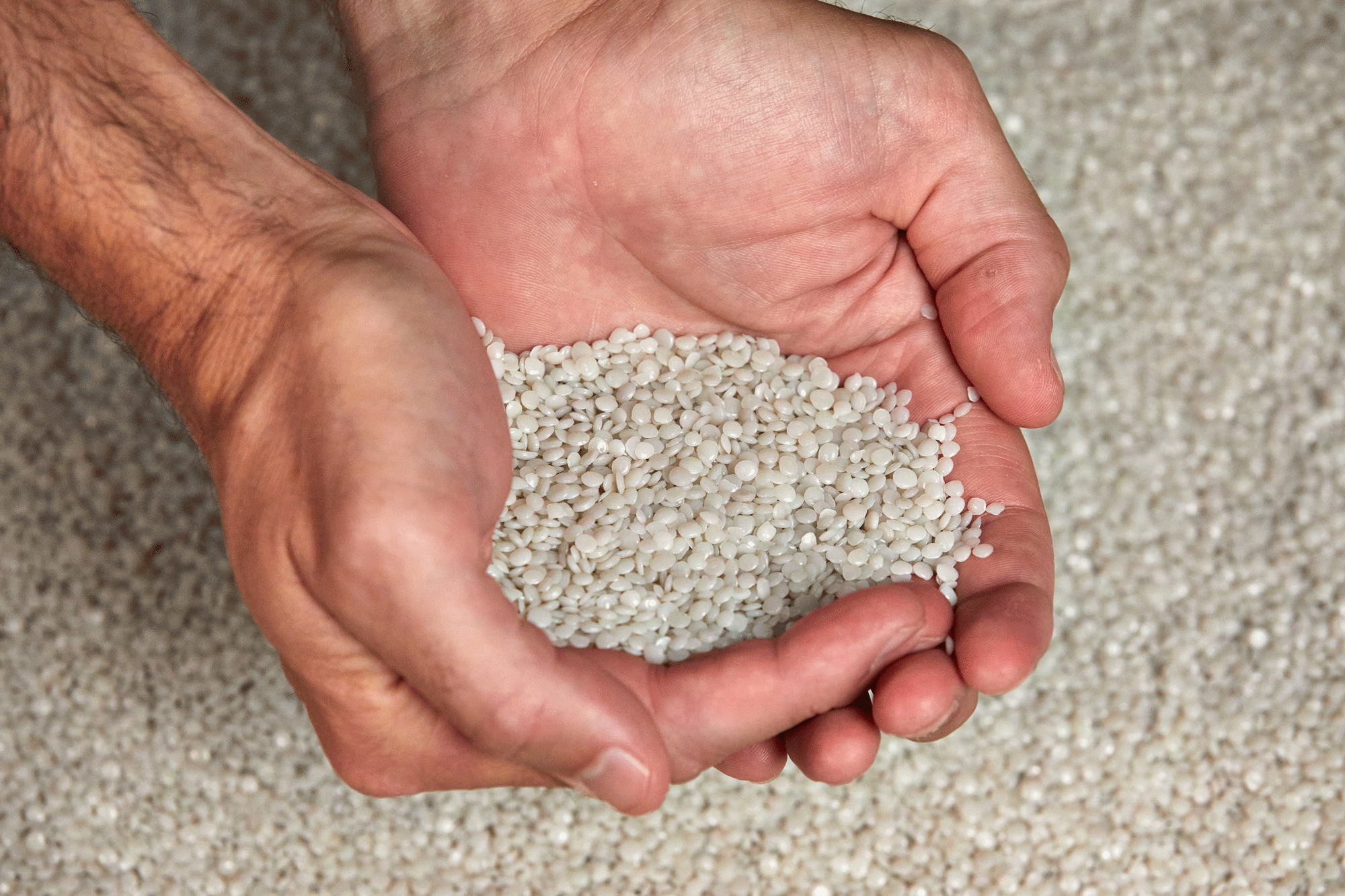
When Canadian polyethylene producer Nova decided to focus on mechanical recycling, less than two years after announcing it was looking at developing a major chemical recycling plant, it joined a growing list of sidelined projects. | Photo Courtesy of Nova Chemicals
The past few years have seen no shortage of ambitious announcements relating to chemical recycling, from small startups to major oil and chemical companies, as recycled content requirements increase and polymer producers struggle to harness future market direction.
In the most recent development, representatives for Canada-based Nova Chemicals confirmed to Plastics Recycling Update in March that they had decided against pursuing a chemical recycling plant in Sarnia, Ontario. In mid-2023, Nova announced it was partnering with U.K. technology company Plastic Energy on a feasibility study for a chemical recycling plant that would be the largest of its kind in Canada.
“Upon completion of the feasibility study in 2024, NOVA Chemicals and Plastics Energy ultimately decided not to pursue the project at this time,” Nova said in an emailed statement.
