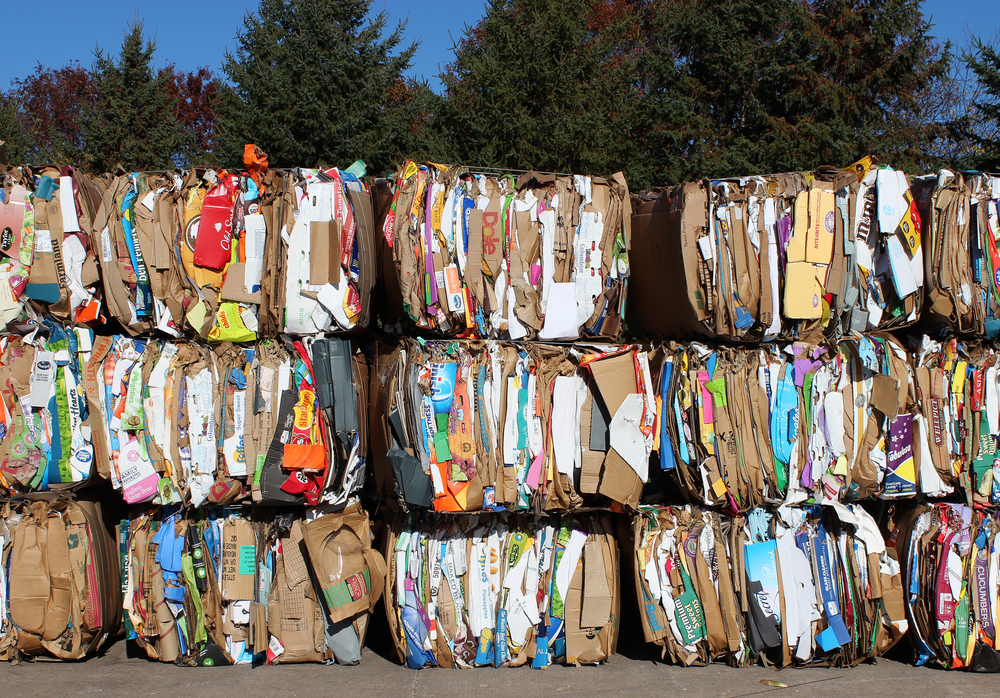
According to one analyst, domestic demand for OCC was up about 6% during the first five months of 2020. | digitalreflections/Shutterstock
Supply and demand realities for key curbside materials are evolving fast, impacted by the coronavirus pandemic, domestic processing capacity increases and other key trends, according to two experts.
Bill Moore of Moore & Associates and Stephanie Baker of KW Plastics last week described the factors impacting recycled material end markets. They spoke during a session of WasteExpo Together Online 2020, a virtual event held in lieu of the annual convention.
During the session, Moore outlined the state of North American end markets for recovered fiber, and he explained why mixed paper has become a more important commodity in the domestic marketplace.
Meanwhile, Baker described how the pandemic has shifted demand for recycled plastic and created surges in certain markets. She also explained recent investments her company has made to keep up with the demand.
Paper supply increase offset by recovery challenge
On the fiber side of the equation, the amount of OCC being generated is growing, Moore said, driven largely by more corrugated boxes being used in the e-commerce market.
However, the supply increase is not cleanly translating into more material being recycled. That’s because of lagging OCC recovery rates in the residential recycling space, where the new OCC supply is ending up, Moore said. There are “significant losses” in this space.
Moore said OCC recovery rates in the commercial sector, particularly from retail stores, is greater than 90%.
“The recovery of corrugated boxes from households is much lower: 40% or 45%,” he said. “And the primary reason is that a large percentage of households don’t participate in programs.”
That’s a particular challenge in the multi-family sector, where recycling access lags far behind that of single-family homes and contamination is a larger problem.
Mixed paper remains among the largest fiber grades handled in the recycling sector and is “the most under-recovered,” Moore said.
The recycled newsprint market is “really kind of disappearing,” with very little generation and the pandemic accelerating that trend. Meanwhile, higher-grade printing and writing paper generation is on the decline as they are simply used less in the business world, Moore explained.
Domestic demand outlook is strong
OCC exports were down 24% during the first half of 2020 compared with a year earlier, Moore said, while overall recovered fiber exports dropped 25%. Much of the decrease stems from China reducing imports steadily in recent years, a trend that will likely continue with the country’s all-out ban on recovered material imports next year.
“We expect to see zero recovered paper exports to China,” Moore said.
Moore tallied some 4 million tons per year of announced North American recycled containerboard capacity coming on-line through 2023, all of which will use OCC and most will some some amount of mixed paper. A couple of those projects are speculative in terms of financing, he noted.
Domestic demand for OCC was up about 6% during the first five months of 2020 compared with 2019, Moore noted. He pointed to a handful of recycled fiber mill projects coming on-line during 2020, including International Paper in Riverdale, Ala.; McKinley Paper in Port Angeles, Wash.; Nine Dragons (ND Paper) in Rumford, Maine; North Pacific Paper Company (NORPAC) in Longview, Wash.; and Verso in Duluth, Minn.
