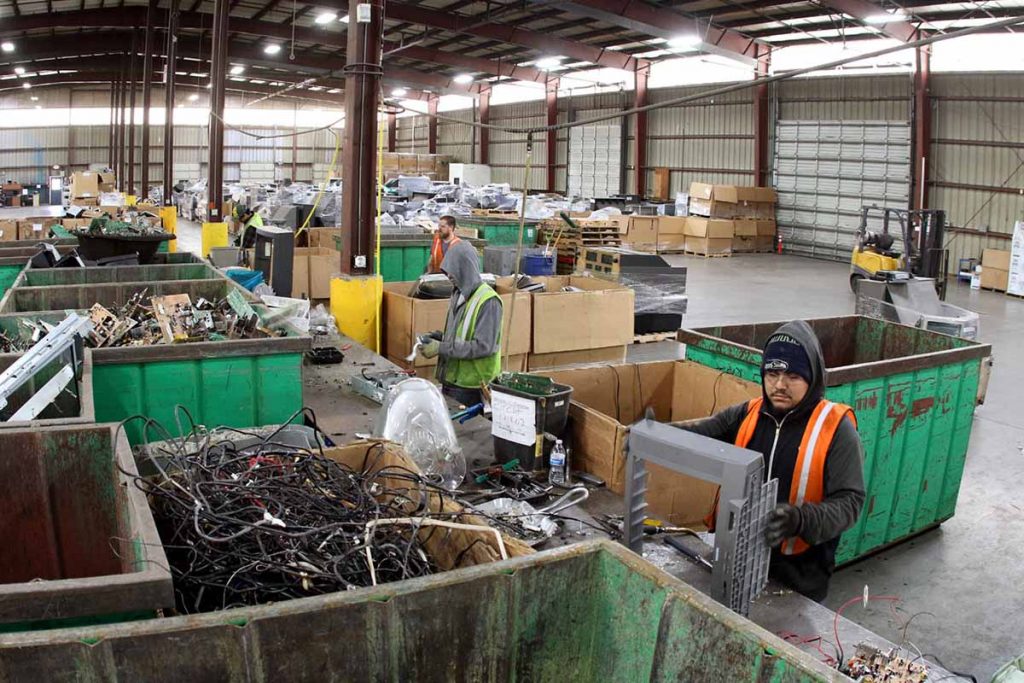
Electronics recycling operations are adapting to the new normal in the wake of the COVID-19 pandemic. | Jared Paben/Resource Recycling, Inc.
E-scrap and ITAD processors nationwide are disinfecting surfaces, changing work stations, modifying the ways they take in material, and more. The goal is to limit employees’ potential contact with the coronavirus.
With more than 400,000 confirmed cases of COVID-19 across the U.S. and regulations limiting daily activities in a growing number of states, electronics recycling operations are adapting to the new normal.
Staffing levels greatly reduced
Most electronics recycling firms have made the determination that they are essential businesses under state and federal regulations. However, most are operating with a quarter of their regular staffing levels, said Kelley Keogh of auditing and consulting firm Greeneye Partners.
Companies are rotating shifts out, meaning there are fewer employees working in the facility at once, Keogh noted, and some facilities are rotating out groups of employees every two weeks.
She said facilities are doing the obvious hygienic measures such as increased handwashing, bathroom cleaning and wiping down door handles. Office employees are working from home at many companies.
Meanwhile, audits for certifications are being conducted virtually for the time being, in accordance with temporary guidance set by certification bodies and standards organizations. Some audits have been pushed out further in the year, Keogh noted.
These and other changes have taken hold in recycling facilities across the country.
No visits, no collection events
At Brockport, N.Y.-headquartered processor Sunnking, changes came quick as the virus began to impact daily life across the state.
“One of our founding principles, if you will, is openness and transparency and inviting people to come see what we do,” said Adam Shine, vice president of Sunnking. But when the virus hit New York, visits by any non-employees stopped altogether.
As the situation in New York worsened, Sunnking began to take a harder look at safety-related changes.
“We identified somebody to clean full-time, all the time,” Shine said. This employee began constantly wiping down and disinfecting desks, cabinets, handles, every common surface in the facility.
Sunnking’s main site is in Brockport, and it recently opened a second facility. Shine said both locations are operating, but the staffs at each site are scaled down and furloughs have occurred.
