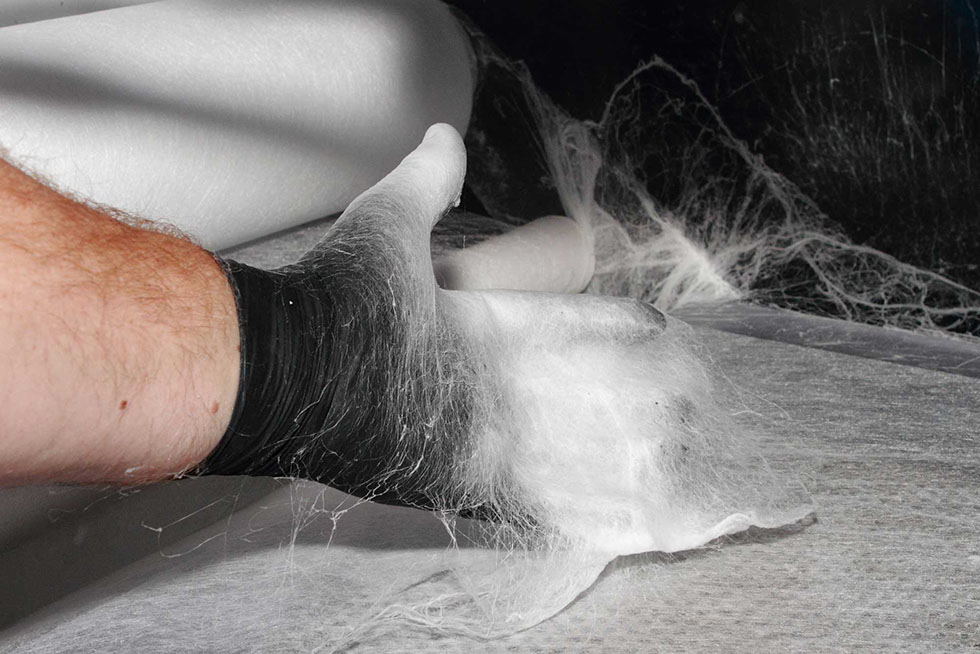
Verdex’s technology can be used to process a variety of polymers. | Courtesy of Verdex Technologies
A company has developed a technology for spinning contaminated post-consumer plastic into extremely thin fibers used to make filters, wipes and other products.
Atlanta-based Verdex Technologies used grant funding provided by stewardship group Carpet America Recovery Effort (CARE) to develop the recycling approach.
Verdex’s patented spinning nozzle technology converts post-consumer resin from carpet or bottles into nano/micro fibers, which are blended with larger fibers to form nonwoven sheets for use in apparel, air filters and sound-dampening materials. Verdex can work with PET resin containing PP and calcium carbonate, both of which are other materials used in carpet.
A document provided by the company indicates it has processed post-consumer compressed plastic produced by Lincoln, Calif. reclaimer Circular Polymers. Circular Polymers, which uses a rotary impact separation technology to recover plastic from carpet, has also received grant funding from CARE.
Verdex’s “beam technology” can be used to process the following polymers: PET, PCL, PLA, PP, PBT and nylon 66. The process uses low-pressure air and does not involve the use of solvents, according to a press release from Verdex.
The release notes that only about 10% of U.S. carpet scrap is recovered, with about 4 billion pounds per year going to landfills.
“Verdex recycling technology can help alleviate this major problem by taking post-consumer carpet and bottles, and turning these into high value nanofiber media for our customers to enhance existing products or create whole new product lines,” Damien Deehan, co-CEO at Verdex Technologies, stated in the press release.
The company currently has a lab-scale line but is scaling it to a 1-meter-wide commercial line, according to the release.
To receive the latest news and analysis about plastics recycling technologies, sign up now for our free monthly Plastics Recycling Update: Technology Edition e-newsletter.
More stories about technology
- RIT researchers develop AI-based textile recycling system
- Industry nuance is key in adopting emerging technology
- Google, Dow partner on AI to identify recyclables