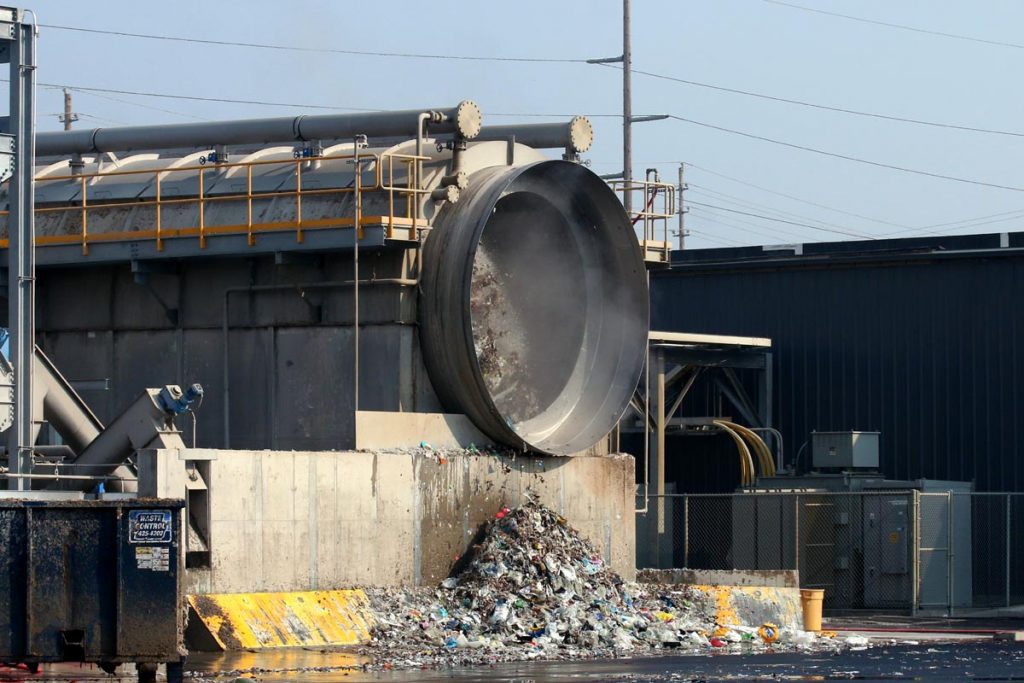
Contamination, including a lot of rigid and film plastic, falling from NORPAC’s new drum pulper, which recycles OCC and mixed paper.
| Jared Paben/Resource Recycling, Inc.
When National Sword hamstrung export markets for fiber bales and U.S. paper plants began announcing plans to expand their recycling capacity, I remember periodically hearing frustration at the seemingly glacial pace of mill upgrade projects.
Now I get it. Or at least I have a little more insight into the complexity, scale and cost of those paper plant projects and understand why they can take so long.
Last week, I was on hand at a ribbon-cutting ceremony for one of the more notable paper mill upgrades in the U.S. (certainly from a curbside recycling perspective): North Pacific Paper Company’s (NORPAC’s) $50 million pulping system, which is allowing the Longview, Wash. mill to recycle not just OCC but mixed paper from MRFs.
Mills across the country recycle OCC into brown packaging, but plants hungry for mixed paper are few and far between – for the most part, they have a sign for Pratt Industries out front. The drum pulper and related mill infrastructure recently added at NORPAC open the door to a regional mixed-paper end market for the Pacific Northwest, where recyclers have historically relied on export.
Largest west of the Mississippi
A new drum pulper is at the heart of the NORPAC improvement project. Supplied by Austria-headquartered equipment company Andritz and built in China, the massive rotating tube at NORPAC uses water and tumbling movements to recover the pulp from cardboard and paper (to my surprise, the feedstock isn’t shredded first).
The final section of this tube is a trommel with a 3/16-inch screen. Water jets blast the recovered fiber through the holes, separating it from the contaminants, which continue riding through the tube until they fall out the end into a pile.
The pulp is then shot through a long pipe that parallels an access road to the mill, where additional cleaning, screening and thickening/washing occurs.
Before this latest pulping equipment installation, the mill used a de-inking system, installed over three decades ago, to recycle paper, particularly newspaper and magazines. At the time, the system allowed NORPAC to meet demand for recycled-content newsprint.