Companies such as Nova are exploring 10-30 capital investment projects at any given time, said Greg DeKunder, vice president at Nova Circular Solutions, in an interview with Plastics Recycling Update. “So just statistically-wise, it’s not unusual that a lot of projects get shelved because we’re looking at a big pipeline for limited capital dollars, and that’s true of every company right now.”
Chemical recycling projects in particular are large and expensive, and “we need a very robust business case for our shareholders and stakeholders to invest,” DeKunder said.
Still, DeKunder emphasized that even though Nova has decided against investing in chemical recycling for now, “it’s not dead. We’re still looking for ways to make that project or another project work, and sometimes you just have to wait for the market and external factors to be more advantageous.”
For the time being, Nova’s focus is to proceed “full steam ahead on mechanical recycling,” starting up its first such plant in Indiana in early 2025 to process post-use LLDPE film. Nova views chemical and mechanical recycling not as competing technologies but “a hierarchy of solutions, and we want to have both in our portfolio. But right now, what makes the most sense to Nova is to go (with a) strong growth program on mechanical recycling.”
Other chemical recycling projects that have been postponed or canceled include Eastman’s PET depolymerization plant in France, Braven Environmental’s planned Virginia plant, Encina’s Pennsylvania project and Brightmark’s plastics-to-fuel recycling plant in Georgia.
But some high-profile projects for chemical recycling – also called advanced or molecular recycling – are reporting progress, including PureCycle, Eastman and ExxonMobil.
In any case, given the current industry environment, several factors can make such large projects too risky, DeKunder said, including feedstock insecurity and insufficient offtake commitments.
Feedstock insecurity shifts industry strategy
While virgin polymer projects tend to be developed in tandem with feedstock capacity expansions, recycling projects may be proposed independent of sourcing considerations.
“I’d say the chemical recycling industry … has seen headwinds in the rollout of chemical recycling projects,” said Agilyx CEO Ranjeet Bhatia during an earnings call in August 2024. He added that the announced chemical recycling project volumes exceed the supply of feedstock by about 60%.
And as 2030 packaging targets approach, “the urgency to make investments to reach targets is really increasing,” which led Agilyx to shift its primary business focus to sourcing feedstock for chemical recycling. “We are focused less on a large pipeline of licensing targets but instead focus more on developing a cornerstone project and a partner to deploy that technology,” Bhatia said.
Although chemical recycling facilities have “a very broad diet of what they can consume, they require a lot of feedstock,” Nova’s DeKunder said, adding that such large investments need multi-year feedstock security.
“And in the plastic waste business, that’s not common. So these companies that are investing in advanced recycling, or chemical recycling, are trying to change long-term practices of not having long-term entrenched security of supply of the feedstock.”
As a response to such pressures, soon after the November investor call Agilyx’s joint venture Cyclyx announced it had made a final investment decision on its second plastics feedstock preparation plant, intended to supply partners ExxonMobil and LyondellBasell with feedstock for their chemical and mechanical recycling plants. The first Cyclyx plant is expected to start up this October. Attempts to reach Agilyx and Cyclyx for this article were unsuccessful.
However, on March 24 Agilyx launched Plastyx with the CEO of Plastic Energy, as a 60:40 joint venture between Agilyx and Circular Resources SARL. Plastyx is meant to supply plastic feedstock for chemical recyclers.
“Agilyx is committed to building an international sourcing platform to support our interests in Cyclyx,” Bhatia said in a press release.
Joe Vaillancourt, then-CEO of Cyclyx, indicated in the November investor call that LyondellBasell would be using offtake from the second Cyclyx plant to make pyrolysis oil intended for making new polymers. LyondellBasell has indicated it was likely to site chemical recycling and other operations in Houston after closing its only refinery in early 2025. However, the company has yet to make a final investment decision, and declined to comment for this article.
ExxonMobil has “a network of North American plastic waste feed suppliers, including our joint venture Cyclyx, that source from a variety of different locations,” spokesperson Lauren Kight told Plastics Recycling Update. In addition to the plastic sorting facility with Cyclyx, ExxonMobil is looking at future expansion plans, she added.
Diffusing risk via offtake contracts
The inherent risk of largely untested technologies combined with an increasingly unpredictable landscape – macroeconomic conditions, fragmented and developing legislation, consumer skepticism of recycling systems – creates myriad landmines for entities wishing to develop chemical recycling at a commercial scale.
This represents a departure from planning virgin chemical production capacity, which typically uses projections for decades into the future to help determine how likely it is that a proposed capital expenditure – usually for a time-tested production process with well-established and robust end markets, as well as plentiful feedstock supply – will pay off within a reasonable amount of time.
“So these offtake agreements are very important because they create that certainty for demand,” and signing offtake agreements before an investment decision is not unusual, as it helps reassure board members, investors and lenders, DuKunder said.
“In general, because this industry is nascent, because it’s not clear what the future demand will be and what the market will bear as to pay for circular products, it’s very helpful to have these offtake agreements with strategic customers, because then the whole value chain shares in the risk and the reward from from building a plastic circular economy,” he said. “And you’re not putting all of that on one company in the chain.”