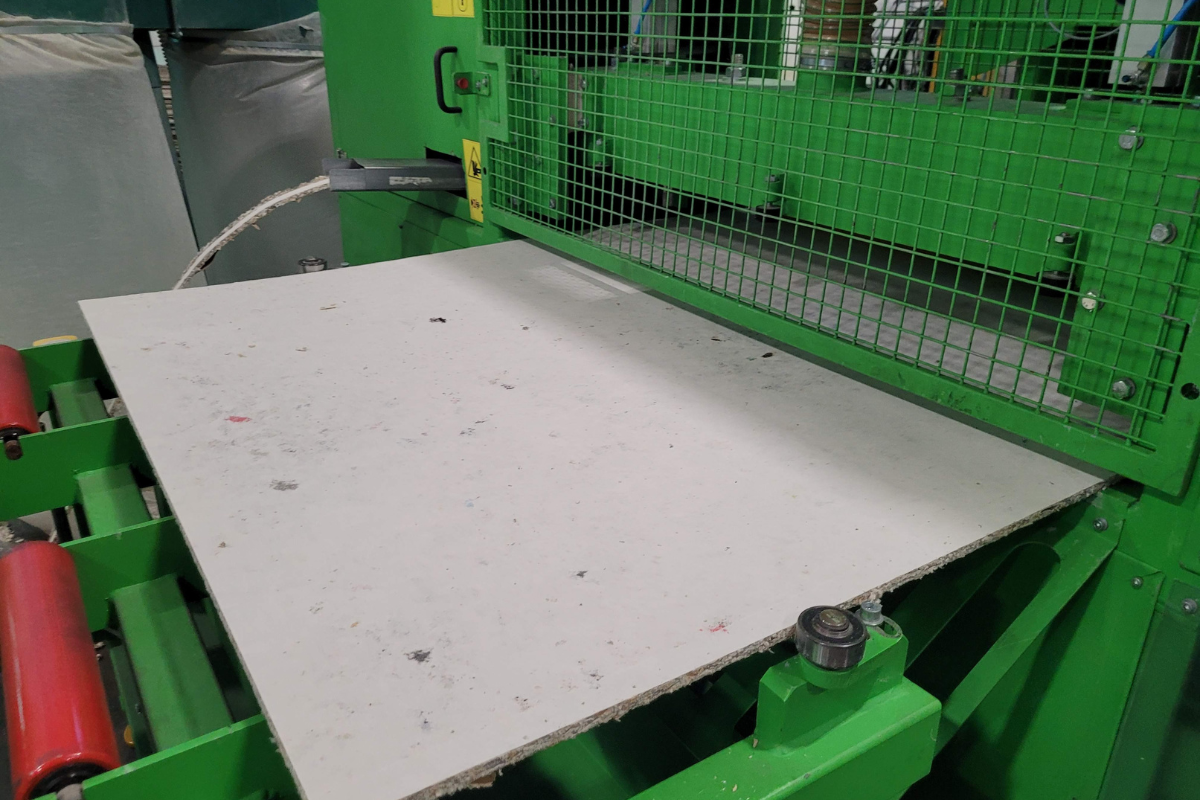
Kelly Green Products’s Connecticut facility is running at full capacity as of November, but the company is already making expansion plans. | Courtesy of Kelly Green Products
Composite board manufacturer Kelly Green Products ramped up to full scale in November and is currently processing 400 tons of post-consumer cartons per month at its Waterbury, Conn. plant.
The company produces a cover board, an alternative to traditional products like plywood, OSB and gypsum board, primarily for roof and wall construction use. Company founder Tom Kelly has been experimenting with using recycled cartons in the board production for about a decade, and Kelly Green Products has been scaling up production at the Connecticut facility for the last few years, with infrastructure grant funding provided by the Carton Council.
The facility is sourcing gable-top and aseptic cartons in No. 52 bales from MRFs in the northeast, Kelly said in an interview. Those cartons are mixed with plastic at a varying ratio based on the desired quality of the end product. The more fiber, the less dense the board, and the more water absorption is allowed. The facility is currently producing boards from a ratio of 70% cartons and 30% plastics.
