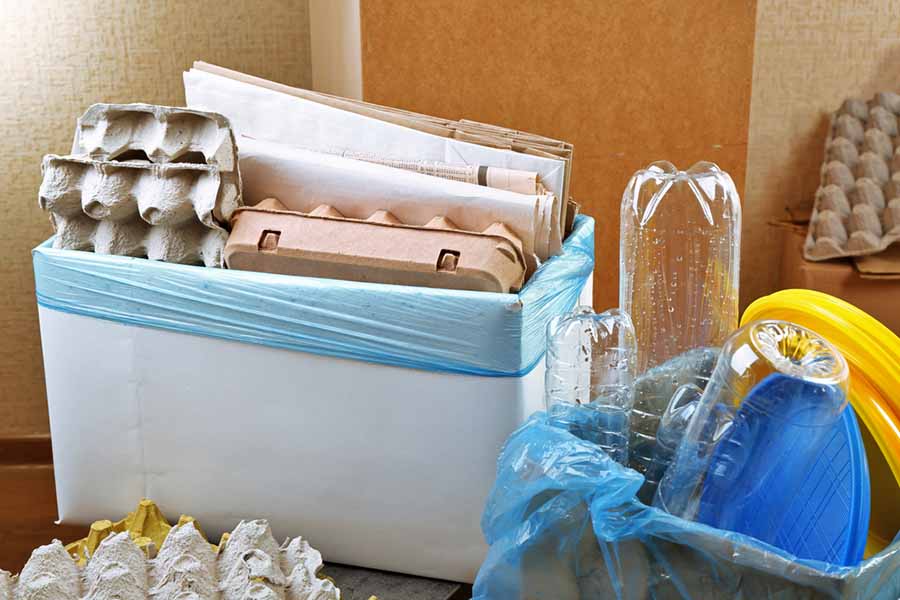
The head of an AI-powered robotics company argues extended producer responsibility legislation focused on material weight will fail to hold producers truly responsible. | Africa Studio/Shutterstock
Colorado’s extended producer responsibility (EPR) legislation, House Bill 22-1355, is a step forward in assuring improvement in recycling – but it is not enough for a state that, according to the bill, “recycled 15% of its waste, which is less than half of the national average,” in 2020.
While we try to make progress, today, EPR is an inaccurate system that will not hold producers responsible for recovering the packaging objects they produce.
The reason? Today’s EPR systems are based on the weight of packaging rather than the number of recyclable objects put into the market. And until every recyclable sold into the market can be accounted for and recovered, we will not truly have producer responsibility.
Weighty considerations
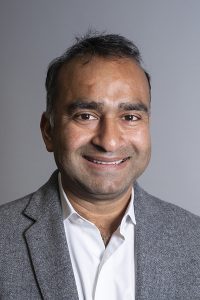
JD Ambati
The Colorado bill describes the obligation of producers in “weight.” A portion of the bill states the following: “Recycling rate means the weight of covered materials that are recycled under the program in a calendar year divided by the weight of covered materials used for products sold or distributed by producers within or into the state in the same calendar year, expressed as a percentage.”
On May 5, New York introduced its own EPR bill, A10185. It was the second New York bill, with S1185 being introduced in 2021. Both bills measure recycling in weight.
Other state legislative EPR initiatives require that producers pay for a portion of the cost of recycling based on weight. EPR bills in Maine and Oregon became law last year. States that are considering or have recently considered EPR bills include California, Hawaii, Maryland and Massachusetts.
The California bill describes the problem facing America, and for that matter, the world: “The United States alone discards 30 million tons each year. Global plastic production is projected to more than triple by 2050, accounting for 20 percent of all fossil fuel consumption.”
How many more objects will result from this tripling? Can our recycling systems manage the number, not the weight, or will it continue to be overwhelmed?
Separately, American Beverage (formerly the American Beverage Association) has been running 30-second commercials under its Every Bottle Back initiative. The campaign notes that America’s beverage companies are “making 100% recyclable bottles and caps and working hard to ensure they’re recycled and remade into new bottles.”
While bottlers may have the best intentions, they are operating in a recycling system that is not yet able to assure 100% of bottles are recycled and recovered for making new bottles or cans. In fact, according to the EPA, in 2018, “the recycling rate of PET bottles and jars was 29.1 percent.”
A technological tracking solution
We have the technology to track down bottles and cans to the object level. Every consumer packaged goods (CPG) brand knows this detail. Look no further than their annual reports that report how many unit cases of “X” have been sold. These are all inventoried at manufacturing sites and distribution warehouses. Retailers like Walmart, Whole Foods and others have the technology and systems to account for every unit case of 24 individual bottles sold.
It’s time to move away from weight-based criteria as a measure of success in the recovery and recycling of packaging.
Consider that there are “more objects per pound” in the market with new manufacturing technologies. It dramatically impacts recovery at recycling plants. According to the American Chemistry Council, in the last 45 years, the 2-liter plastic soft drink bottle has gone on a diet, from weighing 68 grams to just 47 grams today, representing a 31% reduction per bottle. That reduction saved more than 180 million pounds of packaging in 2006 for just 2-liter soft drink bottles. The 1-gallon plastic milk jug has undergone a similar reduction, weighing 30% less than it did 20 years ago. But none of this weight reduction resulted in fewer soft drink bottles or jugs processed in recycling plants.
The EPA reports that the recycling rate of PET bottles and jars was 29.1% in 2018, and the rate for HDPE natural bottles was 29.3% in 2018. Around a 30% success rate is a failing grade.
If retailers are at the epicenter of retail sales and consumption, then MRF operators are at the center of successful recycling. Recycled objects flow down MRFs’ conveyor belts. We need the MRF operators to be the source to measure if an object is recovered.
It is possible. With the advent of the low cost of computing and fast edge-compute AI, we now can document all visible objects at the MRF level to verify their successful recovery. Documentation empowers MRFs to report the recovery of recyclables back to producers. This continuous feedback loop is necessary for a circular system. While this process is not 100% error-prone, this is a good start.
Recovery data from the MRFs can help producers make informed decisions about steps to meet business goals such as environmental, social and governance (ESG), EPR, building brand equity, consumer awareness and loyalty, supply chain efficiency, and others.
Until we execute on easy-to-implement AI systems and use modern technologies, governments and society are asking producers and MRF operators to do the impossible: Be responsible for recycling without precise measurement.
Producers need to be directly connected to MRFs to know if each container is recovered to meet extended producer responsibility. Until then, meeting states’ goals and American Beverage’s lofty goal of every bottle back is a pipe dream.
JD Ambati is CEO and founder of EverestLabs, a provider of AI and robotic sorting technology.
The views and opinions expressed are those of the author and do not imply endorsement by Resource Recycling, Inc. If you have a subject you wish to cover in an op-ed, please send a short proposal to [email protected] for consideration.