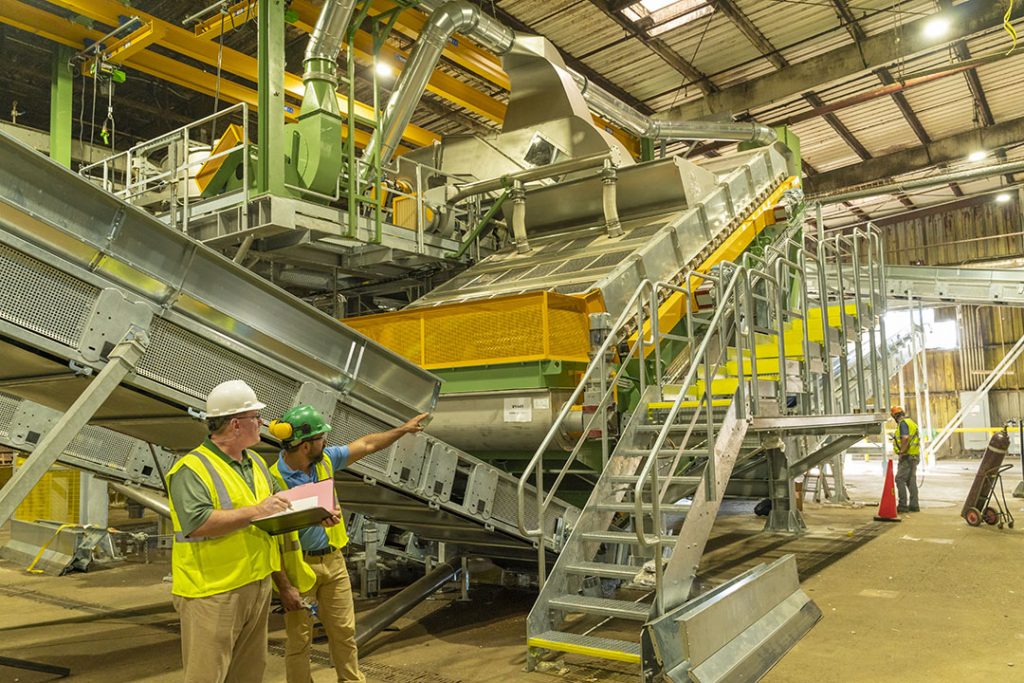
Clear Path Recycling installed a new wash trommel to remove contamination, including sleeve labels, from PET bottles. | Courtesy of Clear Path Recycling.
A $1 million-plus equipment investment is helping North Carolina-based Clear Path Recycling boost PET throughput while using less water and energy.
The Fayetteville, N.C. reclaimer this summer installed new pre-wash equipment to help the facility produce clean flake more efficiently. Clear Path is a joint venture between Shaw Industries Group, one of the world’s largest carpet manufacturers, and DAK Americas, one of the world’s largest integrated PET producers and the main producer of polyester staple fibers in the Western Hemisphere.
The PET flakes produced by the facility are used by Shaw to produce carpet fiber.
Before the upgrades, the pre-wash system had two slow-spinning trommels that used water, heat and steam to remove contaminants. But when it came to removing bottle labels, particularly full-body shrink-sleeve labels, the process wasn’t as efficient as it could have been, said Ricky Lane, director of public affairs, trade relations and corporate communications at DAK Americas.
Over the summer, the company replaced the two older trommels with a wash trommel that operates at higher speeds and uses less water, Lane said. The trommel also has pins to shred and help remove bottle labels. The equipment was provided by Sorema.
According to the North Carolina Department of Environmental Quality (NCDEQ), which provided a grant to Clear Path, the upgrade project also involved installing a conveyor belt and vibrating screen as part of a redesigned infeed system. Lane said NCDEQ’s $40,000 grant helped fund the conveying system, which was provided by Stadler.
Overall, the upgrades and renovations totaled over $1 million. They boosted the nearly 10-year-old facility’s capacity from about 90 million pounds per year to 95 million pounds per year.
“We have an increase in capacity and a more efficient process and less water and less energy,” Lane said.
The plant has a wet side and a dry side. The reduced water usage on the wet side means less overall moisture, which allows Clear Path “to extend the life cycle of a lot of pieces of critical equipment within our processes that were being impacted by a lot of the high moisture content.”
The biggest challenge with the project related to the building, which predates the plant’s installation. “And so now when we went to upgrade this facility, we had to work with some limited footprint opportunities and limited height of the structure with regard to the placement and layout of equipment,” Lane said.
More stories about processing