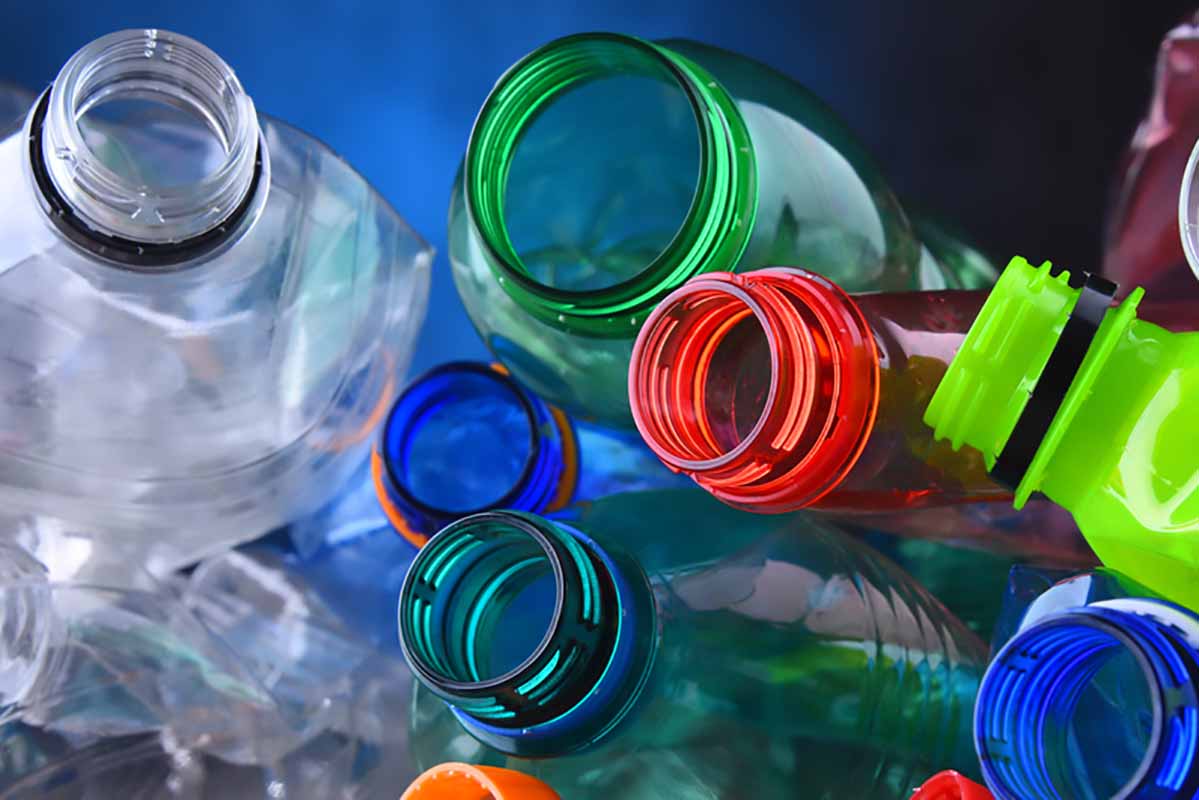
Eastman’s Kingsport, Tennessee plant uses methanolysis to chemically recycle PET. | Monticello/Shutterstock
In their latest earnings call, Eastman representatives said the company’s chemical recycling facility in Kingsport, Tennessee, is ramping up to 100% capacity and is gearing up to take in a “broader set” of uncommonly recycled plastics.
During the July 26 call, Eastman CEO Mark Costa said the company will be “running very hard with the facility” during the third and fourth quarters of the year. The plant started up late last year, and Costa said the company has “learned a lot over the last five months, six months of startup.”
“This has been a journey,” he said. “This is an incredibly complex plant to take garbage and turn it into clear, on-spec polymer that doesn’t have any materials of concern that can exist in that waste feedstock.”
Eastman’s chemical recycling plant uses methanolysis to process scrap PET chemically recycled resin, which the company brands as its Tritan Renew resin line. That includes food-grade PET resin with up to 75% recycled dimethyl terephthalate, or DMT, one of the chemicals produced by the methanolysis process.
“That’s the most difficult product we have to make, the highest standards on clarity, a wide range of performance specs, and we’re making these products with no materials of concern getting through the purification process,” Costa told investors. “So, a very safe product from garbage and that’s an incredible accomplishment and a great job by our team in operating this plant and overcoming a series of challenges.”
The facility takes in hard-to-recycle PET materials, specifically opaque and colored packaging, from sources including a supply agreement with Midwest recycling operator Rumpke. Costa noted Eastman has achieved sustained operating rates of 70%. He added it is working to ramp up to 100% capacity, but that a minor mechanical issue made that a challenge.
“We just recently made the change this week, actually, in fixing that one mechanical issue, and we’re ramping up to full rates,” Costa said.
Additionally, he hinted the facility is expanding to process “a broader set of hard to recycle feedstock,” but that it has encountered challenges in doing so. Costa didn’t specify which additional feedstocks the company is looking at, beyond noting it is similarly hard-to-recycle plastic materials. But he elaborated on the challenges of expanding the processing capabilities to cover additional streams.
“I want to be clear that this is not about chemical impurities, it’s not about processed chemistry,” Costa said. “It took us a few weeks to really understand what was going on, but we realized that it was in the feedstock preparation and some of the fitness for use aspects of a few sources of material.” Addressing those issues involved removing non-plastic contaminants that were coming in from certain feedstock sources, he said.
Costa noted the chemically recycled resin is being purchased by high-profile brand owners such as Procter & Gamble, L’Oreal, Estee Lauder and others. He added that a handful of new customers are experimenting with using the resin, including tool supplier Black & Decker.
Costa also commented on the challenges brands face in their commitments to use recycled content. More and more companies have been publicly acknowledging they’ll miss upcoming target dates to meet specified goals.
“They’re not on track to hit their targets for 2025, partly because the economic situation had them moving a little bit slower,” Costa said, adding that brands are missing targets “partly because mechanical recycling isn’t available to solve the problems.” He added that’s doubly true for the hard-to-recycle packaging materials brands use, offering the example of an opaque plastic tray.
“In many of those you cannot actually use mechanical recycling to actually make those products,” he said. “So they’ve got a challenge on how they’re going to actually get recycled content into some of those products.”