and clean energy is coming,” he said. “As a nation we must ask ourselves if we want to create the infrastructure and jobs to support that shift here in the United States or allow other nations to develop the manufacturing capacity overseas.”
Pulling the government levers
Joseph Britton, executive director of the Zero Emission Transportation Association, emphasized that he feels critical mineral recycling is imperative to the supply chain.
He also asked Congress to “further accelerate the build-out of a robust domestic critical minerals supply chain by expanding the Section 48 investment tax credit to include energy storage systems like batteries, implementing a production tax credit for battery cells and creating a production tax credit for processing domestic critical minerals for use as battery inputs.”
The Department of Energy does intend to fund battery materials refining and production plants, battery cell and pack manufacturing facilities and recycling facilities, with money expected to be made available in the coming months, the U.S. Department of Energy’s Dave Howell said in his testimony.
Howell is the acting director and principal deputy director of the Office of Manufacturing and Energy Supply Chains and the director of the Vehicle Technologies Office.
He said the Vehicle Technologies Office supports the lithium battery recycling R&D center called ReCell, which focuses on developing “innovative, efficient recycling technologies to profitably recover critical battery materials and reintroduce them into the materials supply chain.”
Congress previously included more than $6 billion to fund domestic battery materials processing, manufacturing and recycling in the Bipartisan Infrastructure Law, Howell noted. He said attention also needs to be paid to developing a “skilled and supported workforce” for the battery industry.
More stories about regulation/oversight
- Wisconsin E-Cycle report reflects increasing access
- Illegal e-scrap imports blocked in Malaysia, Thailand
- Right-to-repair initiative in military gains momentum