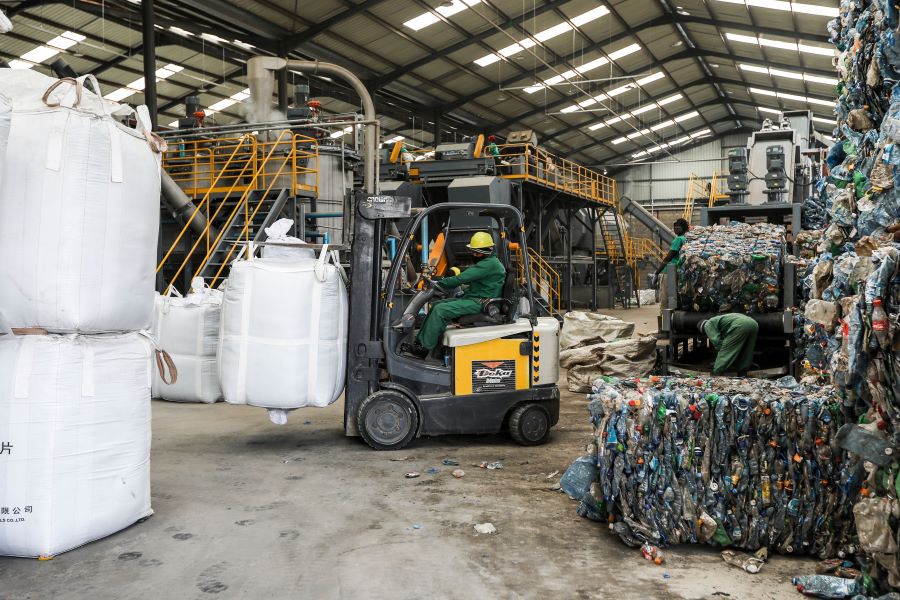
A view inside T3’s PET recycling facility, which produces hot washed flakes, in Athi River, Kenya. | Courtesy of T3 Limited
When it comes to PET bottle recycling in Kenya, a lot will sound familiar to North American audiences: demand for food-grade RPET outpaces supply, collection remains a challenge, and companies want to shorten supply chains.
But other factors are unique, including the fact that the Kenyan government is still working on how it judges the safety of food-grade PCR.
“It’s also very new territory for [regulators], and they’re just trying to find their way around it,” said Gurpreet Kaur Kenth, founder and chief operating officer of plastics reclaimer T3 Limited.
In an interview with Plastics Recycling Update, she talked about recycling realities on the ground in the East African country.
In addition, she outlined her company’s move to purchase a Starlinger recoSTAR PET recycling and extrusion line for its plant in Athi River, which is about a half-hour drive from Nairobi, Kenya’s capital. It will be the first bottle-grade RPET production line in East Africa.
The company’s operations
Owned by the Megh Group and founded in 2018, T3 (“Trash, Thread, Textile”) is already one of the largest PET reclaimers in the region. The company specializes in producing hot-washed PET flakes, Kenth said, with about 70% of the product going to food packaging and 30% to textiles – some flakes are fed to a sister company’s automotive upholstery business.
For collection, the company relies on an expansive and varied network of informal sector suppliers, whom T3 pays for scrap. T3 also provides training for basic skills such as bookkeeping and money management. “Our primary goal is to formalize the informal sector by uplifting them,” she said.
T3’s other goal is to achieve the environmental benefits of recycling, she said. With demand for RPET exceeding supply, it’s also good business.
“As the recycling industry is growing globally, it’s also growing in Kenya,” she said. “Consumers are becoming more conscious and the demand for recycled material, it’s exponentially increasing right now.”
Currently, T3 primarily exports PET flakes to Europe, where converters produce bottle pre-forms for major beverage bottlers, including for Coca-Cola products. The Starlinger line, a nearly $7 million investment, will allow T3 to produce PCR locally for conversion into bottle pre-forms, said Kenth.
Financing the system was challenging, especially in today’s uncertain finance environment in Kenya, where interest rates are rising three-quarters of a percentage point every few months, she explained. But along with debt financing, T3 received financing help from Swedish investor The World We Want Foundation (3W), she said.
The system is scheduled to be installed and commissioned in the second quarter of 2024, she said.
The need for regulations
Kenya currently has a voluntary producer responsibility organization framework through which some beverage companies, particularly international ones with sustainability commitments, pay to support PET recycling in the country. Founded in 2018, the Kenya PET Recycling Company is funded by voluntary contributions from retailers, packaging converters and beverage companies, including Coca-Cola.
But Kenth estimated roughly one in five producers voluntarily contribute money to help finance PET recycling in the country.
Mandatory extended producer responsibility (EPR) regulations are on the way. National leaders have adopted the EPR policies, which should come into effect within weeks and will force producers to pay to help support PET collection and recycling, she said.
It should help with collection, which Kenth said is “very erratic and the most challenging aspect of our business.”
“We’re really hopeful that the EPR will and should change collection, because obviously you get to incentivize more, you get to buy the plastic at a higher price,” she said. “It becomes more attractive for them. They’ll get more plastic out of the environment.”
Still, more regulations are needed, she said, particularly those requiring a minimum amount of recycled content in bottles. The multinational companies are interested in buying T3’s RPET to meet their internal targets, she said, adding that it will mean they don’t have to import material and can shorten supply chains.
“A lot of people are preferring local supply chains and that will also be beneficial to us,” she said.
But many local beverage producers aren’t interested, she said, pointing to a lack of awareness in the local beverage sector. Until the government mandates the use of RPET, she doesn’t see them purchasing PCR for bottles.
In some ways, T3 is also ahead of government food safety regulations. Because Kenya hasn’t produced any of its own virgin or recycled plastic for food containers, it lacks food safety regulations and approvals akin to those from the U.S. FDA and the European Food Safety Authority (EFSA), both of which she called the “gold standard.”
Leaders are working on those rules, but there’s no indication as to when they’ll finalize the draft standards, she explained.
When asked how she can be confident investing $7 million when Kenya’s food safety RPET regulations haven’t been finalized yet, Kenth pointed to strong international demand for RPET – some driven by Europe’s recycled-content mandates – and T3’s good relationship with multinational companies.
“At the end of the day, global demand versus supply will really be the reason why everyone is going to be investing in this industry,” she said.
More stories about processors
- Major plastic initiative sets sights on system change
- California will fund mixed plastics facility, other projects
- E-plastics processor expands line of recycled board