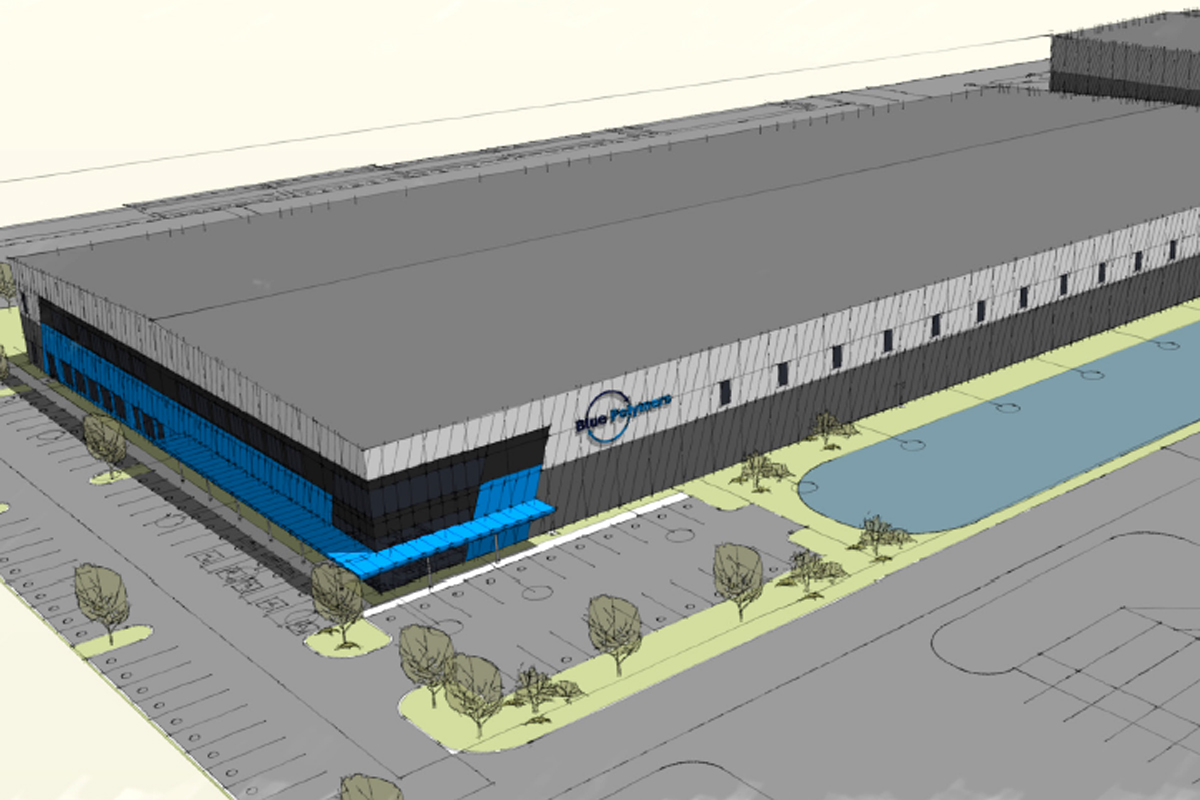
A rendering of one of four Blue Polymers plants that will be built in various regions of the U.S. | Courtesy of Republic Services
Republic Services is moving deeper into plastics processing, launching a $350 million joint venture with a global polymers firm Ravago to produce recycled pellet at four U.S. facilities.
Republic, North America’s second-largest publicly traded waste and recycling business, today announced the partnership with Europe-based plastics production and distribution company Ravago.
The companies’ Blue Polymers venture will be backed by a joint investment of $350 million, with that money being used to build four facilities in several regions of the U.S.
The sites, expected to be operational by 2028, will be fed entirely by Republic’s network of Polymer Center plastic sortation facilities, receiving sorted HDPE and PP and producing recycled pellet.
In most cases, the Blue Polymers plants will be co-located with the Republic Polymer Centers.
The companies say the four sites combined will have the capability to produce 300 million pounds of recycled HDPE and PP annually.
