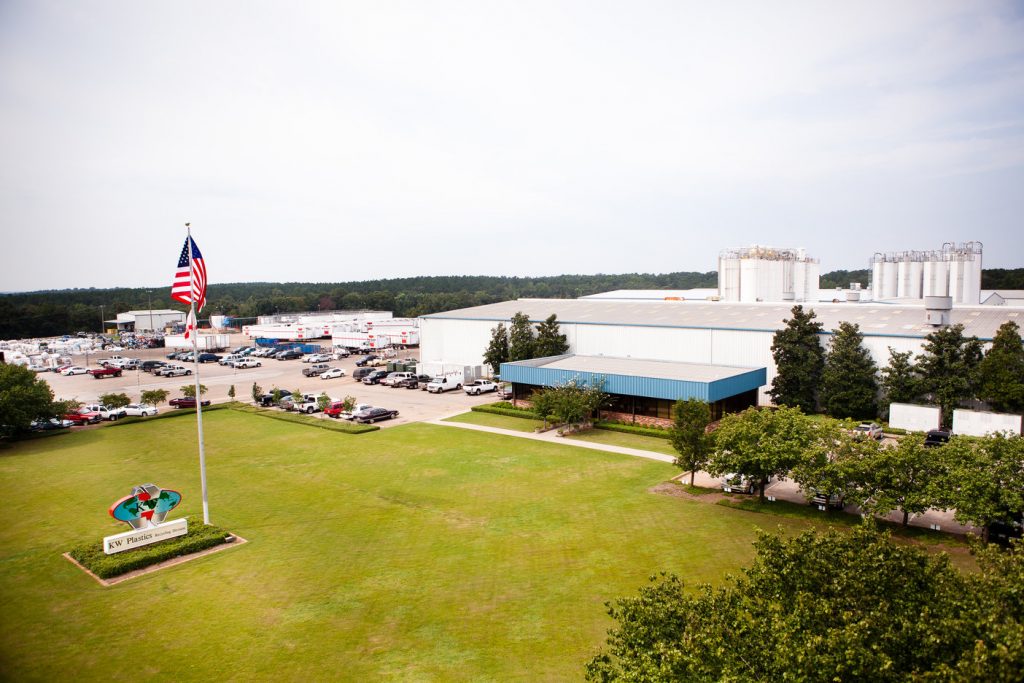
KW has converted several of its extrusion lines over to produce recycled natural HDPE to meet demand for packaging.
The coronavirus has disrupted end markets for KW Plastics, moving demand away from industrial applications and toward packaging for essential products.
Troy, Ala.-based KW Plastics, which describes itself as the world’s largest plastics recycling company, has 350 employees directly tied to plastics recycling. KW has not laid off any of those workers during the coronavirus pandemic, said Stephanie Baker, director of market development for KW Plastics.
Baker spoke on a recent webinar hosted by the Southeast Recycling Development Council (SERDC) and provided more details in an interview with Plastics Recycling Update.
“We’re doing everything we can to keep business as usual so that we can keep PCR flowing to our customers that need it,” Baker said.
But the company has seen fast changes in the numerous end markets it supplies.
The automotive sector has essentially shut down, and “we have seen that business come to all but an abrupt stop,” Baker said. Automotive manufacturers have floated plans to restart their plants in early May, but for the time being, that end market is closed.
At the same time, however, KW has seen demand increase for its natural HDPE recycled pellets. This resin goes into packaging for personal care products, household cleaning agents, detergents, soaps and more.
“We can’t keep that stuff on the shelves,” Baker said. KW anticipates shipping 9.5 million pounds of natural HDPE this month.
“That is a significant amount for us in that particular resin, but, overall, that is significantly lower than what we would ship throughout our whole product line,” Baker said.
KW has converted several of its extrusion lines over to natural HDPE to meet the demand, Baker said.
Meanwhile, the coronavirus has had impacts upstream, shifting the supply of recyclables that make up KW’s raw materials.
Some California MRFs that supply KW shut down recently, but the company continues to purchase bales from its other regular suppliers, Baker said. Still, the company is starting to see a slowdown in bales being produced, she added, not because of collection disruptions, but because MRFs are making internal adjustments to keep employees safe and prevent the spread of the virus, slowing down sorting and baling.
KW was fortunate to have a considerable amount of inventory as the pandemic began to take hold, and the company continues to buy as much material as it can, Baker said.
In a separate shift, KW has noted less activity as far as brand owners experimenting with recycled resin in new applications.
Baker said there has been a large uptick in brand owners making sustainability commitments in the past nine to 16 months, and those pledges have translated to more demand for using recycled plastic in innovative ways within product packaging.
But the coronavirus has shelved that work as companies prioritize responding to the current market.
“All of that has come to a stop right now as we are seeing our suppliers really scale back to producing the items, the products, that are essential right now,” Baker said. “They don’t have any room to introduce new products or new packaging right now.”
More stories about processors
- Major plastic initiative sets sights on system change
- California will fund mixed plastics facility, other projects
- E-plastics processor expands line of recycled board