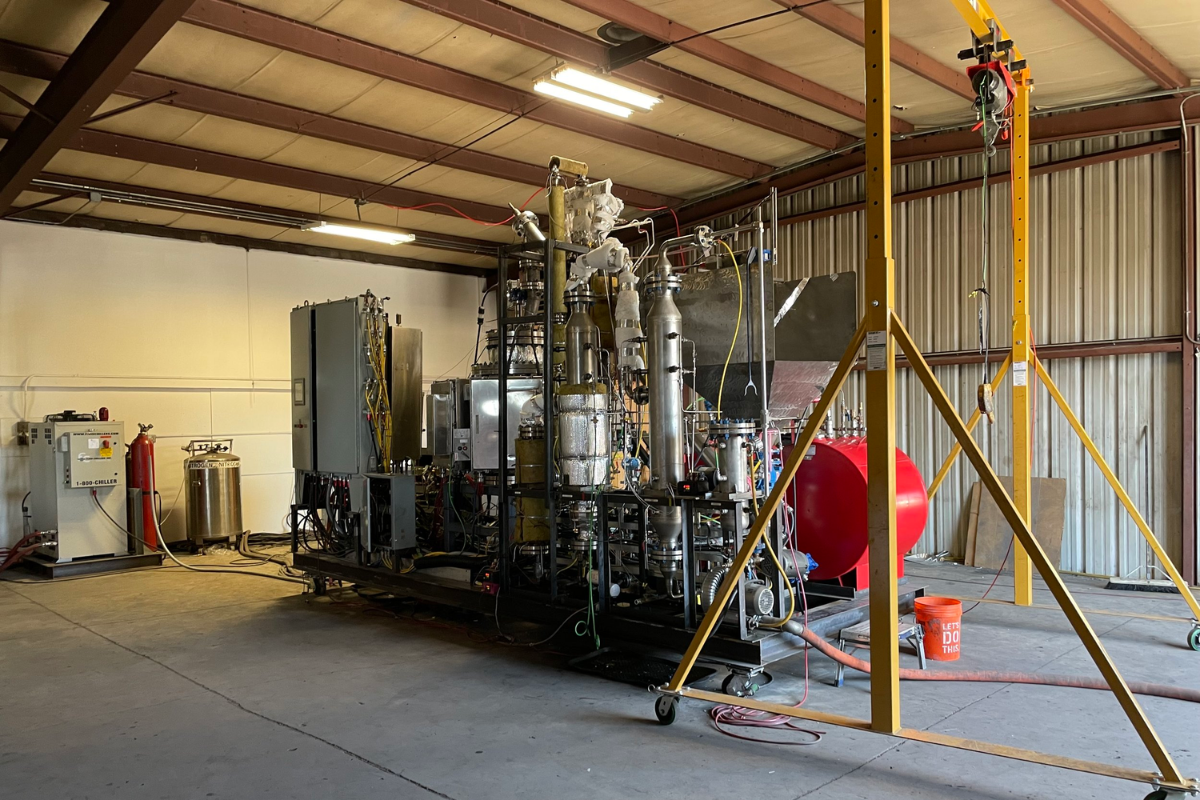
Resynergi’s Evolucient Continuous Microwave Assisted Pyrolysis technology uses microwave energy to break down HDPE, LDPE, PP and PS into pyrolysis oil. | Courtesy of Resynergi
Pyrolysis start-up Resynergi raised $6.4 million in series B funding to bring its modular Continuous Microwave Assisted Pyrolysis technology to commercial scale.
The funding round was led by venture capital fund Transitions First and global energy solutions company Lummus Technology.
In an interview, Brian Bauer, Resynergi CEO, said the funding will help the company build a commercial site to demonstrate how its five-ton-per-day model on a 40-foot skid can be utilized.
“All the functions of a plant are miniaturized on a skid,” he said, meaning customers no longer have to invest in a full build out to get a pyrolysis unit.
Resynergi also plans to use the funds to expand its executive team. Leon de Bruyn, president and CEO of Lummus Technology, and Marianne Abib-Pech, managing partner at Transitions First, will also join Resynergi’s board of directors.
Abib-Pech said in a press release that “as our natural resources are increasingly scarce, supporting Resynergi in scaling their recycling process technology is an example of our role in driving innovation and accelerating industrial transitions for a more sustainable future.”
The technology
Resynergi’s Evolucient Continuous Microwave Assisted Pyrolysis (CMAP) technology can take HDPE, LDPE, PP and PS. By using microwave energy to break down the plastic molecules into pyrolysis oil, the CMAP units can process plastics faster and also have a smaller footprint, Bauer said.
“We can basically bring the process to where the plastic is and eliminate the cost of transporting plastic all over the place,” he said. “Our model is very much to be located near where it’s locally collected already, near the MRFs.”
First, the materials go through an extrusion process. Then, microwaves are fired into a reactor vessel, which breaks the carbon chains in the plastics more quickly than other, traditional heating methods.
The output is about 80% diesel and 20% other materials, and the system yields about 90% of the weight of the plastic fed into it. For every ton of feedstock, the output is roughly 1,000 liters.
Bauer said the pyrolysis oil can be remade into plastic resin that can be used for food grade products.
“There also is a big demand for fuel, but that’s not a big focus of ours,” he said.
The continuous 1- and 2-ton reactor units have been in the pilot stage at a site in Santa Rosa, Calif., for the past several years, and now Resynergi will place several CMAP reactor units on a skid to create a 5-ton-per-day model.
Bauer said there are several different sectors interested in the technology, but the largest group is plastic manufacturers.
“Most of them have internal or external mandates that at least 25% of the plastic they make will come from recycled plastic by 2030,” he said. With that kind of mandate, they need new technology “that actually works,” he said.
Pyrolysis is a leading candidate, Bauer added, and though it’s taken several years to develop the technology, “it’s right on the cusp of much higher volumes.”
“There are so many solutions to recycling, and mechanical recycling has its place for sure,” he said, adding that “we feel like we’re just one part of the overall answer.”