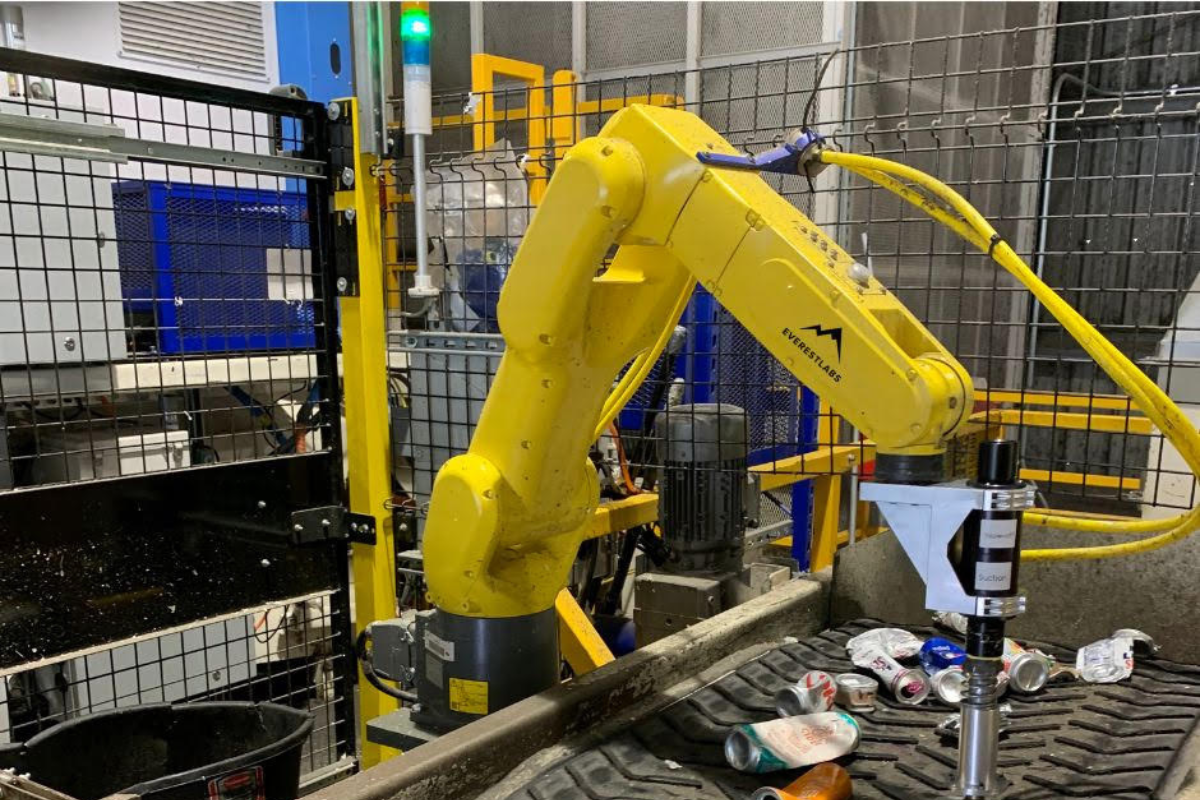
Since making its first sale two years ago, EverestLabs has sold over 50 robotic systems to MRFs and plastics processors. | Courtesy of EverestLabs
Deals with major operators and a partnership with an aluminum group are helping fuel growth for EverestLabs, a relatively new entrant into the business of recycling AI.
In an interview with Resource Recycling, Apurba Pradhan, head of product and marketing for Fremont, Calif.-based EverestLabs, talked about how the company has been commercializing its AI robotics and recyclables-data-capturing systems.
The company has now sold over 50 systems, most of them over the past year, he said. Founded in 2018, EverestLabs had its first sale two years ago.
“In the last 12 months, we’ve had a lot of success in the approach we’ve taken for AI and robots for recycling,” said Pradhan, who joined the company only last year.
Among those successes is a deal with Republic Services, the second-largest garbage and recycling company in North America. EverestLabs briefly mentioned that it was working with Republic in February 2023, at the same time it announced partnerships with West Coast hauler and MRF operator Recology, San Francisco Bay Area-hauler Alameda County Industries, and Pacific Northwest MRF operator Pioneer Recycling Services.
In May, EverestLabs again highlighted its deal with Republic, at the time also mentioning PP and HDPE reclaimer KW Plastics, Southwest U.S. garbage and recycling company Universal Waste Systems (UWS), and Sims Municipal Recycling (SMR), which operates one of the nation’s largest and most advanced MRFs in Brooklyn, N.Y. (SMR is part of Closed Loop Partners’ Circular Services division).
Pick percentage and cost efficiency
EverestLabs is far from the first AI-powered robot company to enter the recycling business.
Among the larger U.S. robot players are Denver-based AMP Robotics, Eugene, Ore.-headquartered Bulk Handling Systems (BHS) and Plessisville, Quebec-based Machinex, all of which have been selling systems to MRFs and other recycling facilities for several years.
EverestLabs’ systems are different from the delta-style robots that most others have rolled out at MRFs around the country. The delta-style robots have three arms suspended above a belt, making them look almost like a spider. (Both BHS and AMP also offer different types of robots for special applications.)
The six-axis arm robots that EverestLabs leases are slower than their delta counterparts, but Pradhan said their percentage of successful picks is higher – typically around 90%. They’re also quicker to install, and their maintenance costs are lower, he said.
For EverestLabs, the robot conversation is focused on MRFs’ last-chance lines, where all facilities are losing some amount of valuable commodities to disposal. With a cost that’s “much less than $100,000 a year,” the robots’ payback can be as short as less than three months, Pradhan said.
“Economically, it’s really a no-brainer at this point,” he said.
One good opportunity for EverestLabs is when private equity firms acquire MRFs, because their focus is on optimizing the MRF and reducing costs.
Part of UBC-focused program
Another opportunity has opened by way of a partnership with the Can Manufacturers Institute (CMI), which has been working to boost UBC recovery around the U.S.
CMI has a can capture equipment financing program for MRFs funded by its members Ardagh Metal Packaging and Crown Holdings. One aspect of this program has been collaborating with The Recycling Partnership on a grant program to pay for UBC-sorting equipment at MRFs. CMI also announced a lease component of this program in May. EverestLabs is in discussions with CMI on being part of this lease program.
Outside of the MRF realm, EverestLabs has made inroads with plastics reclaimers.
Right now, roughly 80% of EverestLabs robots are deployed at MRFs and 20% have been installed at plastics reclaimers, particularly those handling PET, HDPE and PP. But EverestLabs is finding fast-growing demand among the plastics processors. Robots allow processors to buy cheaper, low-grade bales and clean them up so they can still produce high-quality recycled resin, he said.
“[On] the reclaimer side of the business, there’s really clever business cases that the reclaimers can do with robotics that’s helping us get more traction there,” he said.