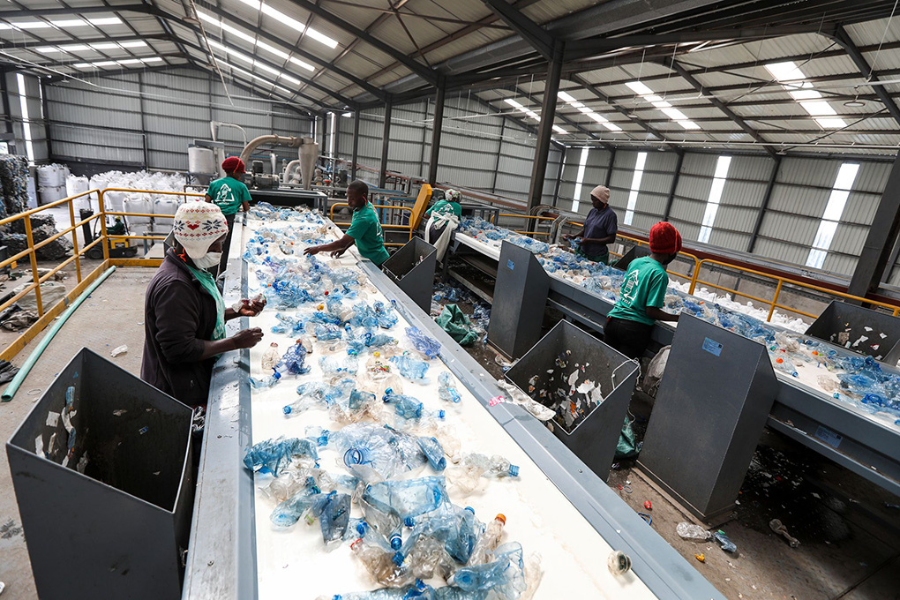
Workers sort PET at T3 Limited in Kenya. | Courtesy of Starlinger
Two companies recently installed Starlinger and SOREMA equipment to help boost PET recycling in Kenya and the Democratic Republic of Congo.
In Kenya, T3 Limited chose a Starlinger recoSTAR PET bottle-to-bottle recycling line, and in the Democratic Republic of Congo, OK Plast purchased a SOREMA sorting, washing and grinding line and a Starlinger pelletizing line.
Kenyan bottle-to-bottle system
Starlinger installed a recoSTAR PET bottle-to-bottle recycling line in Nairobi-based T3 Limited’s plant in Athi River, Kenya.
“Driven by the need to stop pollution of the environment in the country, preserve natural resources and increasing awareness about the benefits of recycling, the market for recycled PET in Kenya is growing,” a press release stated.
T3’s parent company Megh Group said the system is the first for bottle-grade RPET and resin in Kenya and Eastern Africa.
The food-safe RPET produced by the system can be used in bottle preform production and for polyester fiber production in the textile and garment industries. It will also be used for the group’s automotive trims and textile business, Megh Singh Cushion Makers.
T3 will source post-consumer PET bottles using various collection strategies including the informal sector of waste pickers, the press release stated, and “thorough collection and sorting methods and processing” will ensure the RPET “will be of highest quality to meet the standards of global brand owners such as Coca-Cola.”
Gurpreet Kaur Kenth, chief operating officer at T3, said the group’s goal was initially to produce textiles for the automotive sector, but they quickly saw the need for recycled materials in the packaging industry.
The press release noted that the plastics recycling industry in Kenya “is still in its early stages and faces challenges such as lack of input material and infrastructure, low levels of investment and limited access to market information.”
T3 developed its own collection system throughout the country by building incentives for waste collectors, the press release noted.
“Our goal has always been to put Kenya on the global map when it comes to recycling, and being the first company in Kenya to produce not only RPET but food-grade recycled resin will help us to achieve that,” Kenth said.
Democratic Republic of Congo RPET flake system
An OK Plast factory in Kinshasa, Democratic Republic of Congo, installed equipment from SOREMA and Starlinger in a recently built PET bottle recycling facility.
SOREMA provided the sorting, grinding and washing stages, and Starlinger provided the pelletizing line. The line is controlled remotely using the Sorema-Scada 4.0 digital monitoring system.
The OK Plast facility will recycle about 50 tons of plastics daily from Kinshasa. It has a production capacity of 1.1 metric tons per hour of washed RPET flakes for food packaging applications.
“The plant has been successfully commissioned and is another step in the continued expansion of recycling in Africa, helping to solve the plastic waste problem and providing new job opportunities for local communities,” a press release stated.
SOREMA has equipment in facilities in Nigeria, Algeria, South Africa, Egypt and Tunisia, as well.
The plant gets feedstock from a series of collection points in Kinshasa. After the material comes in, it is automatically fed into a pre-washing and de-labeling unit, followed by wet grinding, hot washing, flotation and rinsing and drying. The line has color and material detectors for both bottles and flakes for two stages of sorting.
After grinding and sorting by color, the flakes are transported to a Starlinger recoSTAR PET iV+ plant to be processed into pellets.