Blue Polymers “will have the ability to custom-formulate drop-in solutions for particular customers,” Pete Keller, Republic’s vice president of recycling and sustainability, said in an interview. “That’s an expertise Republic does not possess, but it’s squarely in Ravago’s wheelhouse.”
Keller said that the venture is 55% backed by Ravago and 45% backed by Republic, meaning Ravago’s investment is just over $190 million and Republic’s is just shy of $160 million.
Next stage of ‘forward integration’
Republic first announced its Polymer Center concept in early 2022.
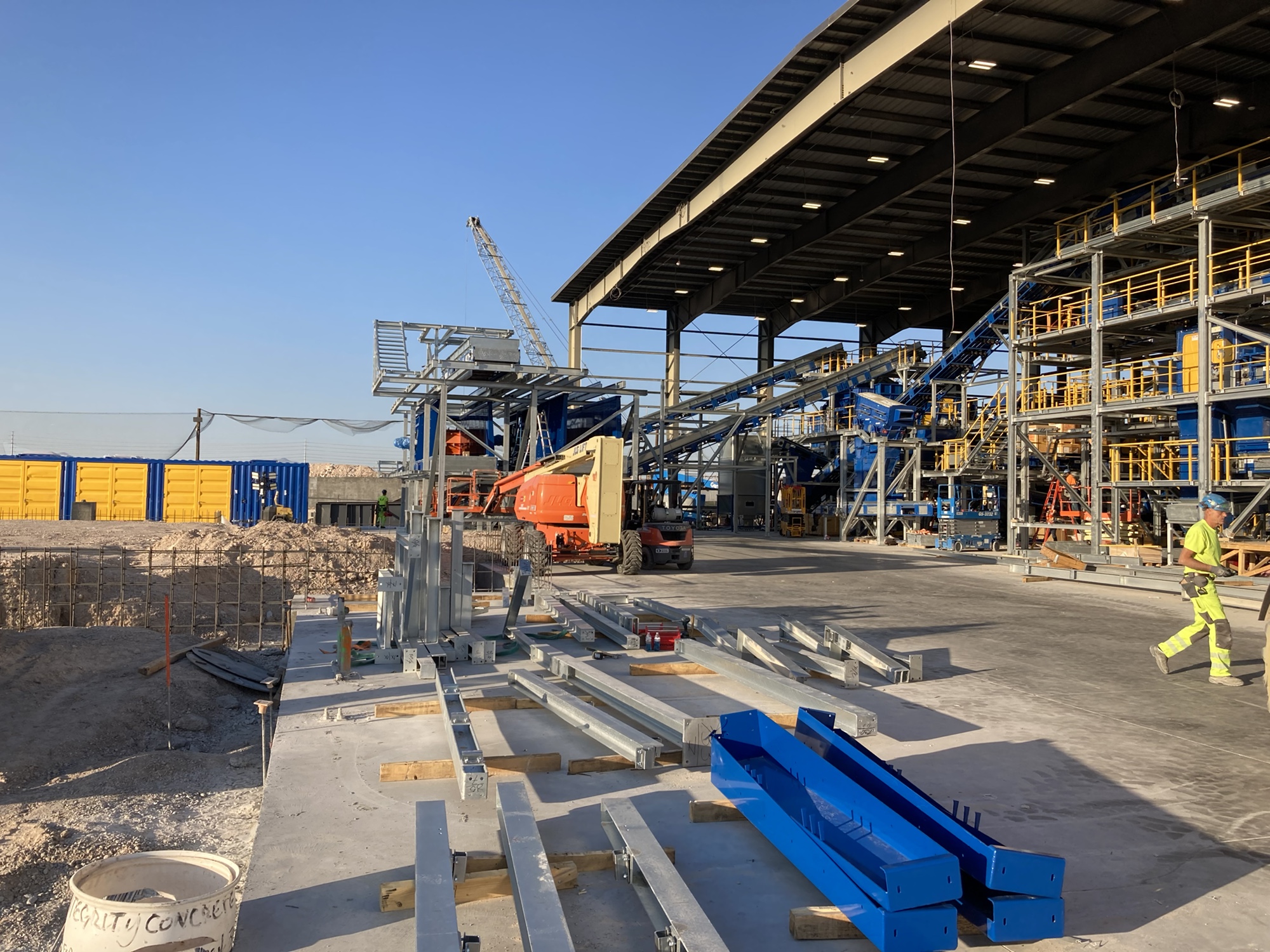
Construction is underway at the first Republic Polymer Center, located in Las Vegas. | Courtesy of Republic Services
The company’s stated plan is to build four sortation plants in various pockets of the country, each with two lines: one dedicated to PET and the other to polyolefins (HDPE and PP).