Moore cited a handful of projects that have increased or will grow domestic mixed-paper demand, including Pratt Industries in Wapakoneta, Ohio; Green Bay Packaging in Green Bay, Wis.; Cascades in Bear Island, Va.; Copamex in Anáhuac, Mexico; McKinley Paper and NORPAC.
During the first half of 2020, U.S. mills consumed 4% more mixed paper than they did in 2019, Moore reported.
If those mill projects had been undertaken 10 or 15 years ago, Moore said, “they would have been OCC only.” As is, mixed paper has begun to look more attractive given its significant supply, particularly in times when OCC prices spike.
Growth in mixed-paper consumption will likely continue into the future. OCC demand “will outpace supply going forward,” Moore said, “so we need more mixed paper.”
MRFs are increasingly rising to the task of creating a cleaner mixed-paper product, and mills are able to install increasingly advanced stock preparation equipment.
Pandemic hits paper recovery hard
COVID-19 has had a “real impact” on OCC recovery, Moore said. Recovered fiber collection as a whole dropped 30% to 50% during the second quarter of 2020, he said. That echoes a collection decline figure offered by Hannah Zhao, senior economist of global recovered paper for analysis firm RISI, in May.
With many retail outlets, schools and other recovered fiber generators slowing down or shuttering altogether, OCC generation declined between 20% and 30% during March. Grocery stores were a rare exception, seeing an increase in generation as consumers went through a phase of panic-buying.
“There was a real run on OCC in April and May, and residential volumes went up – but again, we lose a higher percentage of that OCC,” Moore said.
Beyond generation impacts, the pandemic led some MRFs to make operational adjustments that impacted their ability to sort material, such as slowing sort lines due to staffing shortages. These changes have mostly reversed, Moore noted, and the key concern now relative to recovered fiber impacts is whether the country will climb out of the coronavirus-driven economic slump quickly, or whether the impact will linger.
Crisis reinforces value of recycling
Plastics recycling operators, meanwhile, are encountering their own set of issues.
Public perceptions around plastic have shifted during the pandemic, after a few years of heavy anti-plastics sentiment that sometimes translated into product bans, explained Baker, director of market development for KW Plastics.
“Suddenly, COVID-19 hit and safety and health became an immediate priority overnight,” Baker said. Single-use products found a newfound benefit in preventing the transmission of the new virus.
Supplying the products became the new challenge, and KW, a major reclaimer based in Troy, Ala., quickly began receiving letters from customers who were concerned about sourcing sufficient resin to meet higher demand. Those supply concerns placed greater value on the importance of recycled material processors.
“From the very beginning, there was no question whether recycling was considered essential or not,” Baker said.
“I think it shifted the conversation from talking about recycling as part of the waste industry to talking about recycling as part of the manufacturing industry,” she said.
Demand impacts vary by grade
KW witnessed how the pandemic increased and shifted resin demand substantially.
Demand for natural HDPE spiked quickly, because that resin is used in a wide range of consumer goods products. It is attractive for manufacturers because it can be used to produce products of any color.
“We were sold out immediately for that material,” Baker said. The company received letters from buyers committing to purchase as much resin as KW could supply, a trend that is still continuing.
Mixed-color HDPE saw more of a demand shift, rather than all-out increase. The automotive sector is a major end market for this material, and with car manufacturing shut down in the early weeks of the pandemic, a huge market disappeared and KW saw a short-term decline in that arena.
But as car sales slowed, home improvement projects increased, and KW saw demand growth from agricultural product producers making plant pots and similar rigid plastic products.
KW is also a major PP reclaimer, and the company has seen greater interest from brands in exploring recycled PP use in their products in recent years. That activity slowed to a halt with the onset of the pandemic as companies focused on the essential items that were in high demand. Now, Baker said, some of those PP projects are back in the works, and KW is seeing continued commitment from brands to use recycled PP.
“That is back and shows some very strong signals that we’ll continue to see demand growth for polypropylene,” she said.
Meanwhile, KW is experiencing PP product demand trends firsthand through its in-house manufacturing operation that produces paint cans from recycled PP.
“We have never seen demand in the paint and coatings industry like we have,” Baker said. Typically demand spikes in the spring with consumers launching home improvement projects, and demand levels off late in summer as fall approaches.
This year, “the retailers that sell paint are still going very strong,” Baker said. KW has added additional lines and hired more employees to keep up with that PP paint can demand.
Demand trends could be here for the duration
The overall demand increase across resins led KW to add two new extruders to its production line.
“If we can get the equipment, which is tight right now, we have plans to add two or three more, because we feel like we are going to see this demand continue to grow for at least the next two or three years,” Baker said. “We want to do everything we can to get ahead of that demand.”
“So we are investing in the middle of the pandemic, as crazy as that sounds, into more production capacity,” she continued.
All of these developments indicate that domestic recycled plastic end markets are “very strong and they are reliable,” Baker said.
She attributed KW’s success during the pandemic in part to its diversity of suppliers and customers, and its critical mass of sourced material.
More stories about markets
- ‘Operational readiness is high’ as Oregon rolls out EPR
- Pizza box demand declining, report says
- Paper operations close in Georgia, Texas