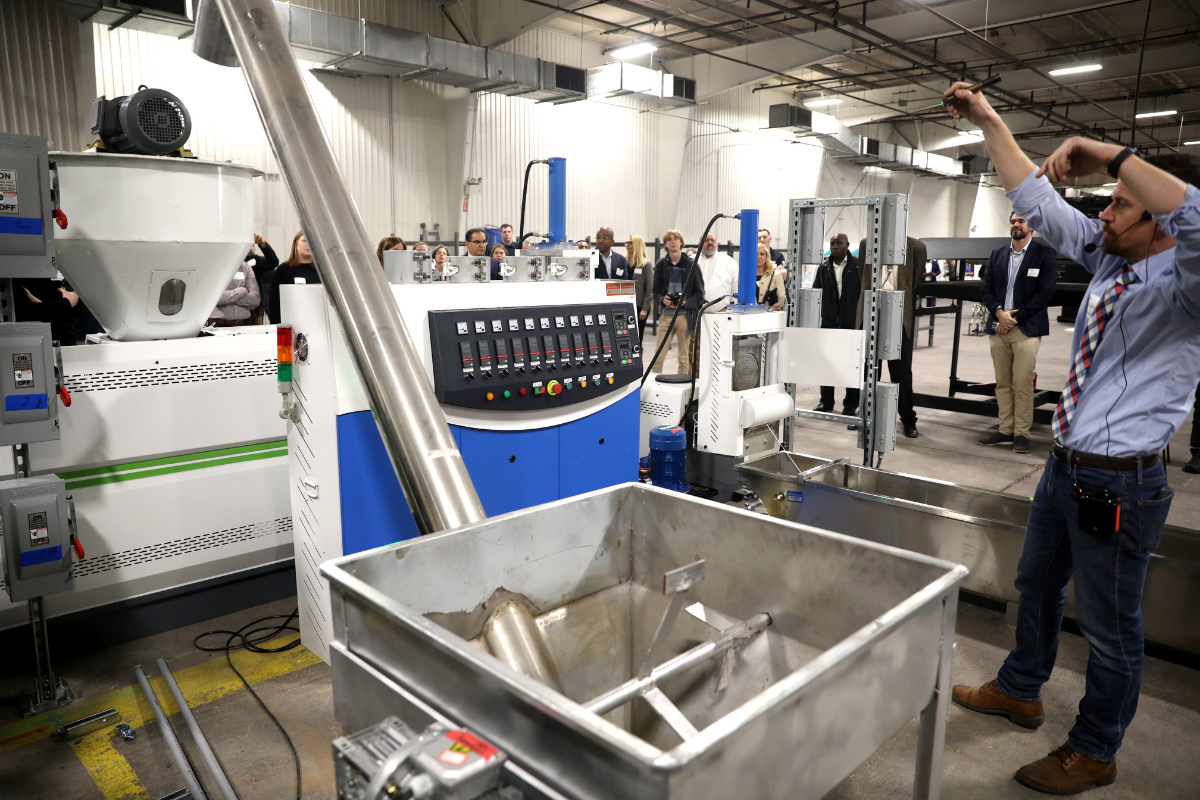
A partnership between the city of Phoenix, Arizona State University (ASU), Goodwill of Northern and Central Arizona and Hustle PHX will recycle several hundred tons of PE and PP into local end markets. | Courtesy of Goodwill of Northern and Central Arizona.
For years, recycling collection has focused on centralizing material and processing high volumes. An Arizona project is exploring other options with a micro-factory.
The micro-factory will recycle several hundred tons of PE and PP into local end markets. It’s a partnership between the city of Phoenix, Arizona State University (ASU), Goodwill of Northern and Central Arizona and Hustle PHX.
Alicia Marseille, senior director of ASU’s Rob and Melani Walton Sustainability Solutions Service, told Plastics Recycling Update that the relationship between the center and the city of Phoenix goes back 10 years in the circular economy space, and they have worked on around 25 applied research projects together.