“There are no glues, adhesives or added water,” Kelly said. The plastic and cartons are combined “homogeneously into a heat-pressed board,” he said.
Facility uses a ‘big panini press’
The process can use a variety of plastic resins, including LDPE, HDPE and even plastics recovered from electronics. The company receives plastics from electrical wiring from a recycling operation located near the manufacturing plant, he said. It can also use PVC, which the company typically receives in the form of recovered roofing membranes.
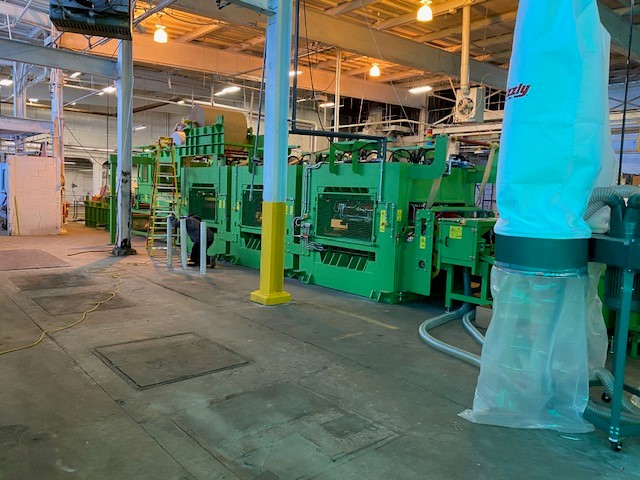
The Waterbury, Conn. plant reached full capacity in late November. | Courtesy of Kelly Green Products
The cartons and plastics are fed into a shredder, where the mixture is size-reduced and fed into a hopper. The hopper feeds the shredder material into a leveler, which has a layer of kraft paper or fiberglass at the bottom with a sheet of polyethylene on top of it. The shredded material is fed onto the polyethylene sheet, until there is a layer of 4 to 5 inches of what Kelly describes as a dry slurry. Another fiberglass sheet goes on top to encapsulate the slurry.
The mixture is brought into a heat press, where it’s cooked at 380 degrees Fahrenheit for several minutes, with the duration depending on how much moisture is in the mixture. Any moisture is expelled as steam out the sides of the press.
“It’s like a big panini press,” Kelly said. The mixture moves through two heat presses and then a cold press, before the boards are cut to size. Depending on its size, each board contains 49 to 63 pounds of cartons.
The company has two heat presses, and each can process about 13 boards per hour. That equates to more than 600 boards per day. The company is currently processing about 400 tons of cartons per month.
So far, Kelly Green’s biggest customer is its sister business, 2001 Company, which does commercial roofing work.
Growth on the horizon
Kelly said the total investment in the facility so far is more than $5 million. The plant is located in an old foundry building on 3 acres of property. The main building totals 50,000 square feet, with additional buildings on the property allowing future expansion. And Kelly has an eye on expanding. He says he’s identified 30 locations around the U.S. where he sees potential for a Kelly Green manufacturing plant. He identified the locations based on proximity to MRFs and potential end markets.
As for the Connecticut plant, although it hit full capacity in the last week of November, Kelly wants to double the capacity with two additional presses, once he gets financing to do so. The shredder already produces enough material to feed the expanded capacity, he said.
Beyond providing another outlet for cartons currently being recovered, new end markets like Kelly Green give stakeholders an opportunity to move upstream and talk with MRFs that haven’t begun sorting cartons, said Jason Pelz, vice president of recycling projects for the Carton Council of North America.
It’s the type of market growth the Carton Council has been emphasizing the importance of especially for the past few years, when carton recycling has faced some challenges: Factors including bale quality concerns following China’s pull-back from the export market and trends related to COVID-19 drove some communities to remove cartons. But with new outlets like Kelly Green, Pelz sees positive signs for carton recovery.
“We’re beginning to see some renewed interest,” he said.