Employees who don’t need to be at the facility every day are working from home, and the company is using video-call software to keep staff in communication.
Sunnking workers who are still on-site are using masks and other personal protective equipment (PPE), and are practicing social distancing measures. Employees are maintaining at least six feet between one another. The company is also staggering lunch and break times.
Sunnking modified its drop-off collection process at its facility to reduce interaction between the public and employees. In the past, visitors would come to a door and ring a bell, and an employee would come to assist them. Now, the facility has bins outside with signage where people can drop off devices, but there is no interaction with workers.
Inbound volumes are down substantially, but Sunnking is still seeing some public interest in its drop-off option.
When drivers go out to pick up materials, they’re wearing gloves and masks. And the company implemented a precautionary waiting period after reports that the virus can live for hours or days on certain surfaces.
“When we get the material back to our facility, the material will sit there for at least 24 hours before anybody touches it,” Shine explained.
Basic screening on-site
Hyla Mobile, a reverse logistic company that refurbishes and resells phones collected through trade-in programs, has also taken steps to protect employees, including the 230 people who are currently working in the company’s 130,000-square-foot processing facility in La Vergne, Tenn. just outside Nashville.
Biju Nair, CEO of Hyla Mobile, said his company reconfigured work stations to provide six feet of distance between staff members who process phones and aren’t able to work from home. All staff are also required to wear PPE.
The company also created a cleaning crew that goes around and sanitizes surfaces over the course of an entire shift. Once a week, Hyla Mobile pays a professional deep cleaning crew to sanitize the whole facility.
To overcome the challenge of hand sanitizer shortages, Hyla Mobile staff bought a 100-gallon tank of isopropyl alcohol and food-grade aloe vera to make hand sanitizer on-site. The company also implemented automatic temperature scanning at the entrance of the facility to ensure people with fevers don’t enter.
“It’s a noninvasive way of making sure that everybody who is entering the facility is healthy,” he said.
Lunch times have been staggered to reduce employee contact with each other. At the end of every shift, Hyla Mobile brings in extra security and opens up the dock doors and ceiling vents to bring in fresh air for an hour.
Incoming inventory generally takes a week to arrive, providing time for the virus on any surfaces to die off. But Hyla Mobile has started letting incoming inventory sit for an extra day to provide extra time.
‘Skeleton crew’ ensures distancing
In Ontario, Calif., an e-scrap operator noted employee health, not profitability, is the priority.
“My No. 1 goal is to go through the year and none of my employees will catch COVID-19,” said Roy Dann, founder and CEO of Cal Micro Recycling and its CRT-recycling-focused sister company, GLS Group.
Employees who are able to work from home at least part of the time, such as accounting and human resources personnel, are staggering shifts at the office, ensuring only one person occupies a work space at a time.
Staff members who process material manually have to work in the building, but because the company is working with a skeleton crew in a nearly 100,000-square-foot facility, the company can ensure distance between workers, he said.
“And we schedule our lunch hours so no employees have to sit together and eat,” he said.
All employees are wearing PPE when they work.
Because drivers are at risk, Cal Micro has informed its clients that when company drivers arrive at client sites, they will not get out of the truck to help load material. Drivers have masks and gloves, and they’ve been told to sanitize their hands after passing paperwork back and forth.
Dann said feedstock that arrives is a minimal risk, because it has been piled up for some time. But all arriving parcels and paper mail are sprayed with disinfectant. Internal company paperwork is placed in plastic pouches when it’s transferred, and couriers have to wear masks, as well. And no visitors are allowed unless they’re also wearing PPE.
The company provides regular updates to managers about new information coming out, including global infection data.
“We institute new policies and procedures almost on a weekly basis,” he said.
Dann, whose wife is from Wuhan, China and still has family there, has put ample focus on collecting and distributing PPE. After the outbreak in China, he mailed PPE to China, and since then he’s distributed PPE to employees and to area hospitals. Last week, the company donated 400 N95 masks and 30 full-body hazmat suits to health care workers, he said.
“We, as a business, I think we hold a certain social responsibility,” he said. “And we need to do whatever we can to help out the society.”
More stories about processors
- New ITAD firm launches, acquiring two processors
- Makor ERP to incorporate ESG reporting into platform
- Australian metals company rebrands, builds Texas plant