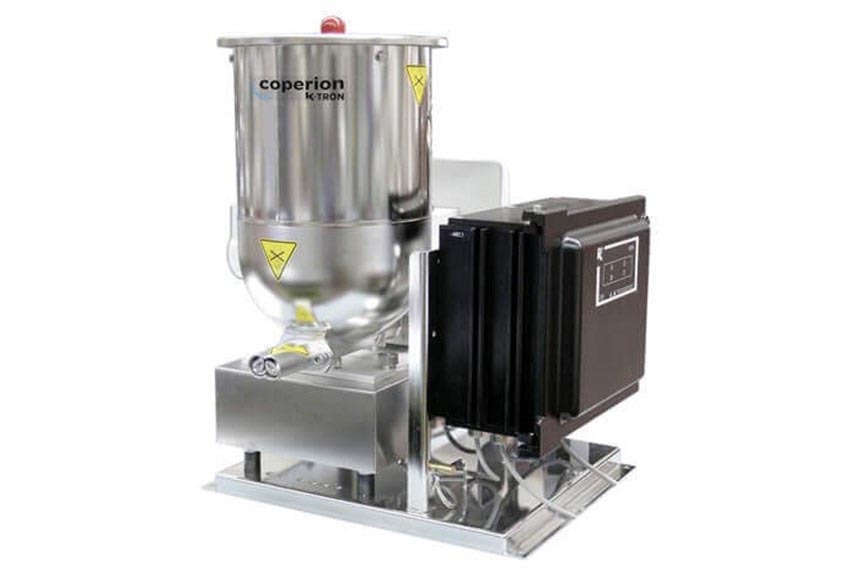
Coperion K-Tron’s feeder can be used for both loss-in-weight feeding to continuous processes and loss-in-weight batching direct to batch blenders. | Courtesy of Coperion K-Tron
The variability of recycled plastic streams doesn’t just present challenges in terms of extruding and molding products. It also complicates the feeding of plastic into compounding equipment.
In a recent presentation, John Winski, director of sales in the Americas for feeding equipment company Coperion K-Tron, discussed the different technologies for methodically moving recycled plastic from a hopper into processing equipment.
Getting this step in the recycling process right is important to ensuring operational efficiency, achieving recycled-content claims, and correctly dosing additives.
During the March 18 webinar, which was organized by trade publication Plastics Technology, Winski described how the variability of recycled plastics streams makes it hard to use a one-size-fits-all approach.
Recycled plastic can enter a hopper in wildly different forms – cubes, pellets, and fibers, for example. Characteristics such as particle shape, size, hardness, bulk density, moisture content, compressibility, cohesiveness and permeability can all affect how the material flows – or doesn’t.
“[Recycled plastics] are unique in themselves in that how they’re processed will really decide how we will handle them,” said Winski, who has 32 years of experience at Coperion K-Tron.
Feeder considerations
Feeders carry material from a hopper into the processing equipment.
When it comes to feeding material, Winski said, shredded bottle scrap is generally an easier material to handle – much less challenging than low-density fluff from post-consumer carpet, for example. But depending on the shredder that was used, the flake size can vary considerably, and that presents feeding challenges.
Winski suggested using a single-screw feeder with either an open flight screw or one with a closed-flight screw in a larger tube. Both approaches relieve pinch points that can restrict the flow of flakes from a storage bin above into the machine below.
“If we tried to feed this material in a twin-screw feeder with these concave screws, it would be a very poor choice, because the material would really get pinched into these screws and would lock the material up,” Winski said.
For regrind that’s a more consistent size, an option is to use a rotary valve feeder, where the material drops from the hopper down into a series of revolving pockets. In that case, it’s crucial to use a shear protector.
“If you don’t have a sheer protector, it’s like putting material into a twin-screw feeder and you’ll have a pinch point,” he said.
Preventing blockages in the hopper
Problems can also crop up in the hopper. Some materials, such as plastic chips, can become interlocked in the hopper, he said. When that happens, they can form what are called “ratholes,” where the material builds up along the lower sides of the hopper, constricting flow into the feeder bowl.
Another problem is the development of “bridges,” where the plastic interlocks and completely clogs the flow into the feeder.
To avoid those situations, Winski recommends the use of an agitator in the feeder bowl, which is located at the bottom of the hopper. That would ensure material in the hopper consistently drops down into the feeder. Additionally, some form of flow agitation in the extension hopper may be needed, he said.
Other options, each with pros and cons, include a vertical agitator in the hopper, flexible liners, air pads, or a bin vibrator.
Winski also said it’s important to consider volumetric versus gravimetric feeders, especially when a processor needs to ensure an accurate amount of material is feeding into equipment at consistent speeds.
The simplest is a volumetric unit, where a turning screw pulls recycled plastic out of the bottom of a hopper. The assumption is material will fall down the hopper and feed out at a fixed speed, Winski said. The accuracy is usually within 3% to 5%, although it can be worse if the material is more variable.
Gravimetric systems include load cells and a controller, which adjust the speed based on how much weight is being lost in the hopper. Most gravimetric systems note they can provide an accuracy to within 0.5%, but it still varies depending on the flowability and particle size of the material, Winski said. If the hopper is full of a heavy material with a large particle size, the accuracy may be within 1%, he said.
To receive the latest news and analysis about plastics recycling technologies, sign up now for our free monthly Plastics Recycling Update: Technology Edition e-newsletter.
More stories about technology
- RIT researchers develop AI-based textile recycling system
- Industry nuance is key in adopting emerging technology
- Google, Dow partner on AI to identify recyclables