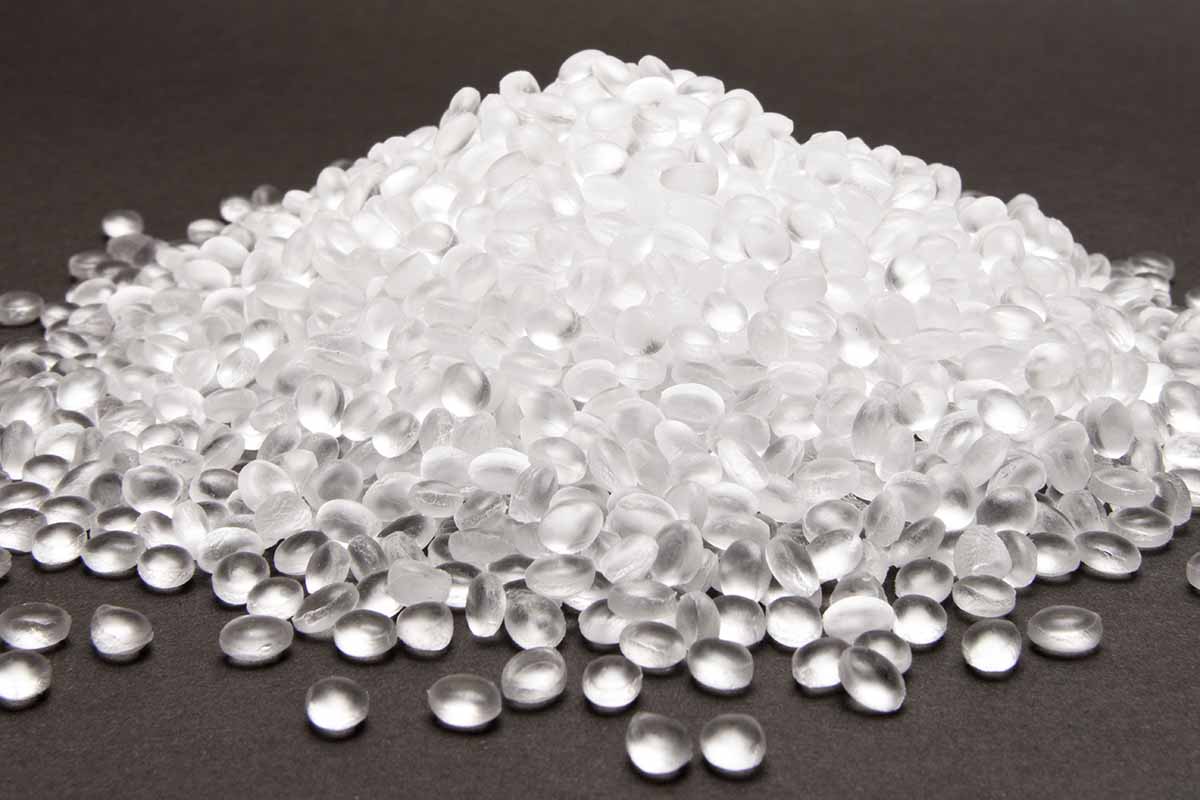
Birch Plastics can produce about 800,000 pounds of FDA-approved natural PP per month. | StanislauV/Shutterstock
Texas-based Birch Plastics recently received a letter of no objection from the U.S. FDA for a line of recycled PP that can be used in all food and cosmetic applications.
The post-industrial PP pellets can be used at levels up to 100% to manufacture articles intended to contact all types of food under all conditions of use. Rob Lang, president of Birch Plastics, told Plastics Recycling Update the company has been selling its recycled natural PP for two years now, but the letter of no objection (LNO) “opens up a whole new market for us” and the PLASTEON line.
“We are still in the process of finding and sampling customers,” Lang said, adding there’s a lot of interest in the food packaging industry.
Birch Plastics is an ISO-certified manufacturing facility with capacity to shred and grind 52 million pounds of scrap plastic annually and compound or pelletize 31 million pounds annually at its 100,000-square-foot facility in Houston. It sells virgin PE, PP, HDPE, LDPE and other plastic resin pellets. For recycled resin, it has lines of certified recycled-content PE and PP for injection molders, blow molders and thermoforming applications.
Lang said the facility has a monthly production of about 1.4 million pounds of sustainable compounds. About 800,000 pounds of that is the natural PP that just received the LNO. The company has a strong post-industrial PP feedstock source, Lang added, and the capacity to do custom compounding.
“We have a big in-house lab so we’re able to basically custom compound our natural recycled to certain specifications,” he said.
The company also has a natural HDPE line made from ocean-bound plastic. The hybrid PLASTEON natural HDPE is made from 30% certified ocean-bound plastics and 70% virgin resin.