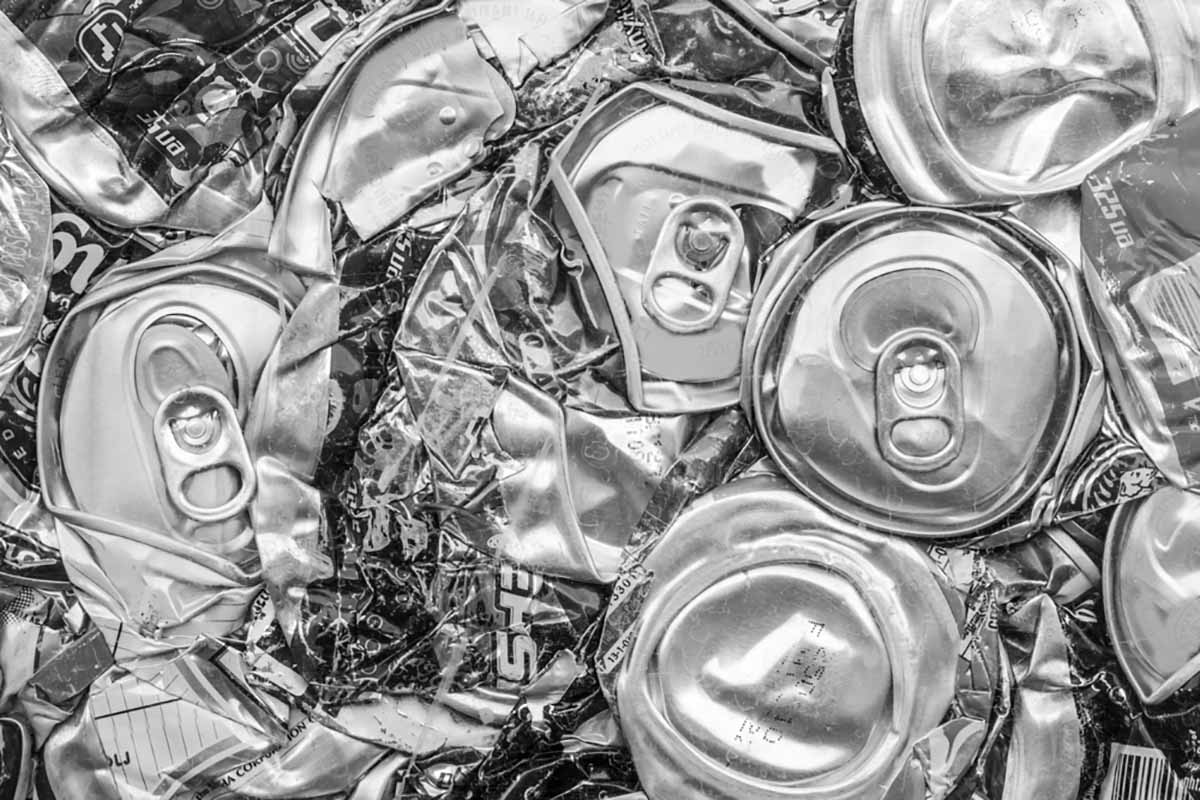
About 40% of the feedstock consumed by Constellium last year was scrap material. | pim pic/Shutterstock
Global aluminum manufacturer Constellium, which operates a large recycling site in Alabama, says it boosted the amount of production scrap it recycled last year.
According to the company’s 2020 sustainability report, about 40% of the feedstock consumed by Constellium last year was scrap material. Of that, 18 percentage points was post-consumer scrap and 22 percentage points was pre-consumer scrap generated by Constellium’s downstream manufacturers.
In 2019, 38% of Constellium’s inputs were recycled (18% post-consumer and 20% pre-consumer).
Headquartered in Paris, Constellium sells aluminum for use in various sectors, including the packaging, automotive and aerospace sectors. In terms of packaging, it provides aluminum for use by AB InBev, Amcor, Ardagh Group, Ball, Can-Pack, Crown, Coca-Cola and others.
The company operates a facility in Muscle Shoals, Ala. that’s capable of recycling 340,000 metric tons of post- and pre-consumer aluminum scrap a year, including used beverage cans (UBCs). Constellium calls the plant one of the largest UBC recycling plants in the world.
The company also has smaller recycling capabilities in Neuf-Brisach, France (recycling capacity of 150,000 metric tons of post- and pre-consumer scrap); Valais, Switzerland (30,000 metric tons of pre-consumer scrap); Issoire, France (20,000 metric tons of pre-consumer scrap); and Děčín, Czechia (20,000 metric tons of post- and pre-consumer scrap).
Constellium plans to further boost its consumption of recovered metal in the future. Earlier this year, it announced a plan to borrow hundreds of millions of dollars for sustainability projects, including metals recycling.
Recycled content in more products?
The 2020 sustainability report included several other updates related to recycling.
For example, the company is conducting R&D to reduce beverage can weights by 10%. “Due for completion within five years, these projects focus on optimizing can domes, the heaviest parts of cans,” the report states. “Our innovative design should allow for a much higher resistance to internal pressure and a reduction in metal use.” Reduced materials usage yields environmental benefits, but lightweighting also means it would take longer for MRFs to accumulate UBC tonnages.
The company is also working to develop recycled-content end products that haven’t incorporated recycled metal because of quality concerns. One example is alloys used in cosmetics packaging.
“Our customers have started requesting alloys with recycled inputs,” the company noted in the report. “We are in the early stages of developing a new alloy that incorporates [post-consumer scrap] and will serve as coils for components such as lipstick sleeves and perfume caps.”
Additionally, Contellium has taken steps to reduce air pollution at its recycling facilities, according to the report. After conducting an R&D project, the company reduced emissions of volatile organic compounds (VOCs) by a factor of 10 at the Neuf-Brisach facility.
“After a successful pilot program with one recycling furnace in 2019, we expanded the initiative to the rest of the recycling units in 2020,” the report states. “We were pleased to see that we could reduce VOC emissions from all gas-fired recycling furnaces without productivity losses, major capital expenditures, or increased operational costs. Recycling process management and industrial process expertise were key to this result.”
More stories about metals
- Tariffs on Canada and Mexico take hold
- Aluminum giant shares expansion plans
- How a national deposit could drive can recovery