But the old de-inking system wasn’t efficient at handling packaging and mixed-paper grades coming out of today’s single-stream MRFs. It simply wasn’t designed for the fiber mix and contamination levels we see today.
Overall, the Andritz system has allowed NORPAC to increase its recycling capacity from roughly 300,000 metric tons per year to nearly 800,000 metric tons. Described by NORPAC as the largest waste paper processing facility west of the Mississippi River, the system is creating a local market for post-consumer mixed paper in Oregon, Washington and Idaho.
But the system took years to bring on-line. The project was first announced over three years ago, just before COVID-19 shut down the country, crimped supply chains and led to worker shortages.
But even without the pandemic, these projects are massive and complex. Just consider that the project used 5,100 cubic yards of concrete, 3 miles of pilings, 4 miles of piping and 11 miles of electrical cable, and it required 150,000 hours of design and construction.
(Click the arrows to navigate through the sequence of photos. Article continues after slideshow.)
From contaminated bales to consistent paper rolls
Watching the mill in action, I was left with two notable observations: just how much contamination was falling out of the end of the pulper, and how even and consistent the final rolls of paper are.
Giant piles of residue on-site were filled with remarkable amounts of plastic, with a whole lot of both film and rigid plastic visible. A longtime manager at the mill told me the residue rates can average up to 30%. None of that separated material gets further sorted, and it all goes to landfill.
After seeing the pulper, I got a tour of the inside of the mill, where machines worth hundreds of millions of dollars convert the slurry of pulp into sought-after products. The NORPAC mill has three paper-making machines, with machine No. 1 installed when Jimmy Carter was still president, focused exclusively on brown packaging products (the others also produce printing and writing papers from virgin fiber).
Today, everything going into machine No. 1 is recycled pulp. That machine, a loud, hot, wet behemoth running nearly the length of a massive warehouse (employees have access to company tricycles to travel around the facility), can produce 900 tons per day of paper rolls. The rolls are later converted into corrugated boxes, displays, bags and other paper-based packaging products.
After seeing a giant paper roll marked “Cull Brightness,” which means that the roll would be recycled because the white paper didn’t meet brightness specifications, I asked about the quality control process – whether and how humans check the products. I was then shown an ABB robot moving slowly back and forth along a paper sheet to perform quality control.
Why bother with dirty feedstock
It’s astonishing that a mill would even bother with feedstock this dirty, particularly when it necessitates “cooking” products with specific recipes that blend fiber from the different sources to ensure a consistent end product.
Economics tell another story, however.
Mixed paper is always cheaper than OCC, and right now, it’s really cheap. According to RecyclingMarkets.net, the national average price for post-consumer mixed paper is now negative $1 per ton. Meanwhile, the price for OCC is $40 per ton. Prices for both grades have collapsed with startling speed in recent months.
A NORPAC expert told me they suspected mills were so desperate to meet raging pandemic-era packaging demand that they gobbled up all the bales they could, which certainly explains the sky-high OCC and mixed paper prices we saw a year ago. But that buying spree led to a glut of feedstock and the inevitable re-balancing, I was told.
At the same time, as we’re all hearing, overall consumer demand for products is dropping – even as inflation remains stubborn – contributing to weaker demand and lower prices for recovered commodities.
And then NORPAC will likely get some marketing and PR benefits from getting its hands dirty with mixed paper. Its expanded thermo-mechanical pulping capabilities give the company a sustainability marketing story to tell the public and its customers in the lightweight packaging market.
At the Oct. 19 event, NORPAC CEO Craig Anneberg noted how China’s National Sword led to the landfilling of mixed paper in the Pacific Northwest.
“But here at NORPAC we saw this as an opportunity, an opportunity to meet the growing demand for recycled packaging and to rise to meet the regional environmental challenge,” Anneberg said at the event. “We knew we could do more.”
The ribbon cutting event also included a talk from U.S. Sen. Maria Cantwell, who praised its environmental benefits, as well job-creation impacts.
“I think it’s a lesson for the entire nation,” Cantwell stated. “They created a new market, they created a new opportunity, and they created a lot of jobs here and saved a lot of jobs here in Cowlitz County.”
More stories about fiber
- Associations update bale specs for fiber, plastics
- Fiber sector adapts to tariffs, cost swings
- Graphic Packaging reports rising post-consumer content