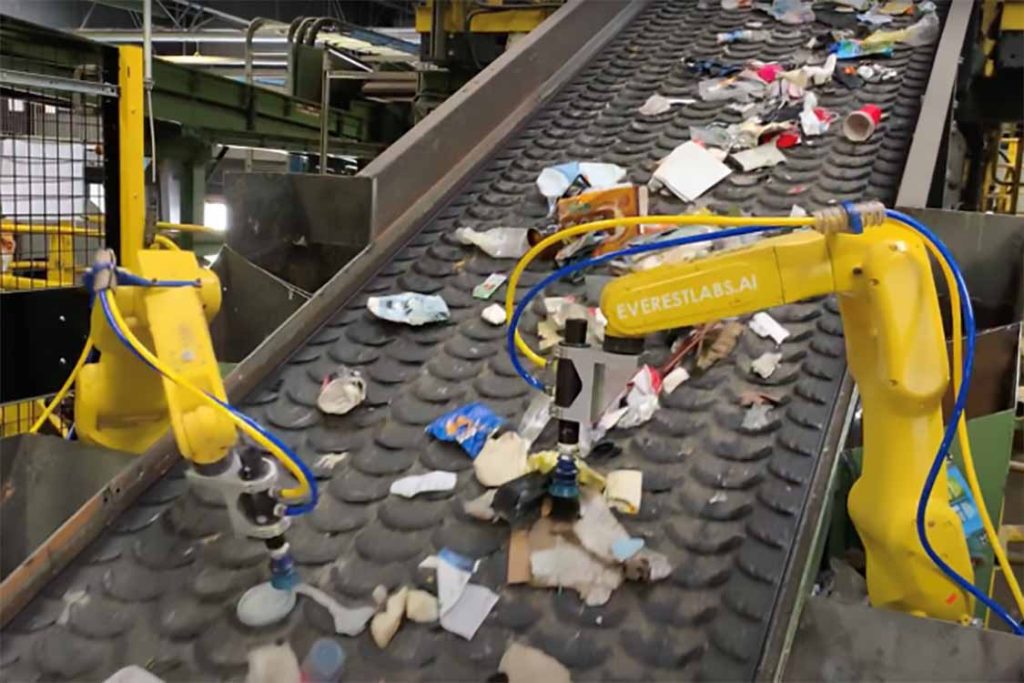
JD Ambati, CEO of robotics company EverestLabs, believes AI-powered robotic sorting can help materials recovery facilities improve both efficiency and safety. | Courtesy of EverestLabs
The recycling and waste industry has undeniably been impacted by labor shortages. According to the U.S. Bureau Labor of Statistics, the unemployment rate for the waste management and remediation services category, which includes materials recovery facility (MRF) workers, increased from 2.9% to 7.9% in November alone. Combined with a potential recession looming, it is now a race against time for industry leaders to identify solutions for navigating this volatile landscape and ensuring business continuity.
For MRFs, the answer to thriving in the downturn lies in rapid innovation.
The recycling industry’s life cycle of innovations
The recycling and waste sector has experienced a fairly robust timeline of innovations, starting with horse-drawn carts bringing waste to incinerators in 1800. Since then, the sector has seen a range of innovations for almost 18 decades, including the invention of the “dumpster” in 1936 and the introduction of the automated side-loader garbage truck in 1969.
That said, innovation in the MRF equipment industry halted after optical sorters for plastics were introduced in the late 1980s, with innovation lagging until 2015, when computing technologies helped bring recycling robots into the market.
AI and robotics have become much more accessible in recent years. Computing power available per dollar has increased by a factor of 10 roughly every four years over the last quarter of a century as measured in floating point operations per second (FLOPS) or millions of instructions per second (MIPS). This, in turn, makes running complex AI algorithms cheaper and
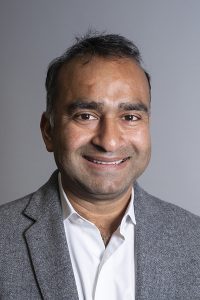
JD Ambati
faster. At the same time, innovations in software and hardware make robotic cells perform non-trivial and unstructured tasks.
As a result, AI and robotics can outperform humans at cost points, and for MRFs, it’s a no-brainer to leverage these systems to reduce human dependency amid labor shortages while also increasing material recovery. MRFs are increasingly seeing the benefit of using these technologies to recover more materials.
AI and robotics improve operational efficiency and reduce costs
MRF operations are highly complex. In the U.S., the average capacity of a MRF is now around 190 tons daily, nearly double the daily average capacity of a MRF in 2000, according to the Waste Business Journal’s latest directory of recycling facilities.
Even with the use of robots in the mix, there is still a significant number of materials that have to be sorted by human workers. Combined with long hours of standing and undesirable conditions, even the strongest of workers’ efficacy and efficiency declines over time, resulting in high rates of contamination and landfilled recyclables as well as a decrease in the overall accuracy of recyclables recovered.
Implementing AI-powered vision systems can vastly improve the accuracy, speed and efficacy of the detection and picking of recyclable materials done by robots. Such AI software, trained with datasets of hundreds of millions of real-world recyclable objects, can compute and identify items that should be picked by robotic cells with inference speeds as fast as 12 milliseconds and with greater than 95% accuracy. With real-time data analytics, AI solutions can also deliver actionable insights to empower MRFs to optimize their lines and ensure that efficacy does not degrade over time.
Furthermore, MRFs are labyrinths of conveyor belts, heavy equipment/machinery, sorting positions and walkways. And safety risks limit the number of belts humans can sort on. If the primary objective for sorters is to pick bottles, containers and aluminum cans one by one, then it is far more economical and safe to deploy AI and robotics to reduce human dependency and intervention.
While legacy sorting equipment and robotic systems are large and costly to deploy, there are modern robotics cells available in the market today that are cost-effective and designed with small footprints so that they can be installed virtually anywhere in a facility. They do not require facilities to be retrofitted, nor will the deployment cause downtime. As a result, MRFs can deploy AI and robotics over the weekend or off-shift and begin recovering up to two to four times more quality recyclables in a few days’ time.
Innovating with AI and robotics
No two recycling facilities are identical. So it is critical that operators collaborate with partners who best understand their needs and can deliver the right solutions tailored to their facility and operations. This ensures that a facility gets the best possible level of efficiency and efficacy from AI and robotics.
Bottom line, MRFs are the central gatekeepers to the circular economy. Ensuring that they innovate ahead of rising socioeconomic challenges is mission-critical because it can help MRFs overcome labor challenges and ensure continuity. As a result, they can simultaneously strengthen the circular economy and ensure the recovery of more valuable recyclables.
JD Ambati is the founder and CEO of EverestLabs, a rapid-growth Silicon Valley company using AI and robotics to decarbonize the packaged goods industry by automating recycling. Steeped in more than 20 years of experience, including a master’s degree in computer science and artificial intelligence (AI) and a bachelor’s degree in chemical engineering, Ambati’s background covers applications of AI to transform how systems can strengthen businesses’ operational efficiency.
The views and opinions expressed are those of the author and do not imply endorsement by Resource Recycling, Inc. If you have a subject you wish to cover in an op-ed, please send a short proposal to [email protected] for consideration.
A version of this story appeared in Resource Recycling on Jan. 23.