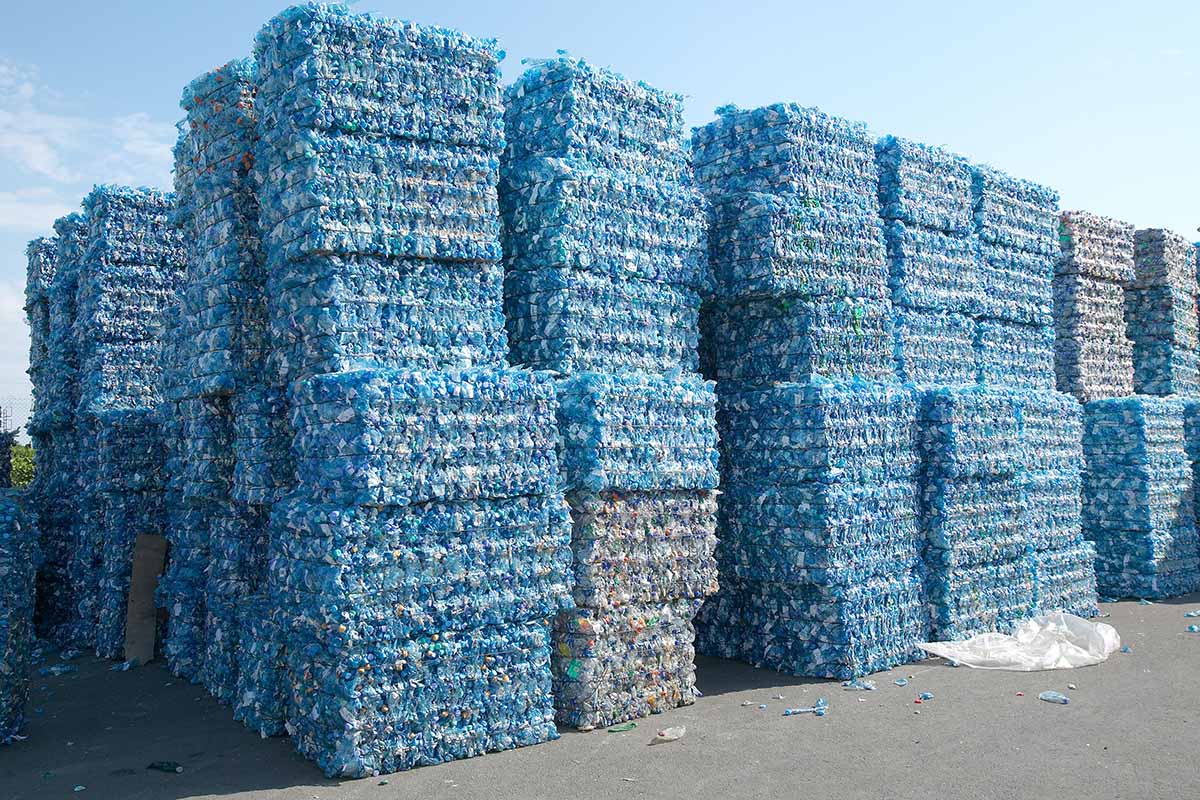
Three companies announced funding and other progress toward building chemical recycling capacity. | Menzl Guenter/Shutterstock
Several companies recently announced progress toward chemical recycling capacity, including a developing method to recycle PET that could require much less energy.
In east Texas, Braven Environmental will build a new pyrolysis plant, according to a press release from Gov. Greg Abbott, in conjunction with the Texas Jobs, Energy, Technology and Innovation program. JETI was announced in February 2024 to provide a competitive economic incentive to help attract jobs and investments to the state.
The Texas plant will be the second after Braven’s first in Zebulon, North Carolina. A 2023 press release said the forthcoming project would produce approximately 50 million gallons of pyrolysis oil per year and process more than 250,000 tons of hard-to-recycle plastics.
In October 2024, Braven entered into a second long-term pyrolysis oil offtake agreement with Chevron Phillips Chemical, a joint venture between oil refiners Chevron and Phillips 66. Braven previously signed a similar agreement with CPChem for its North Carolina plant in 2021. Houston-headquartered CPChem is a global producer of PE and styrenics.
In 2020, the year the Zebulon plant started up, Braven announced it would build a plant in Cumberland County, Virginia, but two years later, local news reported that the project had fallen through.
Another company, California-based Resynergi, raised $18 million in funding toward commissioning its first commercial-scale chemical recycling plant in its home state, according to a Feb. 20 press release.
About a year ago the company raised $6.4 million to help bring its modular continuous microwave-assisted pyrolysis technology to commercial scale. The modular design enables rapid scaling compared to traditional on-site construction, and it processes up to 50 tons of discarded plastic per day, according to the company site.
MacroCycle Technologies
Boston-based MacroCycle Technologies is working toward scaling up its pilot plant for chemically recycling PET, with a recent $6.5 million seed financing round led by Clean Energy Ventures and Volta Circle, an investment firm backed by the founders of Indorama Ventures.
The MacroCycle technology uses 80% less energy than other chemical recycling methods and requires 50-75% less capital expenditure, the company founders said, which would help make recycled PET more competitive with virgin resin.
MacroCycle will use the funding to hire process engineers, said Jan Rosenboom, co-founder and chief technology officer, in an interview with Plastics Recycling Update. Later funding rounds will go toward scaling up its pilot plant to further develop PET and polyester resin with initial customers, according to a press release.
MacroCycle plans to recycle PET bottles and polyester textiles from customers in the cosmetics, textiles, home goods, food and beverage industries with large packaging waste footprints as well as luxury and fast fashion clothing brands.
The pilot plant will be the company’s first effort toward scaling up operations and will produce the first bottles and garments entirely from MacroCycle’s recycled PET resin.
“Everybody’s trying to go back to the single monomer or oligomer, to then have a very small molecule that can be fed back into the supply chain of petrochemicals,” said Rosenboom.
Post-consumer PET is composed of a chain of about 100 molecules, Rosenboom said, while about 150 are needed to make a new beverage bottle. The MacroCycle process selectively “parks” the scrap PET chains in a cyclic form, then opens and ties those “macrocycles” together to regain the 150-unit-long polymer molecule. He said the process is simpler than other approaches that break down the polymer to single molecules, and thus is more energy-efficient.
Longer chains mean stronger, higher-quality polymers, which is why MacroCycle termed its approach “upcycling.”
The process also removes impurities such as colorants and additives, Rosenboom said, “which, of course, is absolutely critical, as I think every other technology is also discovering that impurity removal is important.”
As for feedstocks, MacroCycle is working with textile waste collectors in the U.S. and Europe, in addition to green and amber PET flake suppliers. “We are shooting eventually for the worst stuff,” Rosenboom said, though he acknowledged that in developing recycling technology, chemists start with the easiest materials, then the medium and then the worst at the end.
But the company doesn’t use clear flake, due to the cost but also because “we don’t want to interfere with the established mechanical recycling that is already doing very well and has sophisticated technology available,” he said. “We really want to use what mechanical recycling cannot take.”