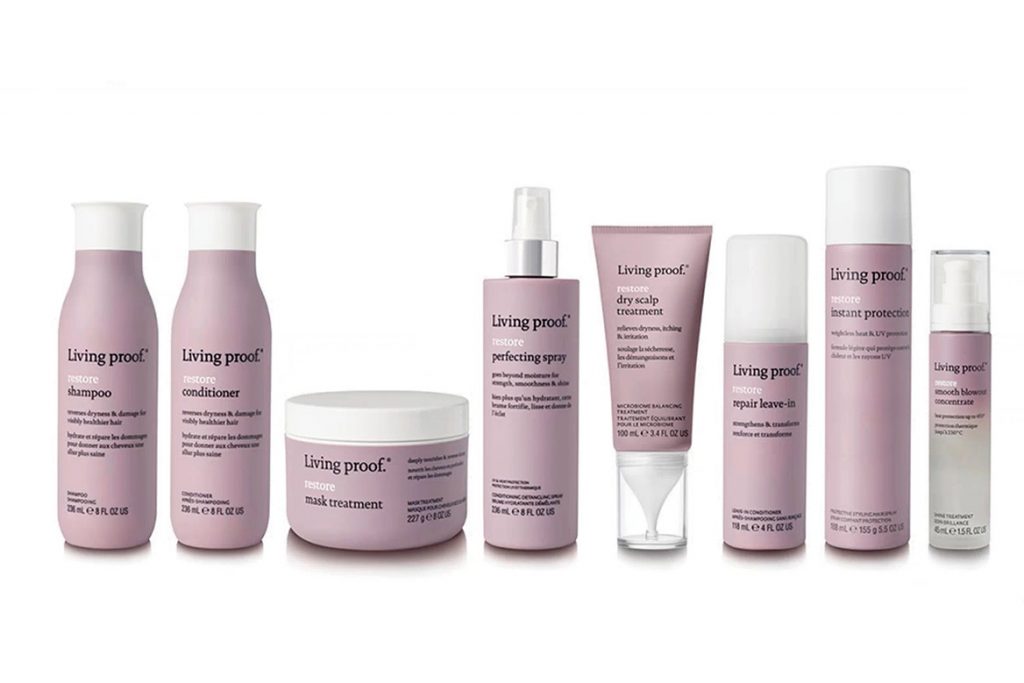
Living Proof recently tested the recyclability of some of the company’s hair care product packaging.
The Association of Plastic Recyclers recently recognized the recyclability of three packaging innovations: a 100% plastic aerosol bottle, a tube with an EVOH barrier, and an HDPE bottle with copolymer coating.
APR issued Procter & Gamble (P&G) a critical guidance letter for its new 100% polymer aerosol container on Dec. 17. Hair care brand Living Proof received a letter for its HDPE bottle with a copolymer coating on Dec. 10. And Albéa Group got an APR letter for its barrier-layer tube on Dec. 6.
In December, officials from all three companies participated in webinar to explain how their packaging passed recyclability testing.
(Disclosure: APR is the owner of Plastics Recycling Update publisher Resource Recycling, Inc.)
Elimination of metal parts
Jennifer Hosmer of P&G noted during the webinar that aerosol containers have long been made strictly of steel or aluminum. Plastic versions were developed more recently, but they have still incorporated a metal value crimped onto a plastic bottle. But the different materials aren’t easy to separate, she noted.
P&G developed a plastic version with a unique weld that provides a seal without the use of metal, Hosmer said. The bottle is made of PET, and the dip-tube assembly, valve and actuator are plastics with a polyolefin backbone, she said.
To test recyclability, P&G enlisted the help of independent R&D and testing company Plastics Forming Enterprises (PFE). The testing involved grinding, washing, elutriation, extrusion and injection molding, according to Hosmer’s presentation. PFE tested the weight and percentage of plastic that floated, the percentage that clumped, and the pellet and plaque intrinsic viscosity.
PFE also checked for black specks, haze and color in the molded plaque. All met APR’s requirements, she said.
Hosmer said P&G uses aerosol containers across five of its product lines: fabric care, home care, grooming, hair care and personal care products.
Barrier tube without aluminum
Tube producer Albéa Group redesigned its laminated tube to make a version that’s recyclable in the HDPE bottle stream. The tubes are used for oral care and cosmetics product packaging.
Gilles Swyngedauw, vice president of marketing, innovation and sustainability for the company, told webinar listeners the company shifted from aluminum barrier laminate (ABL) to plastic barrier laminate (PBL) in creating its Greenleaf tube. In PBL, EVOH is used to provide a barrier instead of a layer of aluminum foil.
Albéa Group developed a way to apply the EVOH in an extremely thin layer that maintains high oxygen and water vapor barrier properties, Swyngedauw said.
According to the presentation, Albéa Group has two different tube sleeve structures available: One with a single layer of EVOH, tie layers and PE layers, and a higher-barrier version with two EVOH layers, tie layers and PE layers. In the tube, the PE layers are usually HDPE or MDPE, and the tie layers are PE with 2% to 10% modification to the polymer chain to improve adhesion between EVOH and the PE, Swyngedauw said. He said the tie layers act as a compatibilizer between the EVOH and the PE layers during recycling.
During recyclability testing, which also took place at PFE, experts conducted trials on what was believed to be among the worst-case scenarios for recycling, he said: Albéa’s GL250IB tube with a low melt flow index shoulder. According to his presentation, the product has a melt flow index of 0.73, density of 0.974, EVOH content of 5.8% and tie layer of 4.4%. PFE shredded the plastic, washed it and extruded it, and the recycled pellets met APR’s expectations, he said.
Then, PFE used the pellets to mold bottles, which passed tests for bottle weight, capacity, dimensions, thickness, and “drop and crush,” he said.
Going forward, Albéa is working to replace the tube’s PP cap with a HDPE version starting in the second quarter of this year, he said. Albéa tested recycling of the tubes with the HDPE cap, and the recycled resin passed in all measures except for melt index, because of the high melt flow of the HDPE cap, he said.
Albéa is trying to see how it can improve that, Swyngedauw said.
Coated HDPE bottle
For a decade, Living Proof has been using an HDPE bottle with a “soft touch” coating for its hair care products, said Barbara Spakowski, vice president of packaging development at Living Proof. The coating, which makes up no more than 10% by weight of the container, is an ethylene/propylene copolymer. The bottle cap is PP.
During the webinar, Spakowski said the feel of the clear coating is an important part of the brand image. Living Proof also worked with PFE to test recyclability.
During the webinar, Kristi Hansen of PFE explained that they began with NIR optical sorter testing to ensure the packaging could be sorted correctly. Testing at optical sorter company MSS showed a capture rate of over 95% after five runs on an optical sorter that separates colored HDPE, Hansen said, adding that the sorter had not been modified ahead of time to recognize that particular package.
Then the plastic was ground, washed, extruded into pellets and injection-molded into a part, Hansen said. Using samples of 25% and 50% Living Proof bottle in them, PFE examined the pellets’ melt index, density, volatiles percentage, PP percentage, ash content, DSC and colors, and it measured screenpack pressure.
PFE then analyzed the melt index, flexural modulus, tensile yield, elongation at break and notched Izod impact strength of the molded part.
The bottle passed APR’s requirements in all areas, Hansen said.
To receive the latest news and analysis about plastics recycling technologies, sign up now for our free monthly Plastics Recycling Update: Technology Edition e-newsletter.