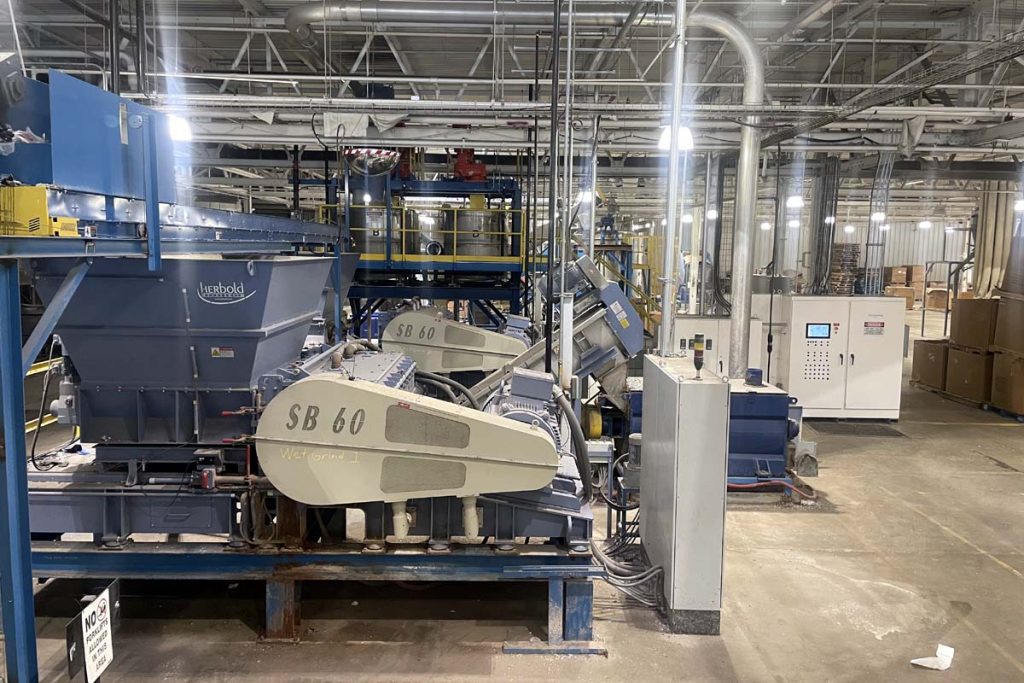
A wet grinder in Plastic Recycling Inc.’s new PP line in Indianapolis. | Courtesy of PRI
Plastic Recycling Inc. is now processing post-consumer curbside PP, with an eye toward obtaining an FDA food-contact letter in the near future.
The Indianapolis-based plastics reclaimer is initially sorting and washing about 25 million pounds of PP per year on the system, said Brandon Shaw, marketing manager for Plastic Recycling Inc. (PRI), but the system is modular and can be scaled up easily.
The line, which processes PP bales from materials recovery facilities (MRFs), includes a trommel, metal removal technology, shredding, optical sorting, wet grinding, washing and rinsing steps, float-sink separation, drying and color sorting.
The company is also looking to add sorting robots to produce a stream of PP scrap consisting entirely of food and drink packaging.
PRI has invested millions of dollars in recent years to boost its production capabilities, including by building-out a $3 million lab.
With the investments, including two new extruders that added 60 million pounds of annual capacity, PRI now has the capacity to produce 160 million pounds of recycled plastic, Shaw said.
In terms of post-consumer PP, specifically, the reclaimer can produce about 45 million pounds a year, said Marco Meloni, chief operating officer at PRI.
“We are able now to really respond to all the requests of the market in terms of recycled content, PCR content and virgin plus recycled products,” Meloni said. “So we are able now to give a very wide range of products to the market.”
Commercial-scale production starts
Located at PRI’s 550,000-square-foot compounding facility in Indianapolis, the new PP line is currently running. (PRI also has a 120,000-square-foot scrap processing plant in Indianapolis, as well as facilities in Tennessee and South Carolina.)
Shaw estimated the line cost about $2 million, not counting roughly $1 million worth of equipment already owned by PRI.
PRI has been buying bales for the last three months, with commercial production starting in August. “We’re working with all the big MRFs,” he said.
So far, PRI hasn’t had any trouble sourcing enough PP feedstock, Shaw said, noting that relatively few reclaimers are recycling curbside PP bales, with the market dominated by KW Plastics.
Prices for PP have been low lately, with post-consumer scrap averaging only about 5 cents per pound nationally, according to RecyclingMarkets.net. Throughout 2022, a year that included some high PCR pricing, bales averaged nearly 20 cents per pound, and during the first half of this year, they averaged 7.5 cents per pound.
Virgin pricing has also been low. Citing marketing conditions, plastics producer Braskem recently decided to reduce PP production levels at a plant in Pennsylvania, according to Plastics News.
Shaw acknowledged that there is a “tough market right now economically, but we are playing the long game and using the lab upgrade to create real compounds with the ability to create colors.”
PRI has invested substantially in its lab, which is expected to employ a staff of 17 people conducting testing on raw materials and finished goods, as well as R&D, Meloni said.
Pursuing a letter of no objection
PRI has received FDA letters of no objection (LNOs) for PP and PS in the past. LNOs allow their recipients to begin marketing their recycled resin for use in food and drink packaging, subject to any limitations spelled out by the FDA. The most recent one was for the mechanical recycling of PP, received May 28, 2019, according to the FDA database.
Shaw explained PRI’s existing PP letter covers source-controlled recyclables, from which PRI produces white, natural and colored compounds. The new line will help PRI achieve a letter covering curbside material, he said.
“With the line, we’ve got capabilities to make custom colors, sort by FDA/non-FDA streams,” Shaw said. “So we’ll be going after FDA on it.”
Closed Loop Partners, the NextGen Consortium and Greyparrot, a company that has developed a visioning system powered by AI, recently announced that they’re working on a study to analyze the composition of curbside PP bales. Their work will build off research conducted in 2022 by the NextGen Consortium and consulting firm Resource Recycling Systems (RRS), which found that PP bales from two MRFs contained about 48% food-grade PP.
Shaw said PRI’s internal analysis is more or less in line with that finding, with PRI calculating that nearly half of a bale is food-grade PP – about 26% clear/natural and 20% light colored. MRFs using optical sorters and robots generally produce the highest-quality bales, and those relying strictly on manual sorting generally produce the lowest, he noted.
In terms of pursuing an FDA LNO on the curbside PP, PRI’s lab can conduct 95% of the testing required by the FDA, Meloni said.
Shaw acknowledged that, for the MRF material, PRI won’t be able to achieve FDA’s A-H conditions of use. (At the top end, A allows the packaging to be exposed to sterilization processes over boiling temperatures, and and at the low end, H allows the PP to be used for frozen, ready-prepared meals that are reheated in a microwave in the package.) But the company’s in-house lab will allow PRI to achieve as many conditions of use as possible, he said.
Shaw said he expects PRI will receive an LNO for curbside PP in the next few months.
He anticipates the PCR would be used for items such as caps and closures, beauty product packaging, and more. It would likely be injection molded, with some thermoforming, as well.
PRI can essentially use its sorting and lab capabilities to make round pegs to fit into round holes, instead of asking customers to force square pegs in.
“There’s a lot of interest,” Shaw said. “Now that people are seeing what we’re doing, we can actually make a product they want, rather than pushing a product on them that they’re forced to attempt to use.”