This specific idea started to take hold five years ago, she added. Goodwill of Central and Northern Arizona came on as a partner a little over a year ago after they realized there were “a lot of values and vision alignment.”
“We have been working since then to commission and install the equipment,” Marseille said, noting that after those pieces are in place, the last step is setting up the workforce and entrepreneurship piece, which is where partner Hustle PHX will come in.
Amanda Jordan, circular economy project manager for the City of Phoenix, said Hustle PHX has “a lot of unique support methods” that will help get the project up and running.
Aligned around circularity
Beth Forsberg, senior vice president of sustainability for Goodwill Central and Northern Arizona said that sustainability “has always been at the heart of everything Goodwill does.”
“When you look back at our history, over 120 years ago our founder decided it would take things that would otherwise be discarded and create jobs,” she said, and the micro-factory project is an extension of that vision.
“Not only is it an opportunity, but it’s also a responsibility to serve our communities,” Forsberg added.
The donations Goodwill receives most frequently are textiles and plastic, she said. Goodwill of Central and Northern Arizona is the largest collector of material of any Goodwill in the U.S., with 112 retail centers or collection sites.
“We collected it, and now we’re going to provide some more circular solutions,” Forsberg said. “What we’re really excited about is providing the feedstock and also keeping jobs local and growing jobs.”
Facility details
On paper, the 10,000-square-foot facility can process between 500 and 600 tons of PP and PE feedstock per year, but as it’s a pilot, the team will get a better understanding of how to optimize the system as it ramps up, said Raj Buch, business development director at the Walton Sustainability Solutions Center.
Equipment in the facility includes a wet wash system, drying drum, an extruder, a pelletizer, a sheet press and a molding machine. The team is not sharing the cost of the project.
It will create both pellets and washed flake, Buch added. Between 30 and 40 tons of that material can then be used in the factory itself to make products annually. The rest will be sold into varied end markets.
While the project will handle just PE and PP to start, Marseille said the end goal is to build out additional material processing capacity in the future, perhaps including film.
Buch added that a “typical waste management system is large-scale, capital-intensive, skill-intensive” and needs to truck in material from a large area.
“What we’ve built is going to process only a few hundred tons,” he said, “but if we have a network of them, 10 or 15 in an urban area, processing different materials,” then it would reduce the need to move materials so far and create decentralization benefits, such as smaller factory footprints.
Both the city of Phoenix and Goodwill of Central and Northern Arizona have been collecting feedstock already in anticipation of the factory’s start-up. Forsberg said most donations come in plastic bags or cardboard boxes, but somewhere around one out of every three or four donations come in a plastic tote.
In a test diversion, Forsberg said Goodwill was able to fill about 900 gaylords with feedstock material in three or four weeks, “and it probably could have been considerably more.”
A model for others
Jordan noted that while Phoenix is unique in that it maintains ownership of its facilities including the MRFs, and therefore owns the waste stream material, this micro-factory model can still be replicated elsewhere as an economic development tool.
It could be especially useful in places that do not have a statewide policy push toward circularity, she noted, providing a way to “engage in a circular transition, divert waste and achieve some big goals set in climate action plans or otherwise through the cultivation of local entrepreneurial ecosystems.”
“From the city level, I’m hoping this can demonstrate how public and private sectors can collaborate on the solution,” Jordan said. “And it doesn’t have to be large-scale. That’s the beauty of this facility we’re building.”
Goodwill is also looking at the micro-factory model as a way to achieve “full circularity for every donation received,” Forsberg said.
“We are very optimized to work 24 hours a day to keep our stores fed and product moving, and this new project is a real complement to this system,” she added.
Marseille noted that one of ASU’s big goals is system transition and transforming the value chain, as no single entity can achieve that kind of change alone, and because the social, economic and environmental benefits that come from those partnerships “are not only amazing, but are imperative” to the future.