On the PET side, the Polymer Centers will produce plastic flake for direct sale to end users. In recent weeks, Republic leaders noted the company had lined up a long-term supply agreement with The Coca-Cola Co., its first publicly named customer.
As part of the venture announced today, Ravago will distribute a portion of the Polymer Center PET through its channels.
For olefins, the Polymer Centers are intended to engage in deeper levels of sortation than would be seen at a typical materials recovery facility. They will generate clean loads of HDPE and PP.
It’s this material that will go to the plants being developed by Republic and Ravago.
Keller explained the Blue Polymers olefin sites will engage on another step of sortation, followed by washing, grinding, extrusion, pelletization, purification, formulation, storage and distribution.
Keller said the move into resin production is part of Republic’s strategy of “forward integration,” one being driven by several trends in the marketplace leading to greater demand for post-consumer resin (PCR).
Brands have made commitments to use high levels of PCR, for instance, and more states are beginning to mandate PCR in various plastic applications.
“Minimum content is something we’ll continue to see expand to other states over time,” Keller said.
He added Republic and Ravago are expecting the Blue Polymers venture’s internal rate of return to be around 20%. “This is a good investment profile,” he said.
Ravago is a privately held chemical and polymers company that has been involved in plastics recycling for decades. The company operates 19 recycling and compounding plants across the globe, supplying a wide variety of customers.
“Partnering with Republic Services in the creation of Blue Polymers to provide transparency in the post-consumer recycling process is transformative,” Jim Duffy, president and CEO of Ravago Holdings America, said in a press release.
Keller said leaders at Ravago and Republic first started discussing a potential partnership at the Plastics Recycling Conference in March 2022, shortly after Republic had announced its Polymer Center plan.
Plans to co-locate operations
The first Republic Polymer Center, located in Las Vegas, is already under construction, and Keller said it will have machinery up and running by the end of the third quarter of this year, with an official opening planned for December.
Keller said a Blue Polymers facility will be paired with the Las Vegas site. The company is planning to build that production facility somewhere in the general Las Vegas region (the Polymer Center under construction does not have space for an additional plant beside it).
Republic has noted that its second Polymer Center will be located in the Midwest. At that site and each subsequent build, Polymer Centers will be built with Blue Polymers facilities co-located.
Keller said the first completed Blue Polymers olefin plant will be at the Midwest location, with the Las Vegas Blue Polymers site coming after that.
“We’re actively working out sites three and four,” Keller added. “We’re building out a regional network that will essentially cover us nationwide.”
A growing trend
Market forces around plastics sustainability and recycled resin use have recently sparked projects from a number of industry stakeholders that, like Republic, see opportunity in integration.
Last year, WM, the nation’s largest hauler and MRF operator, acquired Avangard Innovative’s U.S. plastics recycling business, renaming the film-focused operation Natura PCR.
More recently, resin producer NOVA Chemicals announced a plan to build a large plastic film recycling facility in Indiana, in partnership with Novolex.
Though pricing for many grades of recycled plastics has been low in recent months, Keller said the long-term market outlook is strong, especially for pellet.
“Recycled pellet, particularly [HDPE] natural pellet, is still trading at a pretty significant premium to virgin [resin] today,” Keller said.
He said the aim of Blue Polymers is to develop recycled resin products that have more value than other recycled materials in the marketplace. He gave the example of the production sites being able to offer a custom color HDPE resin for a particular customer, allowing that customer to move away from needing to purchase natural resin and then color it themselves.
“We are hearing from customers what they’d like to purchase and we’re bringing those materials to the market,” Keller said.
A version of this story appeared in Plastics Recycling Update on July 31.