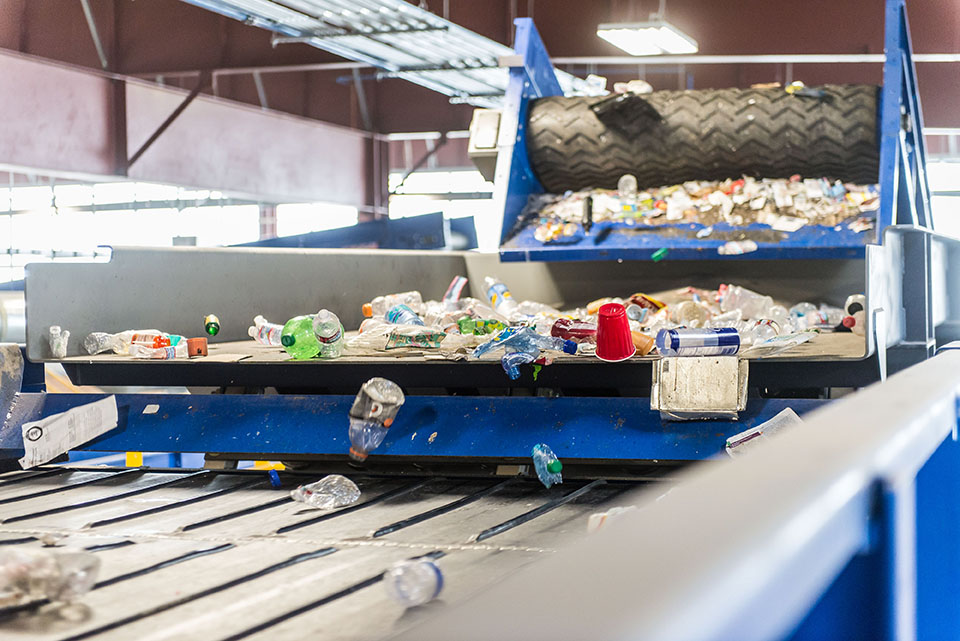
The Recycling Partnership has identified three key initiatives to improve the current recycling system.
PET collection is lagging behind recycled resin demand by more than 1 billion pounds per year, according to a study, and investment of $500 million is needed to improve the situation.
The Recycling Partnership this week released “The Bridge to Circularity: Putting The New Plastics Economy Into Practice In The U.S.” The report is premised on the concept that the current recycling system is insufficient, and The Recycling Partnership identifies key initiatives to move forward.
“Our current recycling system is fundamentally underfunded and incapable of delivering a circular economy without dramatic evolution,” said Keefe Harrison, CEO of The Recycling Partnership, in a release.
The report identifies three major findings that guide its recommendations for improvement:
- New types of packaging are coming onto the market faster than recycling infrastructure can keep up.
- The U.S. recycling system is unable to supply the amount of recycled material that brands need to meet the New Plastics Economy Global Commitment, as laid out by the Ellen MacArthur Foundation.
- Recycling stakeholders must look at building a more sustainable future recycling system that addresses the previously identified challenges.
To address these issues, The Recycling Partnership is planning the following:
- The organization will launch “Pathway to Recyclability,” a project aimed at “developing a clear roadmap for how to move a package from technically recyclable to commonly accepted for recycling.” This effort will feature a variety of meetings with stakeholders representing different material sectors beginning early next year.
- The Recycling Partnership will kick off “Unlocking Supply,” an “industry-wide, CEO-level” effort to raise $250 million over the next five years. This money would be put toward capturing more recyclables, particularly hundreds of millions of pounds of additional post-consumer plastic.
- The group will also begin a project called “Recycling 2.0,” which will call for another $250 million in investment over five years to “design and implement the future recycling system.” The project will develop a vision for what this system should look like and will come up with a “roadmap” for how to get there.
In addition to its major points, the report contains other key takeaways for plastics recycling stakeholders.
Address the supply and demand gap
The oft-cited shortfall of recycled resin to meet upcoming brand owner demand, particularly through the New Plastics Economy pledge, featured strongly in the report.
The group quantified an annual 1.1 billion pound gap between the supply of available RPET and the expected demand in the immediate future as brands pledge to use more recycled plastic. That figure comes from looking at recent annual PET bottle sales volumes and calculating how much RPET would be needed to hit 25% recycled content across all PET bottle sales in the U.S. However, the report points out that because of yield loss during processing, the needed supply of scrap PET would be about 1.6 billion pounds to generate the 1.1 billion pounds of PCR.
To bridge the gap, the group recommends a multi-pronged approach focused on boosting residential recycling infrastructure across the country. Extending some sort of recycling service to the 6% of households that don’t have it currently could bring in as much as 280 million additional pounds of PET per year, according to the report.
Meanwhile, getting residents with fee-based voluntary curbside recycling access to sign up and take full advantage of the service could bring in an additional 660 million pounds of PET per year. Introducing curbside access in areas with drop-off only would bring in even more PET.
“In all, lack of effective access to recycling services could amount to the loss of 2 billion pounds of PET per year, easily enough to close the 25% recycled content gap,” the report notes, acknowledging that that equation assumes all the collected PET would go to packaging.
The report focuses on collection improvement needs but also comments on processing infrastructure. Notably, although The Recycling Partnership notes that chemical recycling has been cited as a viable option for hard-to-recycle plastics, the report identifies mechanical recycling as the “only recycling process currently available at scale.” Therefore, the report recommends focusing on traditional recycling technologies in the short term and supporting chemical recycling as an option down the road as it commercializes.
Policy solutions?
Although the report is not focused on specific policy recommendations, it advises the industry search for “a new, and uniquely American, approach to the problem.”
The report advises “careful consideration and consultation” before selecting regulatory programs to improve recycling. For example, although bottle deposits are very effective at increasing recycling rates, The Recycling Partnership points out they also can take high-value materials out of the curbside stream. This can mean financial impacts on MRFs.
The organization also cautions that extended producer responsibility (EPR), which has been proposed for packaging in several U.S. states, can “take very different forms, and deliver very variable results.” And EPR isn’t a fix for everything, the group writes: Countries in Europe and elsewhere that have had packaging EPR for decades have not been insulated from the market impacts of China’s recovered plastics import ban.
Meanwhile, The Recycling Partnership brings up other tools, such as incentives, to improve the recycling system. To this end, the report discusses incentivizing recycled material use and design for recyclability, as well as adjusting landfill tipping fees to make recycling the more cost-effective option.
The report also likens the need for recycling funding to other major infrastructure challenges in the nation’s past, suggesting that taxpayer funding could be appropriated for recycling improvement.
More stories about collection
- Report shows $5B in materials saved from landfills
- NexTrex program boosts local film recovery efforts
- How MRFs develop their accepted material lists